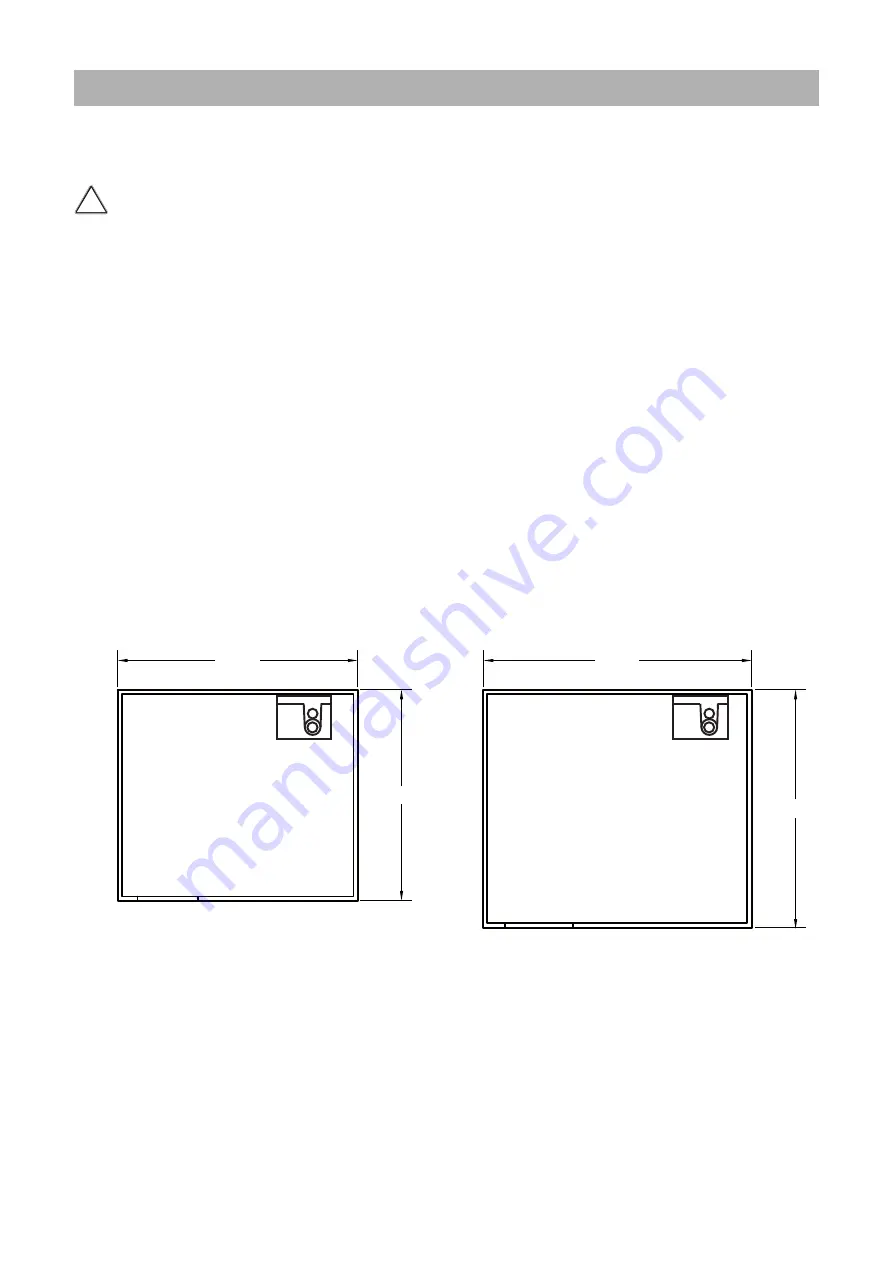
Installation & Servicing Instructions Rinnai E-Series
39
6.6.9 Room Air System (indoor combustion air)
When using indoor air, Rinnai strongly recommends the use of an indoor air
filter, P/N 808000025.
This boiler requires adequate combustion air for ventilation and dilution of flue
gases. Failure to provide adequate combustion air can result in unit failure, fire,
explosion, serious bodily injury or death. Use the following methods to ensure
adequate combustion air is available for correct and safe operation of this boiler.
Important: Combustion air must be free of corrosive chemicals. Do not provide
combustion air from corrosive environments. Appliance failure due to corrosive air is
not covered by the limited warranty.
Combustion air must be free of acid forming chemicals such as sulfur, fluorine and
chlorine. These chemicals have been found to cause rapid damage and decay and
can become toxic when used as combustion air in gas appliances. Such chemicals
can be found in, but not limited to bleach, ammonia, cat litter, aerosol sprays, cleaning
solvents, varnish, paint and air fresheners. Do not store these products or similar
products in the vicinity of this boiler.
Unconfined Space:
An unconfined space is defined in NFPA #54 "as a space whose volume is not less
than 50 cubic feet per 1000 Btu/hr (4.8 m3 per kW per hour) of the aggregate input
rating of all appliances installed in that space. Rooms communicating directly with
the space in which the appliances are installed, through openings not furnished with
doors, are considered a part of the unconfined space." If the “unconfined space”
containing the appliance(s) is in a building with tight construction, outside air may
still be required for proper operation. Outside air openings should be sized the same
as for a confined space.
Unconfined Space
91,300 BTU Boiler
Unconfined Space
200,000 BTU Boiler
25FT
NOTE: 8FT CEILING
25FT
36FT
NOTE: 8FT CEILING
36FT
Unconfined space
figure 19
!
WARNING