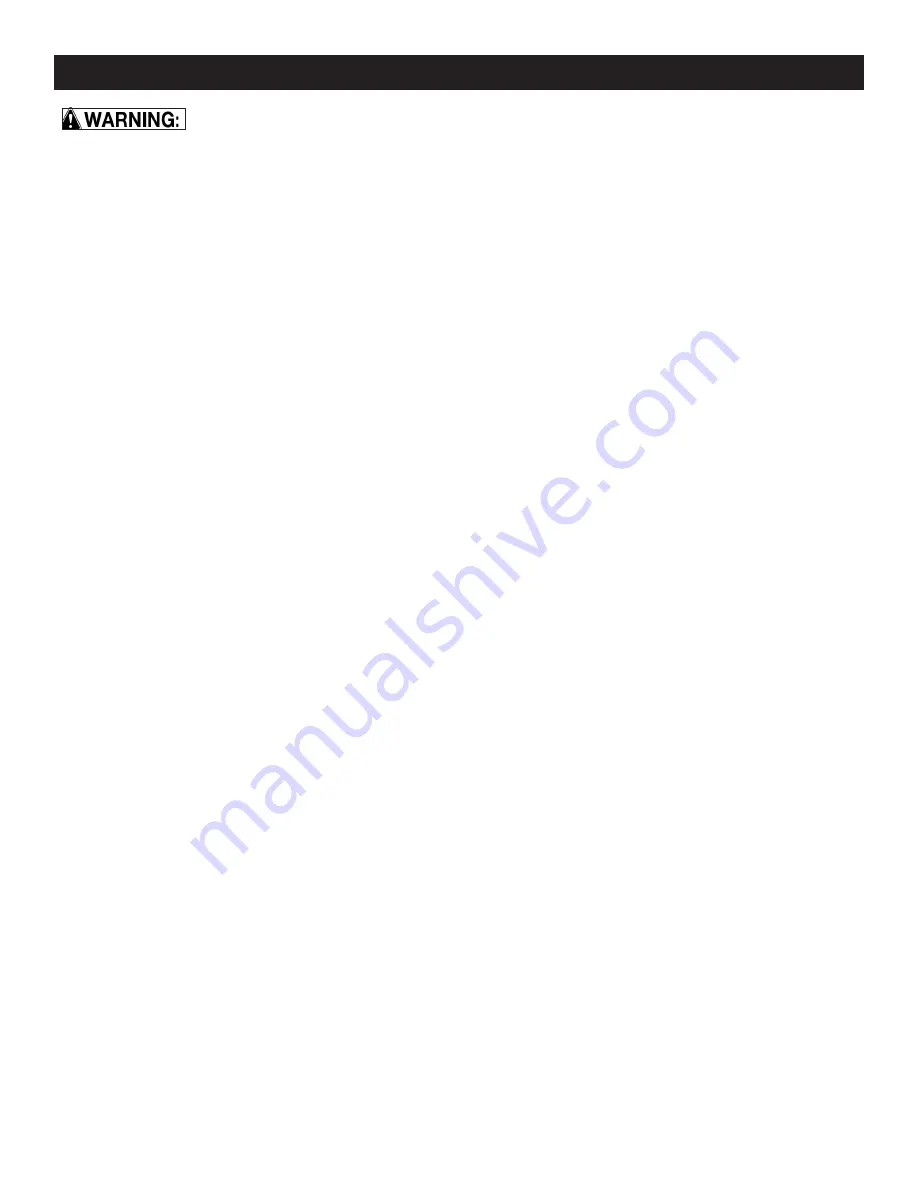
21
TROUBLESHOOTING
ADJUSTING THE UPPER GUIDE BEARINGS PARALLEL TO THE BLADE
The guide bearing assembly is factory pre-set. If adjustment is needed, follow the steps below.
Refer to “Guide Post Assembly” parts diagram on page 30.
1. Slightly loosen the four Hex Screws (#143) on right side of the upper bandsaw housing. This will
allow you to adjust the two Set Screws (#145) in the Support Plate (#146).
2. With the top door open, lower the Guide Post Assembly (#124) until you can access the two Set
Screws that are located at the top of the Support Plate.
3. Turning the front set screw clockwise will adjust the left bearings to the right.
Turning the rear set screw clockwise will adjust the right bearings to the left.
Check the bearings for parallel settings to the blade, and re-adjust as necessary.
4. Lastly, re-tighten the four Hex Screws on the housing. Repeat the steps if the bearings are still not
parallel.
ADJUSTING THE UPPER GUIDE BEARINGS TO TRACK CLOSE TO THE BLADE
If the upper guide bearings do not adjust to within 1/32” of the blade after the normal blade guide
adjustments are done (see page 14), then Guide Post (part #124) may need adjustment.
Refer to “Guide Post Assembly” parts diagram on page 30.
1. Lower the Guide Post (part #124) all the way to the table.
2.
Slightly loosen the four Hex Screws (#143) on right side of the upper bandsaw housing.
To further adjust the rear Thrust Bearing’s positon to the back of the blade;
3. Swing the whole Guide Post forward or back until the thrust bearing can be properly positioned.
To further adjust the Side Bearings alignment to the blade;
4. Adjust both of the two Set Screws (#145) that are located at the top of the Support Plate (#146).
Turning both set screws clockwise will list the Guide Post to the right.
Turning both set screws counter-clockwise will tilt the Guide Post a bit to the left.
Bearings must be properly spaced on each side of blade, and the blade will strike the center of the
rear thrust bearing.
5. Raise the Guide Post seven inches off the table and check alignment. If side guide bearings travel
out of alignment repeat steps above. Raise the Guide Post to the top of the travel and check final
alignment. Repeat steps above if necessary.
6. Re-tighten the four Hex Screws on the housing when the alignments are completed.
CHANGING BANDSAW TIRES
Use a putty knife to get underneath the tire and pull it up and away from the wheel. Work the putty
knife all the way around the wheel to loosen the tire. Then, use the putty knife as leverage to flip the
tire over and off of the wheel. Clean the inside of the groove, removing any dirt, debris or cement with
lacquer thinner.
Soak the replacement tire in warm water to make it more flexible. Dry the tire, and while it is still
warm, lay it on top of the wheel. Start by setting the tire into the wheel groove at the top of the wheel.
Using a putty knife, work the new tire around the wheel, making sure not to slice the tire. If rubber
cement is to be used as a binder, make sure to distribute it evenly. Having high spots between the
wheel and the tire will cause a vibration and effect blade tracking.
THE MACHINE MUST NOT BE PLUGGED IN AND THE POWER SWITCH MUST
BE IN THE OFF POSITION UNTIL ALL ADJUSTMENTS ARE COMPLETE.