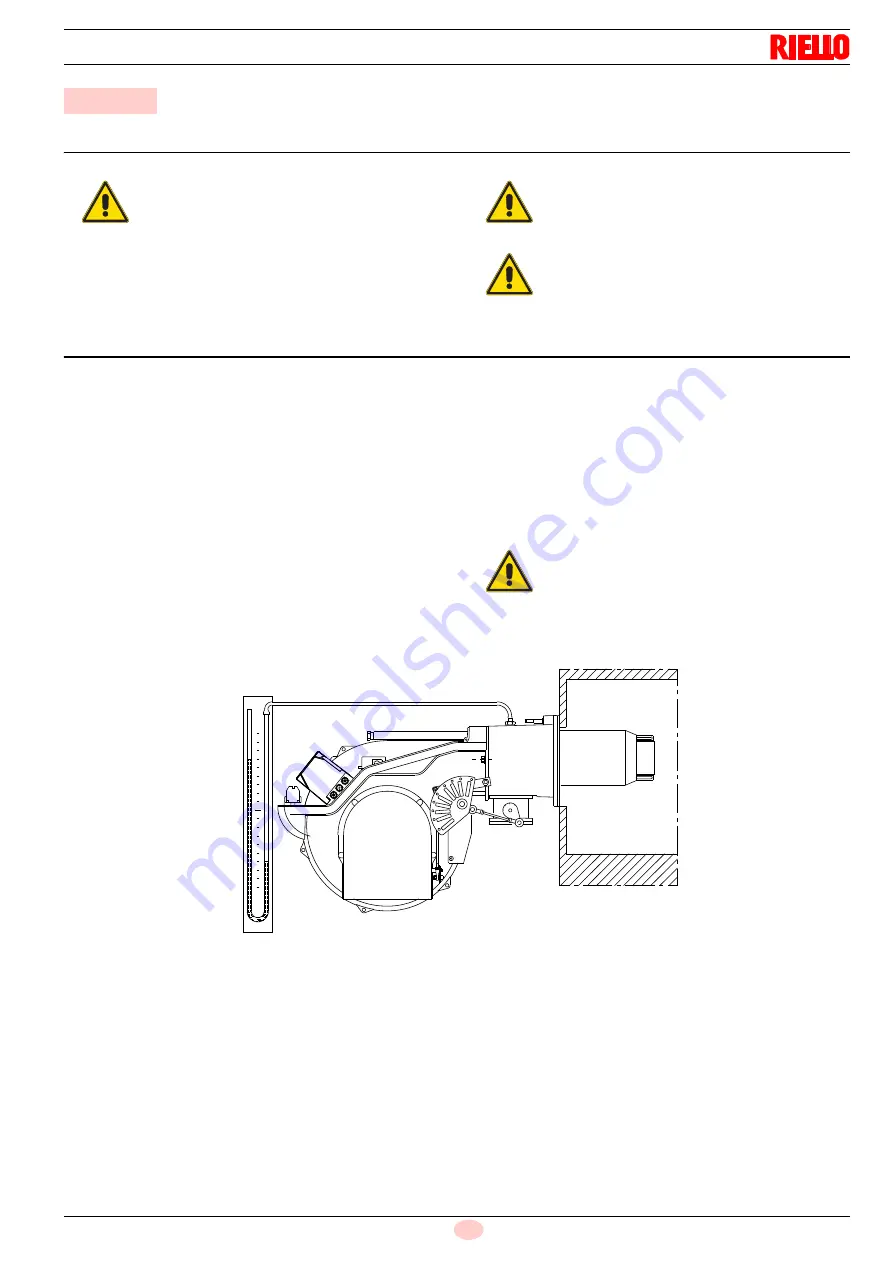
29
20152093
GB
Start-up, calibration and operation of the burner
6.1
Notes on safety for the first start-up
6.2
Adjustments prior to ignition
The following adjustments must be carried out:
ensure that the gas supply company has carried out the
supply line vent operations, eliminating air or inert gases
from the piping.
Slowly open the manual valves situated upstream from the
gas train.
Adjust the minimum gas pressure switch (Fig. 37 on
page 33) to the start of the scale.
Adjust the maximum gas pressure switch (Fig. 36 on
page 33) to the end of the scale.
Adjust the air pressure switch (Fig. 35 on page 33) to the
start of the scale.
Bleed the air from the piping of the gas train, connecting a
plastic tube to the pressure test point 1)(Fig. 29) of the
minimum gas pressure switch.
Take the vent tube outside the building so you can notice the
smell of gas.
Fit a U-type pressure gauge (Fig. 29) to the gas pressure
test point on the pipe coupling.
It is used to calculate approximate MAX burner output using
the Tab. L on page 24.
Connect two lamps or testers to the two gas line solenoid
valves to check the exact moment in which voltage is
supplied.
This operation is not required if each of the two solenoid
valves is equipped with a pilot light that signals voltage
passing through.
6
Start-up, calibration and operation of the burner
ATTENTION
The first start-up of the burner must be carried out
by qualified personnel, as indicated in this manual
and in compliance with the standards and
regulations of the laws in force.
ATTENTION
Check the correct working of the adjustment,
command and safety devices.
ATTENTION
Before starting up the burner, refer to section
“Safety test - with no gas supply” on page 35.
CAUTION
Before starting up the burner, it is good practice to
adjust the gas train so that ignition takes place in
conditions of maximum safety, i.e. with gas
delivery at the minimum.
Fig. 29
20155992
Summary of Contents for RS 200/M BLU
Page 2: ...Translation of the original instructions ...
Page 51: ...49 20152093 GB Appendix Electrical panel layout 0 ...
Page 55: ......