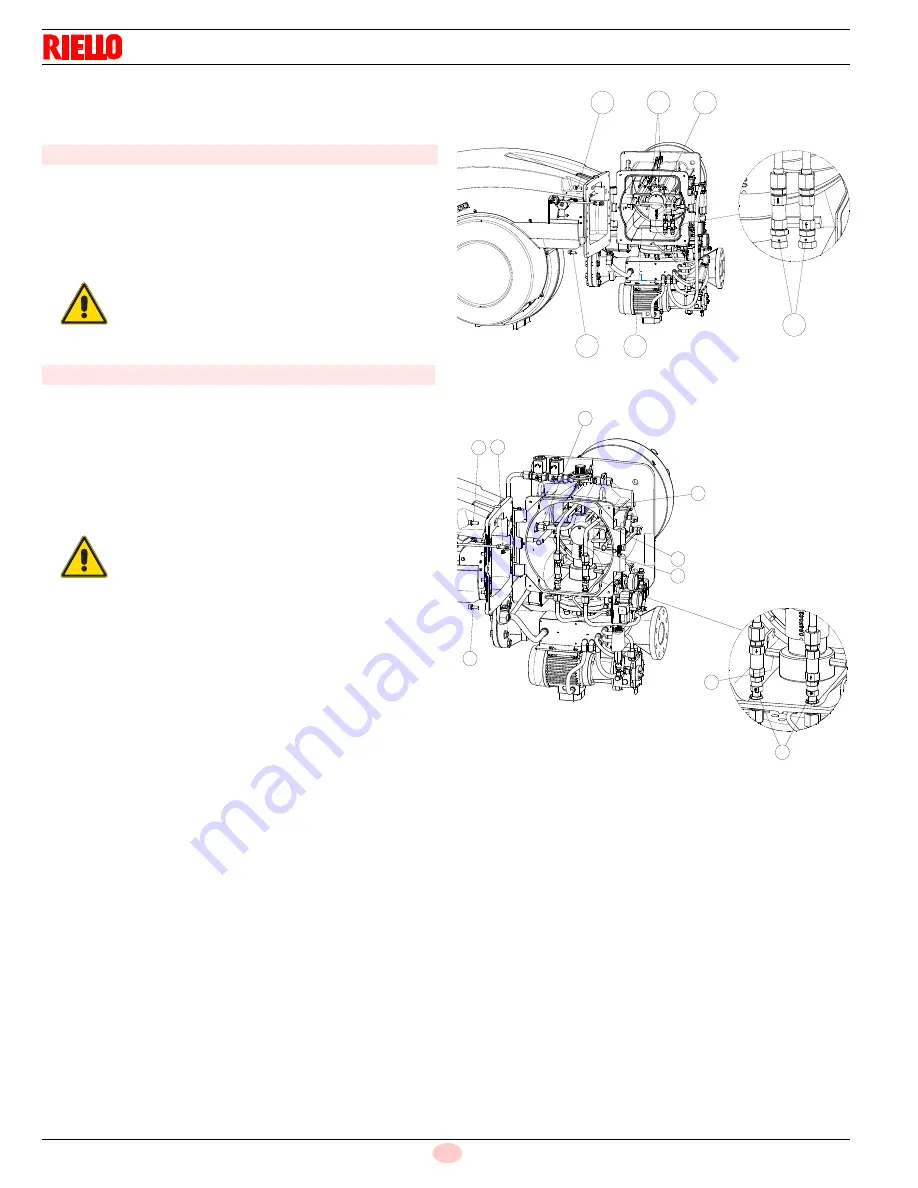
20036644
24
GB
Installation
4.7.3
Accessibility to the interior of the combustion
head
In order to reach inside the combustion head proceed as follows:
open burner at hinge (Fig. 14) after removing the 4 screws 1);
disconnect the wires 2) from the electrodes;
disconnect the oil pipes by unscrewing the two connectors 3);
unscrew the under part of the elbow 4) until it comes free of its
slot.
Extract the internal part 5) of the combustion head.
Disconnect the electrical wiring related to oil pump/servomo-
tor, air servomotor and gas pressure switch;
disconnect the leverages related to air damper and head
movement;
unscrew the 4 x fixing screws 1);
release the cable of the electrode 2);
disconnect the oil pipes by unscrewing the two
connectors 3).
Release the ignition pilot retainer;
remove the screw/gas pressure test point 6) of the combus-
tion head;
unscrew the under part of the elbow until it comes free of its
slot;
extract the internal part 5) of the combustion head.
RLS 300 - 400 - 500/E model (Fig. 14)
WARNING
While unscrewing, some fuel may leak out.
RLS 650 - 800/E model (Fig. 15)
WARNING
While unscrewing, some fuel may leak out.
Fig. 14
1
4
1
2
5
3
A
D3508
Fig. 15
1
2
2
3
4
7
5
8
6
D9424
Summary of Contents for RLS 300/E
Page 2: ......
Page 50: ...20036644 48 GB Appendix Spare parts A Appendix Spare parts ...
Page 57: ......
Page 58: ......
Page 59: ......