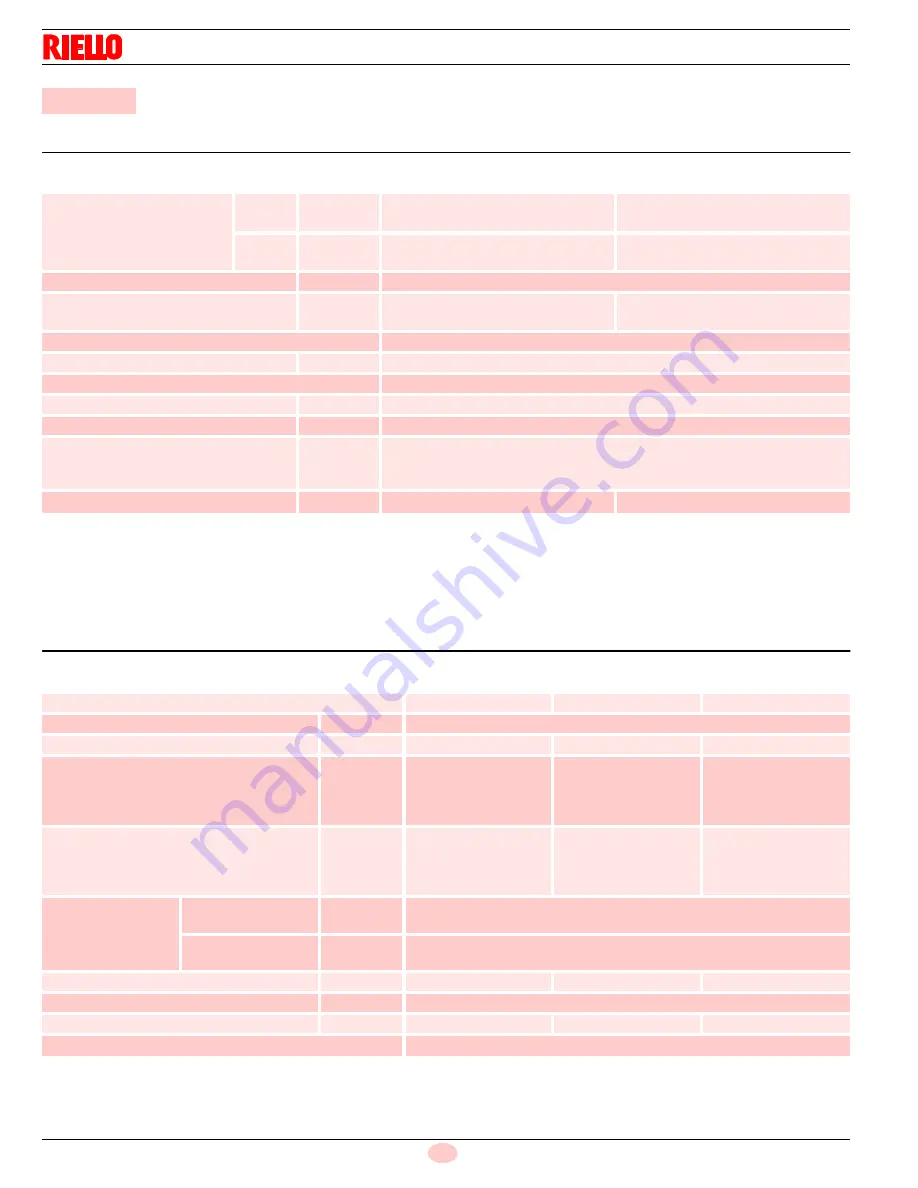
20095042
6
GB
Technical description of the burner
3.1
Technical data
Tab. A
(*)
Firing rate for C - UL Canadian Listing (CNL).
(1)
Reference conditions: Ambient temperature 68 °F (20°C) - Barometric pressure 394” WC - Altitude 329 ft.
(2)
Pressure at test point 18)(Fig. 6) with zero pressure in the combustion chamber and maximum burner output.
(3)
Sound pressure measured in manufacturer’s combustion laboratory, with burner operating on test boiler and at maximum rated output.
(4)
Equivalent Btu values based on 1 USGPH = 140,000 Btu/hr.
3.2
Electrical data
Tab. B
3
Technical description of the burner
Model
RLS 160/E
RLS 200/E
Output
(1)
Delivery
(1)
High
MBtu/hr
(4)
GPH
3542 - 7000 (6440*)
25.3 - 50 (46*)
5207 - 8870 (8055*)
37.2 - 63.3 (57.5*)
Low
MBtu/hr
(4)
GPH
1176
8.4
2100
15
Fuel
# 2 Fuel oil - Natural gas
Gas pressure at maximum delivery
(2)
Gas: Natural gas
“ WC
5.5
10.6
Operation
Modulating oil/gas
Nozzle
number
1
Standard applications
Boilers: water, steam, thermal oil
Ambient temperature
°F
32 - 104 (0 - 40 °C)
Combustion air temperature
°F max
140 (60 °C)
Pump
delivery (at 290 PSI)
pressure range
fuel temperature
GPH
PSI
° F max
146
102 - 580
302 (150 °C)
Noise levels
(3)
dB(A)
83.1
85
Model
RLS 160/E
RBNA Code
C9354400
C9354410
C9354401
Control circuit power supply
V/Ph/Hz
120/1/60
Main power supply (+/-10%)
V/Ph/Hz
230/3/60
460/3/60
575/3/60
Fan motor IE2/EPACT
rpm
HP
V
A
3500
7.5
230
17.8
3500
7.5
460
8.9
3500
7.5
575
7.1
Pump motor IE2/EPACT
rpm
HP
V
A
3530
1
230
3
3530
1
460
1.5
3530
1
575
1.2
Ignition transformer
Oil
V1 - V2
I1 - I2
120 V - 2 x 5 kV
2.7 A - 30 mA
Gas
V1 - V2
I1 - I2
120 V - 1 x 8 kV
1.6 A - 20 mA
Electrical power consumption
W max
7000
7000
7000
Electrical control circuit cons.
W
750
Total electrical consumption
W
7750
7750
7750
Electrical protection
NEMA 1
Summary of Contents for RLS 160/E
Page 2: ...Original instructions ...
Page 51: ......