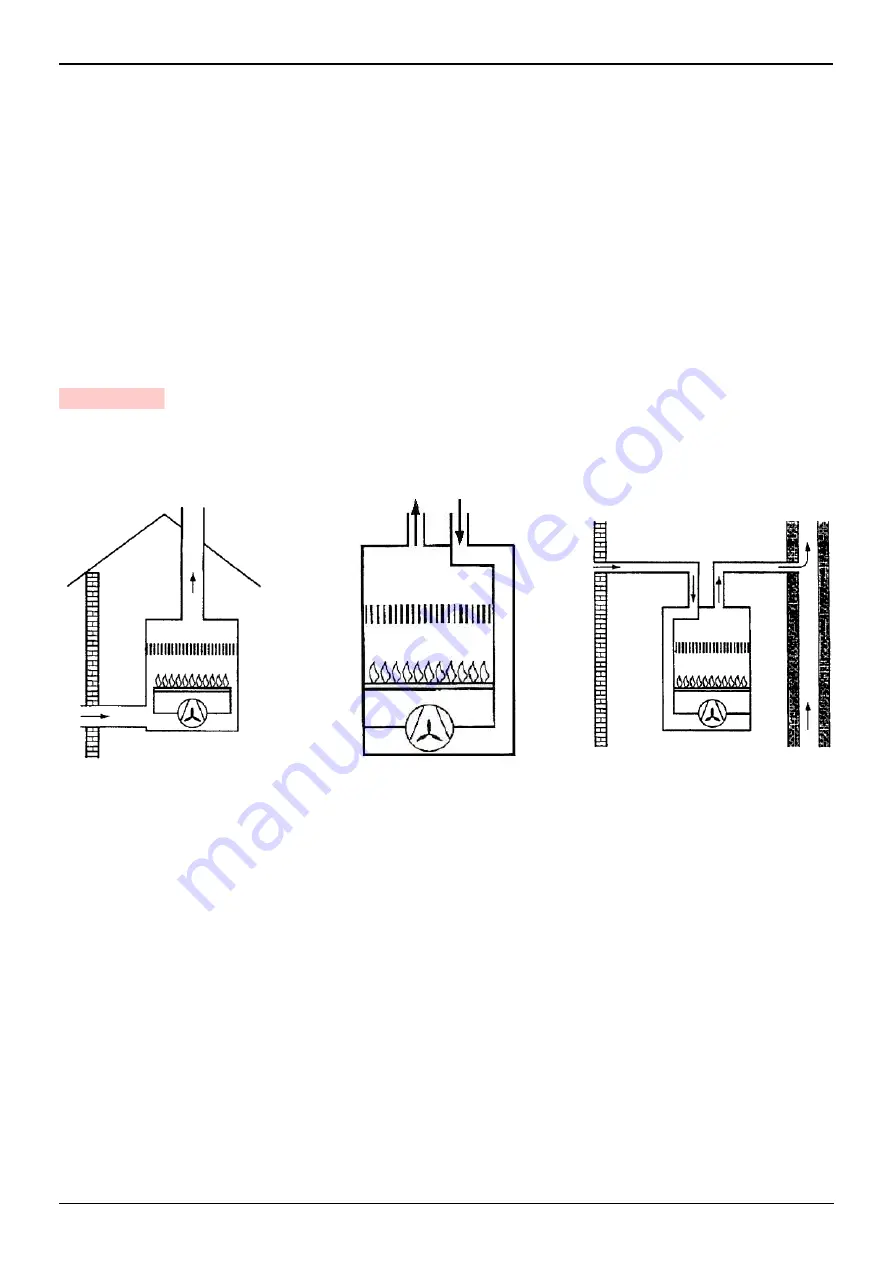
3445
6
➤
The intake-tube / burner system must not allow a loss of over 2 m
3
/h at 0.5mbar:
for instance, the above requirements will be met if you use flues for pressure exhaust of flue gases (the con-
densation kind).
➤
Make sure the air intake tube’s inlet is positioned so that it is not likely to be obstructed by foreign matter and,
where necessary, use suitable screens.
➤
The temperature of the incoming air must not exceed 40 °C;
➤
The inside diameter of the hose must be at least 80 mm.
➤
The intake tube can be up to 6 metres in length.
Warning: length is reduced if there are bends in the intake section.
For instance, using a tube with a smooth inside surface, you must allow for the following losses:
- for each 45° bend, tube length is reduced by 0.5 m;
- for each 90° bend, tube length is reduced by 0.8 m.
BURNER INSTALLATION MUST COMPLY WITH ONE OF THE INSTALLATIONS ILLUSTRATED IN THE
FIGURES BELOW.
➤
Under no circumstances should the air’s entry in the hose intake area be obstructed.
➤
The hose must not be blocked in any way or feature a shutting device (valves, membranes etc.).
➤
Coaxial tubes must not be installed for any reason.
ATTENTION
S7851
S7853
S7876