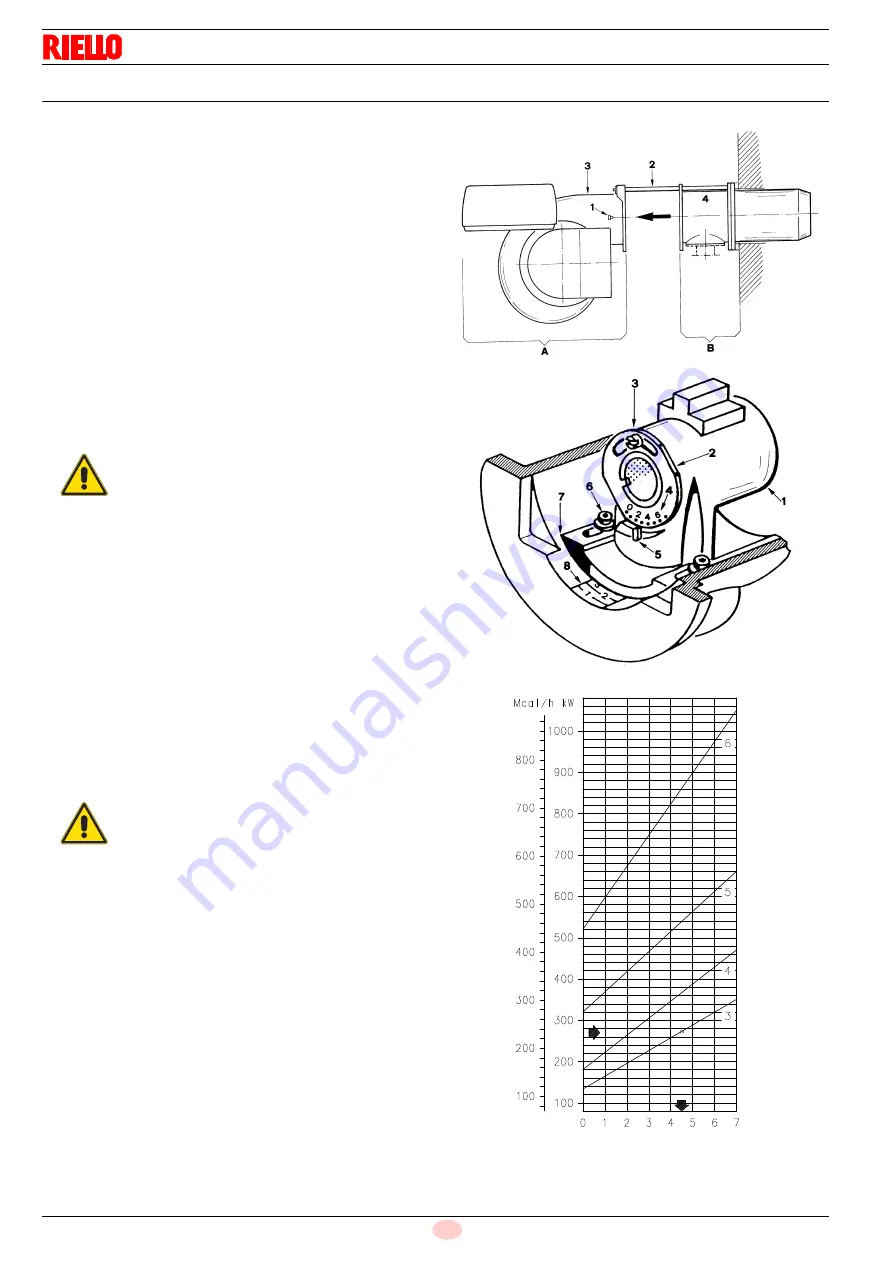
20144819
16
GB
Installation
5.7
Combustion head adjustment
The adjustment of the combustion head depends only on the
maximum output developed by the burner.
Therefore, this value must be set before adjusting the combus-
tion head.
Two adjustments of the head are envisaged:
for the gas and for the air. They are carried out with the burner
open (Fig. 11), when the burner is fixed to the boiler.
Gas adjustment
Turn the ring nut 2) so that the index 5) lines up with the
desired notch 4).
Tighten the screw 3) fully down.
Air adjustment
Loosen the two screws 6)(Fig. 12).
Move the elbow 1) forward or backward so that its rear sur-
face 7) lines up with the desired notch of the label 8).
Lock the screws 6).
Example:
The GAS 3 burner is installed in a 240 kW boiler. Considering an
efficiency of 89%, the burner should deliver about 270 kW.
The diagram (Fig. 13) shows that the gas and air adjustments for
this burner output are carried out on notch 4.5.
NOTE:
The diagram shows the ideal adjustment of the head. If the
pressure in the gas supply network is low and does not allow
the desired pressure (and therefore output) to be reached, it
is possible to further open the ring nut 2)(Fig. 12) by 1-2
notches. See also the note on page 18.
Finally close the burner:
-
Slide unit A on the two slide bars 2)(Fig. 11).
-
Put back the screws 1).
WARNING
The notch number for gas and air is the same and
is gained from the diagram (Fig. 13) in accordance
with the burner output.
WARNING
When the burner is closing on the two slide bars,
the high voltage cable and the flame detection
probe cable should be pulled outwards until they
are slightly taut.
Fig. 11
D202
Fig. 12
D118
Fig. 13
D227
GAS
Notches on the ring nut 2)(Fig. 12)
and on the label 8)(Fig. 12)
Summary of Contents for GAS 3
Page 2: ...Translation of the original instructions...
Page 37: ...35 20144819 GB Appendix Electrical panel layout GAS 3 4 SINGLE PHASE D2855 DIAGRAM A...
Page 38: ...20144819 36 GB Appendix Electrical panel layout GAS 5 6 THREE PHASE D2861 DIAGRAM A...
Page 39: ...37 20144819 GB Appendix Electrical panel layout 20144739 GAS 3 4 SINGLE PHASE DIAGRAM B...
Page 40: ...20144819 38 GB Appendix Electrical panel layout DIAGRAM B GAS 5 6 THREE PHASE 20144741...
Page 41: ...39 20144819 GB Appendix Electrical panel layout GAS 3 4 SINGLE PHASE DIAGRAM C 20144742...
Page 42: ...20144819 40 GB Appendix Electrical panel layout DIAGRAM C GAS 5 6 THREE PHASE 20144743...