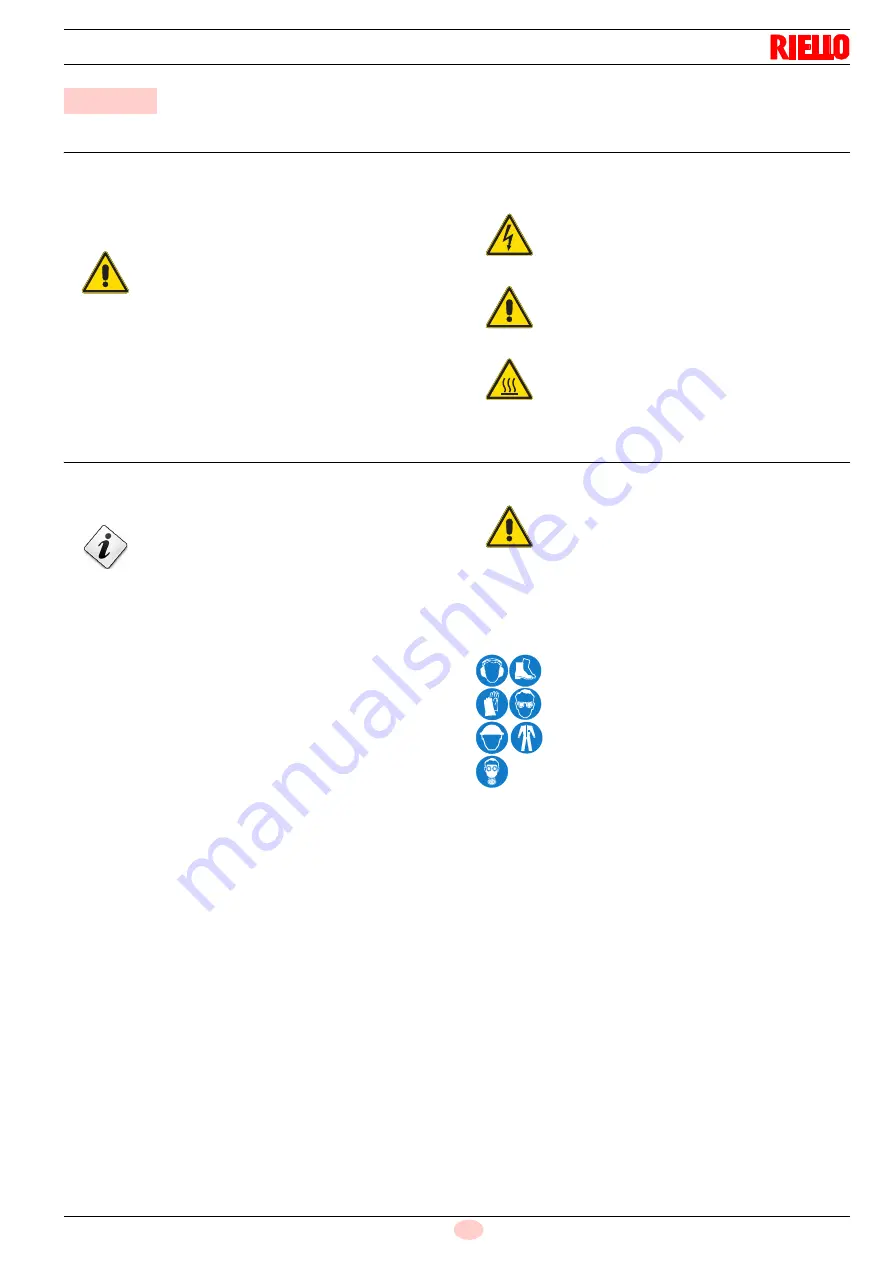
27
20144819
GB
Maintenance
7.1
Notes on safety for the maintenance
The periodic maintenance is essential for the good operation,
safety, yield and duration of the burner.
It allows you to reduce consumption and polluting emissions and
to keep the product in a reliable state over time.
Before carrying out any maintenance, cleaning or checking oper-
ations:
7.2
Maintenance programme
7.2.1
Maintenance frequency
7.2.2
Safety test - with gas supply closed
For a safe start up it is very important to check that the electrical
wiring between the gas valves and the burner has been carried
out correctly.
To this end, after checking that the wiring has been carried out in
conformity with the burner's wiring diagrams, a starting cycle
must be carried out with the gas tap closed (dry test).
1
The manual gas valve should be closed with the locking/re-
leasing device ("lock-out / tag out" procedure).
2
Make sure the limit electric contacts of the burner close
3
Make sure that the minimum gas pressure switch contact
closes
4
Proceed with a burner start up attempt.
The starting cycle should take place with the following phases:
-
Starting of the fan motor for the pre-purging
-
Control of the gas valve leak detection, if applicable.
-
Completion of the pre-purging
-
Attainment of the ignition point
-
Power supply to the ignition transformer
-
Power supply to the gas valves.
Since the gas is closed, the burner will not be able to start and its
control box will stop or safely lockout.
The effective powering of the gas valves can be verified with the
insertion of a tester; some valves have indicator lights (or open-
ing/closing position indicators) that are activated when they are
powered.
7.2.3
Checking and cleaning
Burner
Check that there are not excess wear or loosen screws. The
screws securing the electrical leads in the burner plugs should
also be fully tightened.
Clean the outside of the burner.
Clean and grease the adjustable profile of the cams.
Fan
Check to make sure that no dust has accumulated inside the fan
or on its impellers, as this condition will cause a reduction in the
air flow rate and provoke polluting combustion.
Boiler
Clean the boiler as indicated in its accompanying instructions in
order to maintain all the original combustion characteristics in-
tact, especially: the flue gas temperature and combustion cham-
ber pressure.
Gas leaks
Make sure that there are no gas leaks on the pipe between the
gas meter and the burner.
Gas filter
Change the gas filter when it is dirty.
7
Maintenance
DANGER
The maintenance interventions and the calibration
of the burner must only be carried out by qualified,
authorised personnel, in accordance with the con-
tents of this manual and in compliance with the
standards and regulations of current laws.
DANGER
Disconnect the electrical supply from the burner
by means of the main system switch.
DANGER
Close the fuel interception tap.
Wait for the components in contact with heat
sources to cool down completely.
The gas combustion system should be checked at
least once a year by a representative of the man-
ufacturer or another specialised technician.
WARNING
IF THE ELECTRICAL SUPPLY TO THE GAS
VALVES OCCURS AT UNEXPECTED TIMES,
DO NOT OPEN THE MANUAL VALVE, DISA-
BLE THE ELECTRICAL SUPPLY, CHECK THE
WIRING; CORRECT THE ERRORS AND CAR-
RY OUT THE ENTIRE TEST AGAIN.
The operator must use the required equipment
during maintenance.
Summary of Contents for GAS 3
Page 2: ...Translation of the original instructions...
Page 37: ...35 20144819 GB Appendix Electrical panel layout GAS 3 4 SINGLE PHASE D2855 DIAGRAM A...
Page 38: ...20144819 36 GB Appendix Electrical panel layout GAS 5 6 THREE PHASE D2861 DIAGRAM A...
Page 39: ...37 20144819 GB Appendix Electrical panel layout 20144739 GAS 3 4 SINGLE PHASE DIAGRAM B...
Page 40: ...20144819 38 GB Appendix Electrical panel layout DIAGRAM B GAS 5 6 THREE PHASE 20144741...
Page 41: ...39 20144819 GB Appendix Electrical panel layout GAS 3 4 SINGLE PHASE DIAGRAM C 20144742...
Page 42: ...20144819 40 GB Appendix Electrical panel layout DIAGRAM C GAS 5 6 THREE PHASE 20144743...