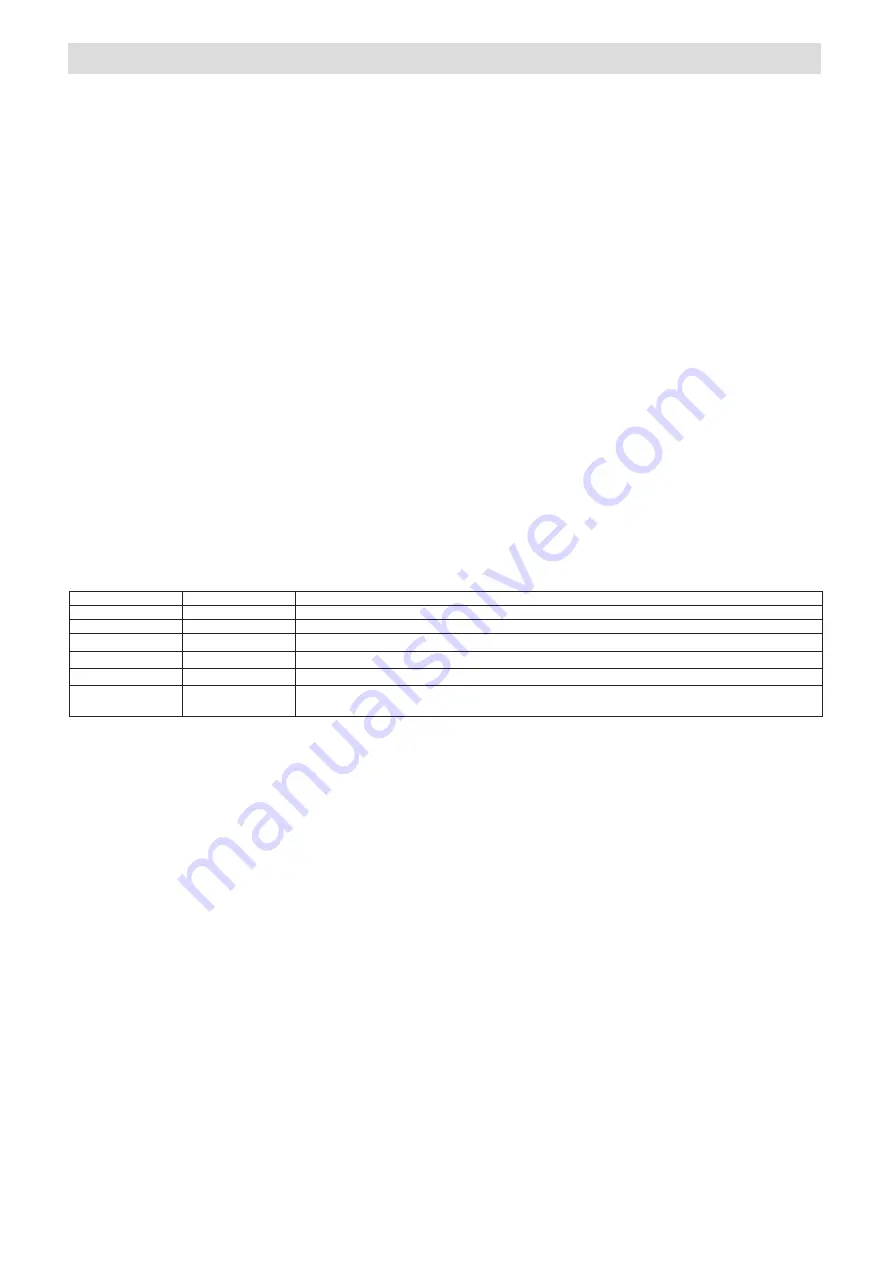
16
3 GENERAL REQUIREMENTS (UK)
This appliance must be installed by a competent person in ac-
cordance with the Gas Safety (Installation & Use) Regulations.
3.1 RELATED DOCUMENTS
The installation of this boiler must be in accordance with the
relevant requirements of the Gas Safety (Installation & Use)
Regulations, the local building regulations, the current I.E.E.
wiring regulations, the bylaws of the local water authority, the
Building Standards (Scotland) Regulation and Building Stand-
ards (Northern Ireland) Regulations.
It should be in accordance also with any relevant requirements
of the local authority and the relevant recommendations of the
following British Standard Codes of Practice.
ATTENTION
The use of PPE (Personal Protective Equipment) such as but
not limited to gloves, mask, safety glasses, etc. is strongly
recommended whenever carrying out the installation, repair,
or maintenance of this appliance – please pay particular at-
tention to:
• Sharp edges that may be encountered when:- handling or
lifting the appliance, removing parts, etc. during installation
and maintenance
• Airborne particles that may be released and/or disturbed
when cleaning or removing components during
maintenance
• Water treatment chemicals that could have been added to
the system water may spill from the appliance and or com-
ponents during maintenance
Please refer to an appropriate Health and Safety document
such as HSE L23 (UK) or S.I. 299 (Ireland), for more detailed
advice on safe working practices and procedures.
If the gas supply serves more than one appliance, it must be
ensured that an adequate supply is maintained to each appli-
ance when they are in use at the same time.
NOTE
It is recognised that ‘pressure loss’ through the gas cock and
gas valve may result in a pressure drop of approximately 2mbar
between the gas meter and gas valve inlet test point; this will
not impair the performance of the appliance, provided that a
dynamic pressure of 18mbar is available at the appliance inlet.
3.4 FLUE SYSTEM
The terminal should be located where the dispersal of combustion
products is not impeded and with due regard for the damage
and discoloration that may occur to building products located
nearby. The terminal must not be located in a place where it
is likely to cause a nuisance (see Fig. 9). In cold and/or humid
weather, water vapour will condense on leaving the terminal;
the effect of such pluming must be considered.
If installed less than 2m above a pavement or platform to
which people have access (including balconies or flat roofs)
the terminal must be protected by a guard of durable material.
The guard must be fitted centrally over the terminal. Refer to
BS 5440 Part 1, when the terminal is 0.5 metres (or less) below
plastic guttering or 1 metre (or less) below painted eaves.
3.5 AIR SUPPLY
The following notes are intended for general guidance only.
This appliance is a room-sealed, fan-flued boiler, consequently
it does not require a permanent air vent for combustion air sup-
ply. When installed in a cupboard or compartment, ventilation
for cooling purposes is also not required.
3.6 WATER CIRCULATION
Detailed recommendations are given in BS 5449 Part 1 and
BS 6798. The following notes are for general guidance only.
3.6.1 PIPEWORK
It is recommended that copper tubing to BS 2871 Part 1 is used
in conjunction with soldered capillary joints. Where possible
pipes should have a gradient to ensure air is carried naturally to
air release points and that water flows naturally to drain cocks.
Except where providing useful heat, pipes should be insulated
to avoid heat loss and in particular to avoid the possibility of
freezing. Particular attention should be paid to pipes passing
through ventilated areas such as under floors, loft space and
void areas.
3.6.2 AUTOMATIC BY-PASS
The appliance has a built-in automatic by-pass, consequently
there is no requirement for an external by-pass, however the
design of the system should be such that it prevents boiler
‘cycling’.
3.6.3 DRAIN COCKS
These must be located in accessible positions to facilitate
draining of the appliance and all water pipes connected to the
appliance. The drain cocks must be manufactured in accord-
ance with BS 2879.
3.6.4 AIR RELEASE POINTS
These must be positioned at the highest points in the system
where air is likely to be trapped. They should be used to expel
trapped air and allow complete filling of the system.
3.2 LOCATION OF APPLIANCE
The appliance may be installed in any room or internal space,
although particular attention is drawn to the requirements
of the current I.E.E. wiring regulations, and in Scotland, the
electrical provisions of the Building Regulations, with respect
to the installation of the appliance in a room or internal space
containing a bath or shower.
When an appliance is installed in a room or internal space
containing a bath or shower, the appliance or any control per-
taining to it must not be within reach of a person using the bath
or shower. The location chosen for the appliance must permit
the provision of a safe and satisfactory flue and termination.
The location must also permit an adequate air supply for com-
bustion purposes and an adequate space for servicing and air
circulation around the appliance. Where the installation of the
appliance will be in an unusual location special procedures may
be necessary, BS 6798 gives detailed guidance on this aspect.
A compartment used to enclose the appliance must be designed
and constructed specifically for this purpose. An existing com
-
partment/cupboard may be utilised provided that it is modified
to suit. Details of essential features of compartment/cupboard
design including airing cupboard installations are given in BS
6798. This appliance is not suitable for external installation.
3.3 GAS SUPPLY
The gas meter – as supplied by the gas supplier – must be
checked to ensure that it is of adequate size to deal with the
maximum rated input of all the appliances that it serves. Instal-
lation pipes must be fitted in accordance with BS 6891.
Pipe work from the meter to the appliance must be of adequate
size. Pipes of a smaller size than the appliance gas inlet con-
nection must not be used. The installation must be tested for
tightness in accordance with BS6891.
BS 5440
PART 1
FLUES
BS 5440
PART 2
FLUES & VENTILATION
BS 5449
PART 1
FORCED CIRCULATION HOT WATER SYSTEMS
BS 5546
INSTALLATION OF GAS HOT WATER SUPPLIES FOR DOMESTIC PURPOSES
BS 6798
INSTALLATION OF BOILERS OF RATED INPUT NOT EXCEEDING 60kW
BS 6891
LOW PRESSURE INSTALLATION PIPES
BS 7074
PART 1
APPLICATION, SELECTION, AND INSTALLTION OF EXPANSION VESSELS AND
ANCILLARY EQUIPMENT FOR SEALED WATER SYSTEMS