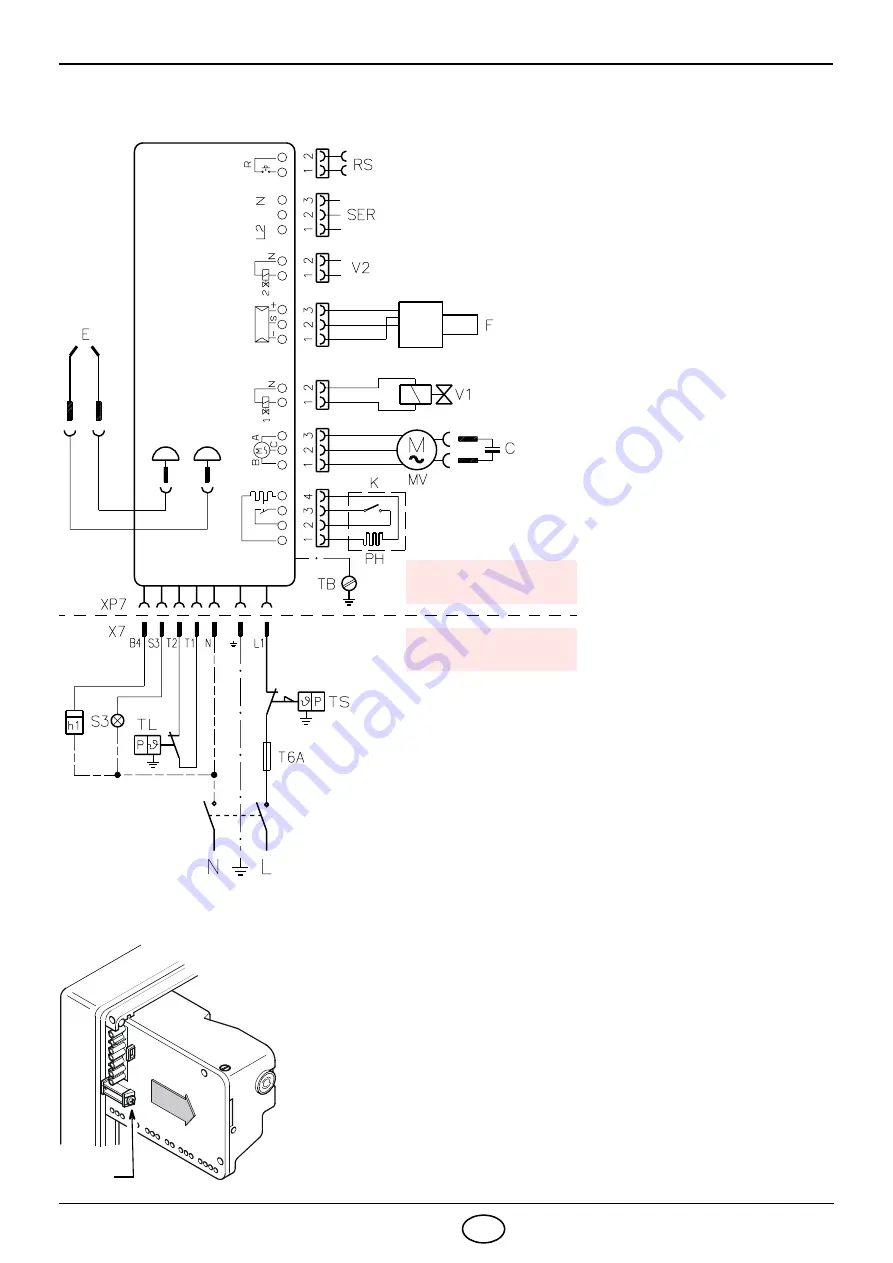
3330
6
GB
3.4
ELECTRICAL WIRING
ATTENTION:
³
Do not swap neutral and phase over, follow the diagram
shown carefully and carry out a good earth connection.
³
The section of the conductors must be at least 1mm².
(Unless
requested otherwise by local standards and legislation).
³
The electrical wiring carried out by the installer must be in
compliance with the rules in force in the country.
CONTROL BOX,
(see fig. 10)
To remove the control box from the burner it is necessary to:
³
Disconnect all the connectors, the 7-pin plug, the high voltage ca-
bles and the earth wire (
TB
);
³
Unscrew the bolt (
A
) and pull the control box in the direction of the
arrow.
To install the control box it is necessary to.
To install the control box it is necessary to:
³
Screw the bolt (
A
) in at a torque of 1 - 1.2 Nm;
³
Reconnect all the connectors previously disconnected.
NOTES:
The burners have been type-approved for intermittent operation.
This means they must stop at least once every 24 hours in order to al-
low the electrical control box to check its efficiency on start-up.
The boiler limit thermostat (
TL
) normally ensures the burner halts. If
this does not happen a time switch halting the burner at least once
every 24 hours must be applied in series to (
TL
).
A
E9275
LAY-OUT
C
– Capacitor
E
– Electrode
F
– Photoresistance
h1
– Hour counter
K
– Thermostat enabling start-
up after preheating
MV
– Motor
PH
– Oil heater
RS
– Remote reset
SER
– Safety lockout device
S3
– Lock-out signal
T6A
– Fuse
TB
– Burner-earth
TL
– Limit thermostat
TS
– Safety thermostat
V1
– Oil valve
V2
– Safety lockout device
X7
– 7 pin plug
XP7
– 7 pole socket
TO BE DONE BY
THE INSTALLER
CARRIED-OUT
IN THE FACTORY
TESTING
³
Check the burner has stopped by
opening the thermostats.
³
Make sure the operating burner locks
out by covering the
photoresistance
.
CONTROL BOX
MO550
D7240
Main switch
230V ~ 50Hz
Fig. 10
Black
Blue
Brown
Black
White
Blue