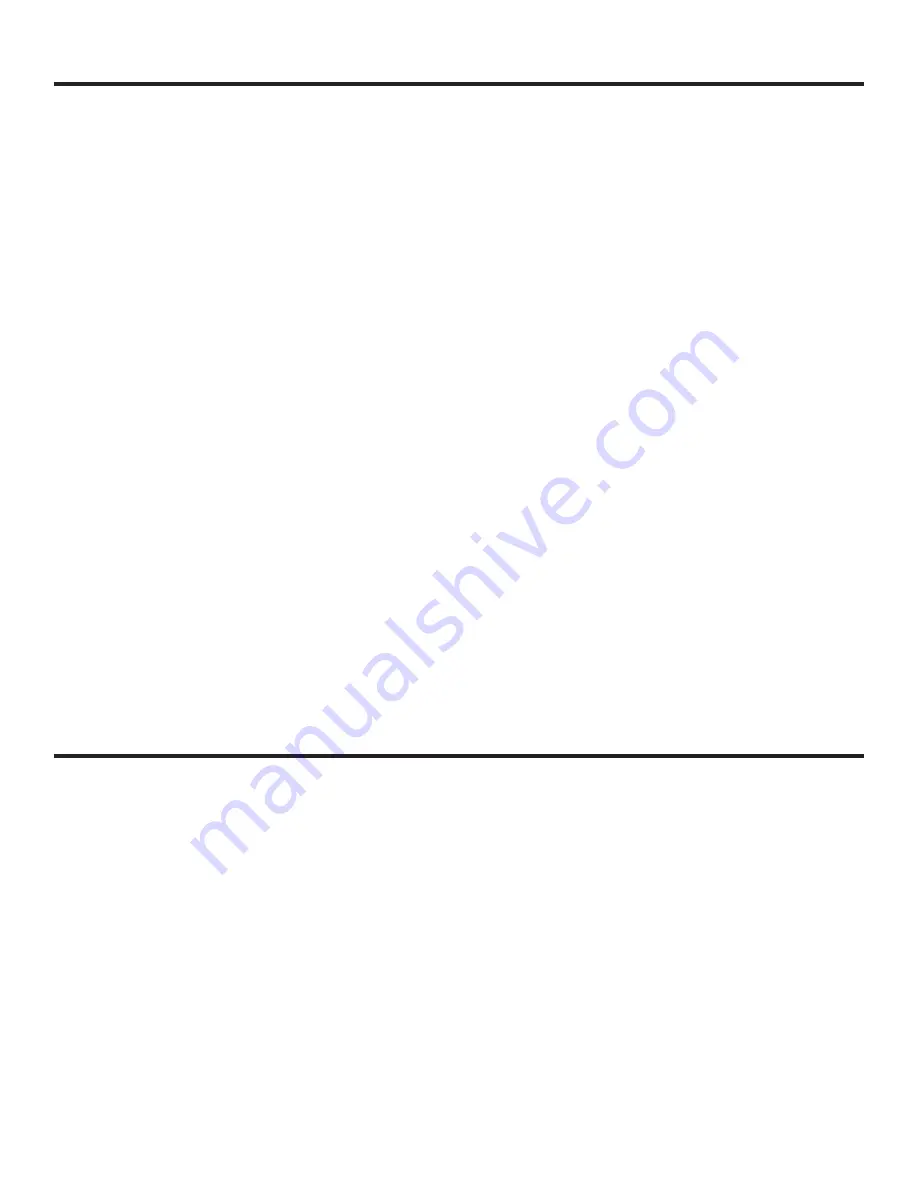
4
GENERAL SAFETY RULES
SPECIFIC SAFETY RULES
BLADE COASTS AFTER BEING TURNED OFF.
�
NEVER USE IN AN EXPLOSIVE ATMOSPHERE.
Normal sparking of the motor could ignite fumes.
�
INSPECT TOOL CORDS PERIODICALLY.
If dam-
aged, have repaired by a qualified service technician at
an authorized service facility. The conductor with insulation
having an outer surface that is green with or without yellow
stripes is the equipment-grounding conductor. If repair
or replacement of the electric cord or plug is necessary,
do not connect the equipment-grounding conductor to a
live terminal. Repair or replace a damaged or worn cord
immediately. Stay constantly aware of cord location and
keep it well away from the rotating blade.
�
INSPECT EXTENSION CORDS PERIODICALLY
and
replace if damaged.
�
GROUND ALL TOOLS.
If tool is equipped with three-prong
plug, it should be plugged into a three-hole electrical
receptacle.
�
CHECK WITH A QUALIFIED ELECTRICIAN
or service
personnel if the grounding instructions are not completely
understood or if in doubt as to whether the tool is properly
grounded.
�
USE ONLY CORRECT ELECTRICAL DEVICES:
3-wire
extension cords that have 3-prong grounding plugs and
3-pole receptacles that accept the tool’s plug.
�
DO NOT MODIFY
the plug provided. If it will not fit the
outlet, have the proper outlet installed by a qualified
electrician.
�
KEEP TOOL DRY, CLEAN, AND FREE FROM OIL AND
GREASE.
Always use a clean cloth when cleaning. Never
use brake fluids, gasoline, petroleum-based products, or
any solvents to clean tool.
�
STAY ALERT AND EXERCISE CONTROL.
Watch what
you are doing and use common sense. Do not operate
tool when you are tired. Do not rush.
�
DO NOT USE TOOL IF SWITCH DOES NOT TURN IT
ON AND OFF.
Have defective switches replaced by an
authorized service center.
�
USE ONLY CORRECT BLADES. Do not
use blades with
incorrect size holes. Never use blade washers or blade
bolts that are defective or incorrect. The maximum blade
capacity of your saw is 10 in. (254 mm).
�
BEFORE MAKING A CUT, BE SURE ALL ADJUST-
MENTS ARE SECURE.
�
BE SURE BLADE PATH IS FREE OF NAILS.
Inspect for
and remove all nails from lumber before cutting.
�
NEVER TOUCH BLADE
or other moving parts during
use.
�
NEVER START A TOOL WHEN ANY ROTATING COM-
PONENT IS IN CONTACT WITH THE WORKPIECE.
�
DO NOT OPERATE A TOOL WHILE UNDER THE
INFLUENCE OF DRUGS, ALCOHOL, OR ANY
MEDICATION.
�
WHEN SERVICING
use only identical replacement parts.
Use of any other parts may create a hazard or cause
product damage.
�
USE ONLY RECOMMENDED ACCESSORIES
listed
in this manual or addendums. Use of accessories that
are not listed may cause the risk of personal injury.
Instructions for safe use of accessories are included
with the accessory.
�
DOUBLE CHECK ALL SETUPS.
Make sure blade is
tight and not making contact with saw or workpiece
before connecting to power supply.
�
GUARD AGAINST KICKBACK.
Kickback occurs when
the blade stalls rapidly and workpiece is driven back to-
wards the operator. It can pull your hand into the blade
resulting in serious personal injury. Stay out of blade path
and turn switch off immediately if blade binds or stalls.
��
USE RIP FENCE.
Always use a fence or straight edge
guide when ripping.
�
SUPPORT LARGE PANELS.
To minimize risk of blade
pinching and kickback, always support large panels.
�
REMOVE ALL FENCES AND AUXILIARY TABLES
before
transporting saw. Failure to do so can result in an accident
causing possible serious personal injury.
�
ALWAYS USE BLADE GUARD, SPREADER, AND ANTI-
KICKBACK PAWLS
on all “through-sawing” operations.
Through-sawing operations are those in which the blade
cuts completely through the workpiece as in ripping or
cross cutting. Keep the blade guard down, the anti-kick-
back pawls down, and the riving knife/spreader/splitter
properly aligned to the saw blade.
�
ALWAYS SECURE WORK
firmly against rip fence, miter
fence, or miter gauge.
�
ALWAYS USE A PUSH STICK FOR RIPPING NAR-
ROW STOCK.
A push stick is a device used to push a
workpiece through the blade instead of using your hands.
Size and shape can vary but the push stick must always
be narrower than the workpiece to prevent the push stick
from contacting the saw blade. When ripping narrow
stock, always use a push stick, so your hand does not
come closer than three inches to the saw blade. Use a
featherboard and push blocks for all non-through cuts.
�
NEVER
perform any operation “freehand” which means
using only your hands to support or guide the workpiece.
Always use either the rip fence or miter fence to position
and guide the work.
�
NEVER
stand or have any part of your body in line with
the path of the saw blade.
�
NEVER
reach behind, over, or within three inches of the
blade or cutter with either hand for any reason.
Summary of Contents for TS2400LS
Page 44: ...44 NOTES ...