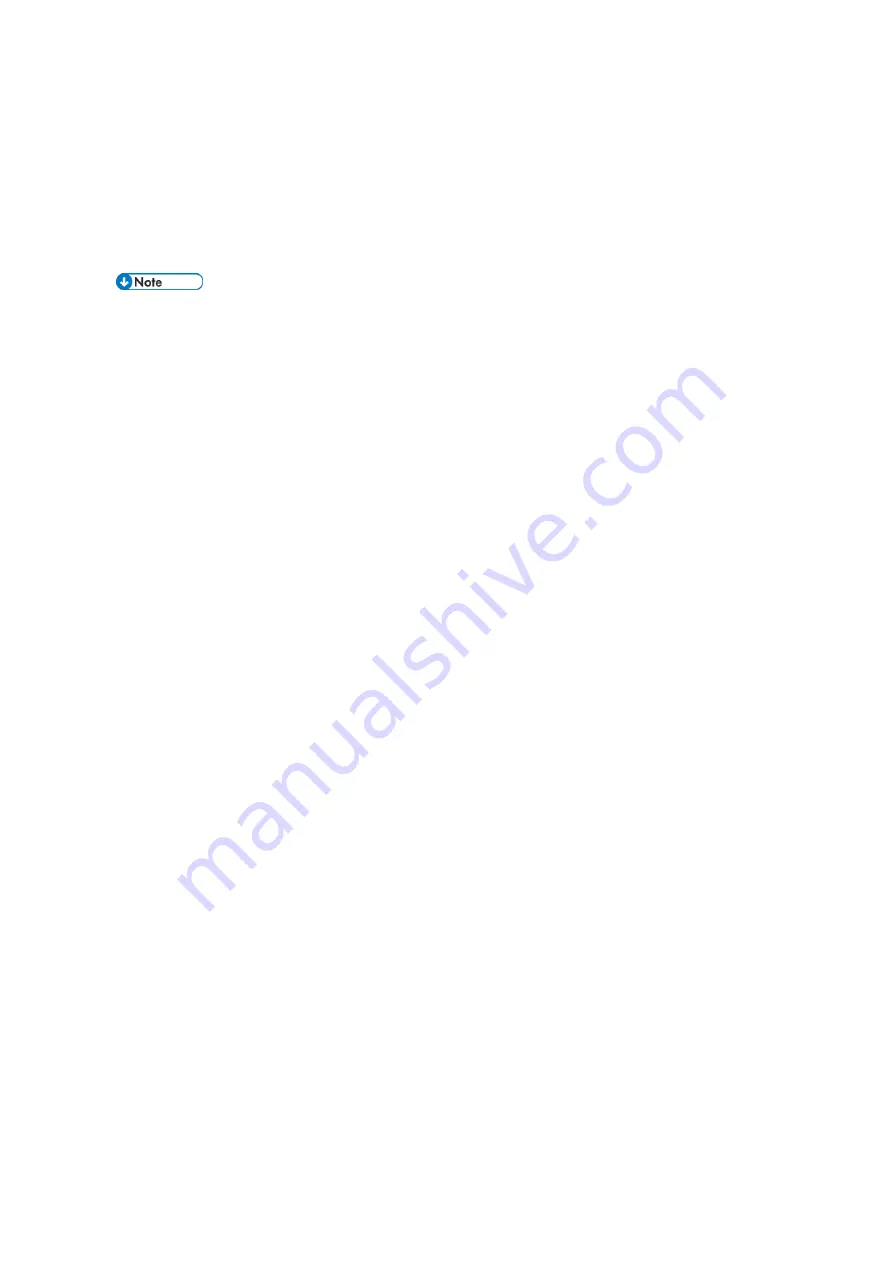
5.Other Information
853
these adjustment procedures.
1. Re-install the ITB. (Field Service Manual > ITB Unit > Belt Replacement > Belt Re-installation)
2. Open SP2-310-002 (Force Apply Lubricant Operation Time Setting), and then change the setting
from 300 to 100 sec.
3. Open SP2-920-013 (Steering Control Roller Timeout of Belt Ready), and then change the setting
from 400 to 105 sec.
The timing settings for these SP codes must be shortened from their normal operation
settings in order to allow diligent operation checks.
Reducing
SP2-310-002
to 100 sec. allows the machine to apply lubricant at 100 sec.
intervals, confirm that the position of the belt is stable, and then adjust the belt to the
positions of the left and right scale plates.
Depending on the conditions of the machine, after application of the lubricant ends the
belt may not be adjusted to its correct position within the target range within 100 sec. This
can occur if the belt has been re-installed out of position. In this case after the SP
executes lubricant application for 10 sec. and stops, the machine is not able to do the
correction quickly enough, so beforehand the belt ready
SP2-920-013
timeout setting is
set to 105 sec. If the machine cannot correct the belt position within 105 sec. the machine
issues SC471-01 (Belt Position Ready Timeout), and SP2-310-002 (applying the
lubricant) stops, and then starts the process again after the belt has been steered to the
correct position.
4. Set the following steering control SP codes to “0”.
SP 2-920-002 (Steering Control Roller Stable Position of Steering Roller)
SP 2-920-004 (Steering Control Roller Last Time Ai Value)
5. SP 2-310-001 (Force Apply Lubricant Belt Cleaning) – 1st Execution
SP2-310-001 executes (100 sec.) After the SP executes, check the value of SP2-920-002
(Steering Control Roller Stable Position of Steering Roller).
If the value is -20 ≤ SP Value ≤ +20, do the next 2nd SP execution. At this time the SP value in
Step 4 is not set to “0”.
If the SP value is <-20 or >+20, then the “Steering Plate Adjustment” described below is
required. After this adjustment, set the value for the Step 4 SP to “0”, and then do the 2nd SP
execution.
6. Do SP2-310-001 – 2nd Execution
Do SP2-310-001 (100 sec.). After this SP executes, check the value of SP2-920-002 (Steering
Control Roller Stable Position of Steering Roller)
If the value is -20 ≤ SP Value ≤ +20, do the next 3rd SP execution. At this time the SP value in
Step 4 is not set to “0”.
If the SP value is <-20 or >+20, then the “Steering Plate Adjustment” described below is
required. After this adjustment, set the value for the Step 4 SP to “0”, and then do the 3rd SP
Summary of Contents for Pro 8300S
Page 2: ......
Page 8: ......
Page 653: ...2 Image Quality Problems 645 of paper Solution ...
Page 654: ...2 Image Quality Problems 646 ...
Page 740: ...3 Paper Delivery Problems 732 Flowchart for a folded corner correction ...
Page 846: ...4 Troubleshooting for Peripheral Units 838 Solution ...
Page 849: ...4 Troubleshooting for Peripheral Units 841 ...
Page 885: ...5 Other Information 877 Registration Unit Rollers View B Top ...
Page 886: ...5 Other Information 878 Registration Unit Guide Plate View B Top ...
Page 888: ...5 Other Information 880 ITB Cleaning Unit Bottom ...
Page 889: ...5 Other Information 881 PTR Unit ...
Page 890: ...5 Other Information 882 PTB Unit ...
Page 892: ...5 Other Information 884 Fusing Exit Guide Plate Lower ...
Page 893: ...5 Other Information 885 Fusing Exit Guide Plate Upper ...
Page 895: ...5 Other Information 887 Straight Through Exit 1 View A Top ...
Page 896: ...5 Other Information 888 Straight Through Exit 2 View A Top ...
Page 897: ...5 Other Information 889 Rollers View A Top Invert Exit View B Left ...
Page 898: ...5 Other Information 890 Duplex 1 View A Top Duplex 2 View A Top ...
Page 901: ...5 Other Information 893 ...
Page 904: ...5 Other Information 896 Rib Position Vertical Transport Unit ...
Page 905: ...5 Other Information 897 ...
Page 908: ...5 Other Information 900 Paper Transport Movable Guide Ribs and Rollers Left View ...
Page 909: ...5 Other Information 901 Paper Transport Tray 5 Transport Fixed Guide Ribs Left View ...
Page 911: ...5 Other Information 903 ...
Page 912: ...5 Other Information 904 ...
Page 913: ...5 Other Information 905 Vacuum Feed LCIT Transport Path General Layout T1 T2 ...
Page 915: ...5 Other Information 907 Vertical Transport Right ...
Page 916: ...5 Other Information 908 Vacuum Feed LCIT Bridge Unit No Name A Upper Side B Bottom Upper Side ...
Page 925: ...5 Other Information 917 Driven Roller Drive Roller Rib Position ...
Page 927: ...5 Other Information 919 Driven Roller Drive Roller Rib Position Driven Rib Drive Rib ...
Page 931: ...5 Other Information 923 Driven Roller Drive Roller Rib Position Driven Rib Drive Rib ...
Page 934: ...5 Other Information 926 Driven Roller Drive Roller Rib Position Driven Rib Drive Rib ...
Page 937: ...5 Other Information 929 H Booklet Shift Roller I Fold Roller J Fold Exit Roller ...
Page 939: ...5 Other Information 931 Booklet Upper Guide Plate Booklet Lower Guide Plate ...
Page 940: ...5 Other Information 932 ...
Page 958: ...5 Other Information 950 Drive Roller ...
Page 960: ...5 Other Information 952 ...
Page 962: ...5 Other Information 954 Horizontal Transport Path Bead Position ...
Page 963: ...5 Other Information 955 ...