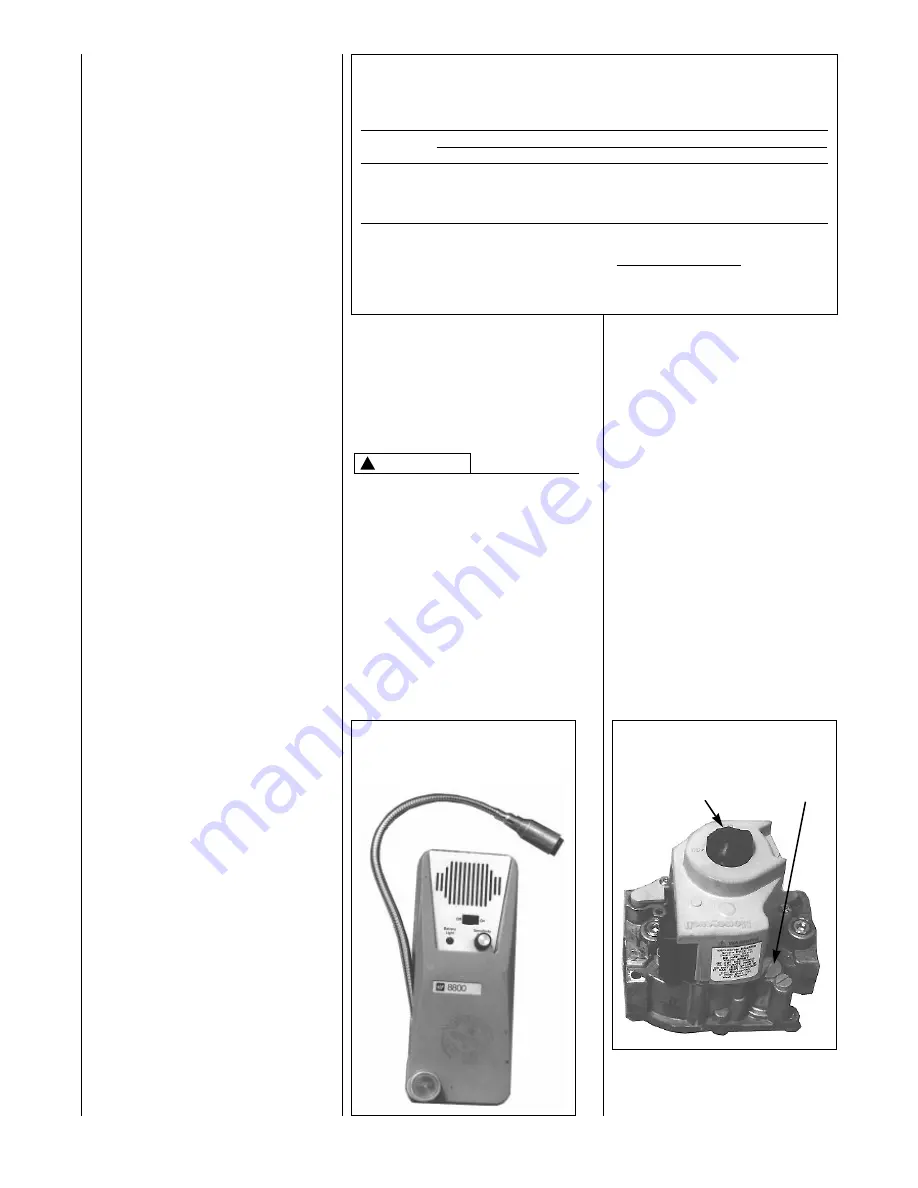
32
The minimum supply pressure to the
gas valve for proper furnace input
adjustments is 5" w.c. for natural gas,
however 6" to 7" is recommended.
The minimum supply pressure is 11"
w.c. for LP gas.
NEVER PURGE A GAS LINE INTO
THE COMBUSTION CHAMBER.
NEVER USE MATCHES, FLAME OR
ANY IGNITION SOURCE FOR
CHECKING LEAKAGE. FAILURE
TO ADHERE TO THIS WARNING
CAN CAUSE A FIRE OR
EXPLOSION RESULTING IN
PROPERTY DAMAGE, PERSONAL
INJURY OR DEATH.
To check for gas leakage, use an
approved chloride-free soap and
Install a ground joint union inside
the cabinet to easily remove the
control valve assembly. Install a
manual shut-off valve in the gas
line outside the furnace casing.
The valve should be readily
accessible to turn the gas supply on
or off. Install a drip leg in the gas
supply line as close to the furnace as
possible. Always use a pipe
compound resistant to the action of
liquefied petroleum gases on all
threaded connections.
IMPORTANT: When making gas pipe
connections, use a back-up wrench to
prevent any twisting of the control
assembly and gas valve.
Any strains on the gas valve can
change the position of the gas orifices
in the burners. This can cause erratic
furnace operation.
IMPORTANT: DO NOT RUN A
FLEXIBLE GAS CONNECTOR
INSIDE THE UNIT. Extend the 1/2"
black pipe from the gas valve to
the outside of the cabinet. Connect
any flexible gas connector from
there to the gas piping.
The gas pipe gasket in the cabinet
does not seal around a flexi-ble gas
connector. It is important to have all
openings in the cabinet burner
compartment sealed for proper
furnace operation.
IMPORTANT: ENSURE that the
furnace gas control valve not be
subjected to high gas line supply
pressures.
DISCONNECT the furnace and its
individual shut-off valve from the gas
supply piping during any pressure
testing that exceeds 1/2 p.s.i.g.
(3.48 kPa).
GAS PRESSURE
Natural gas supply pressure
should be 5" to 7" w.c. LP gas
supply pressure should be 11" to
13" w.c. This pressure must be
maintained with all other gas-fired
appliances in operation. Do not
exceed a maximum gas supply
pressure of 13" w.c. with any fuel.
!
WARNING
FIGURE 36
ELECTRONIC COMBUSTIBLE
GAS DETECTOR
FIGURE 37
GAS VALVE
PRESSURE
CONTROL
REGULATOR
KNOB
ADJUSTMENT
TABLE 3
NATURAL GAS PIPE CAPACITY TABLE (CU. FT./HR.)
Capacity of gas pipe of different diameters and lengths in cu. ft. per hr. with pressure drop of 0.3 in. and specific
gravity of 0.60 (natural gas).
Nominal
Length of Pipe, Feet
Iron Pipe
Size, Inches
10
20
30
40
50
60
70
80
1/2
132
92
73
63
56
50
46
43
3/4
278
190
152
130
115
105
96
90
1
520
350
285
245
215
195
180
170
1-1/4
1,050
730
590
500
440
400
370
350
1-1/2
1,600
1,100
890
760
670
610
560
530
After the length of pipe has been determined, select the pipe size which will provide the minimum cubic feet per hour
required for the gas input rating of the furnace. By formula:
Gas Input of Furnace (BTU/HR)
Cu. Ft. Per Hr. Required
=
Heating Value of Gas (BTU/FT
3
)
The gas input of the furnace is marked on the furnace rating plate. The heating value of the gas (BTU/FT3) may be
determined by consulting the local natural gas utility or the LP gas supplier.
water solution, an electronic com-
bustible gas detector (see Figure 36),
or other approved method.
GAS VALVE
This furnace has a 24-volt operated
valve. It has ports for measuring
supply pressure and manifold
pressure. The valve body contains a
pressure regulator to maintain proper
manifold pressure.
A manual control is on the valve
body. It can be set to only the “ON”
or “OFF” positions. The gas valve is
a slow-opening valve. See Figure 37.
When energized, it takes 6 to 8
seconds to fully open.
Summary of Contents for RGRA SERIES
Page 62: ...62...
Page 63: ...63...
Page 64: ...64 Rheem Manufacturing Company Air Conditioning Division Fort Smith Arkansas CM 1197...