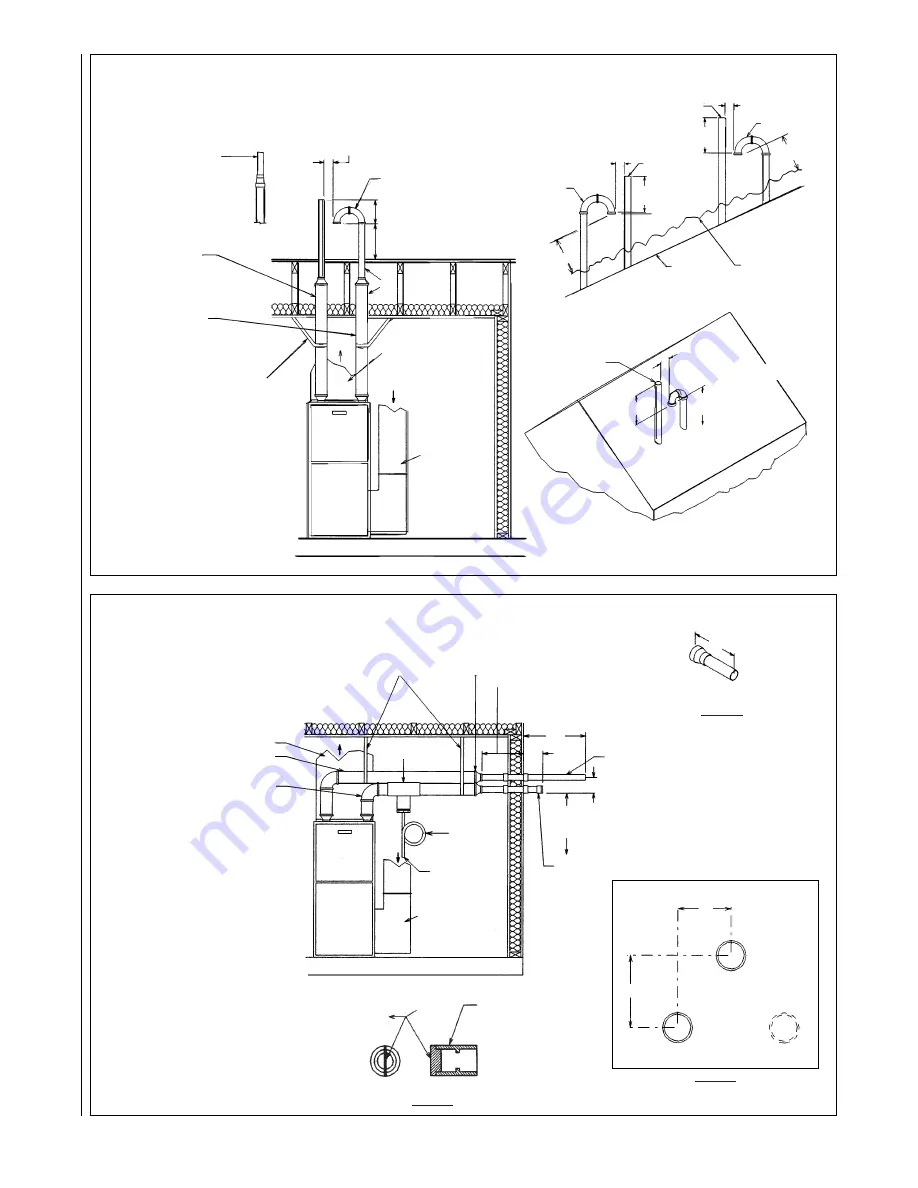
23
FIGURE 20
STANDARD VERTICAL DIRECT VENTING
UPFLOW MODEL SHOWN (TYPICAL FOR DOWNFLOW MODELS)
FIGURE 21
STANDARD HORIZONTAL DIRECT VENTING
UPFLOW MODEL SHOWN (TYPICAL FOR DOWNFLOW MODELS)
I407
EXHAUST
TERMINATION
➀
➁
3" MAX.
SEPARATION
COMBUSTION AIR
PIPE
12" MIN.
SEPARATION
12" MIN. ABOVE
ROOF LEVEL
ROOF LINE
EXHAUST PIPE
COMBUSTION
AIR PIPE
SUPPLY AIR
RETURN AIR
EXHAUST VENT
➂
➃
3"
MAX.
EXHAUST
VENT
ROOF LINE
COMBUSTION
AIR PIPE
12"
MIN.
12" MIN.
ANTICIPATED
SNOW LEVEL
COMBUSTION
AIR PIPE
3"
MAX.
EXHAUST
VENT
12"
MIN.
12" MIN.
3"
MAX.
12" MIN.
12" MIN. ABOVE
ANTICIPATED SNOW LEVEL
➄
NOTES:
➀
THE COMBUSTION AIR PIPE
MUST TERMINATE IN THE
SAME PRESSURE ZONE AS
THE EXHAUST PIPE.
➁
INCREASE THE 12-IN. MINIMUM
TO KEEP TERMINAL OPENING ABOVE
ANTICIPATED LEVEL OF SNOW
ACCUMULATION WHERE
APPLICABLE.
➂
WHEN 3-IN. DIAM. PIPE IS USED,
REDUCE TO 2-IN. DIAMETER BEFORE
PENETRATING ROOF. A MAXIMUM OF
18 IN. OF 2-IN. PIPE MAY BE USED
BEFORE PASSING THROUGH ROOF.
➃
SUPPORT VERTICAL PIPE EVERY 6
FEET.
➄
EXHAUST TERMINATION - TERMINATE
THE LAST 12 INCHES WITH 2
(
PVC
PIPE ON 90,000 THROUGH 120,000
BTUH MODELS. REDUCE AND
TERMINATE THE LAST 12 INCHES
WITH 1
1
⁄
2
(
PVC PIPE ON 45,000
THROUGH 75,000 BTUH MODELS.
PITCHED ROOF INSTALLATIONS
NOTES:
➀
SUPPORT HORIZONTAL PIPE
EVERY FOUR FEET.
➁
WHEN 3 IN. PIPE IS USED REDUCE TO 2 IN.
BEFORE PENETRATING OUTSIDE WALL.
➂
18 IN. MAXIMUM. 2 IN. DIAMETER PIPE MAY
BE USED INSIDE THE WALL.
➃
DETAIL “A” - EXHAUST TERMINATION
TERMINATE THE LAST 12 INCHES WITH 2
(
PVC PIPE ON 90,000 THROUGH 120,000
BTUH MODELS. REDUCE AND TERMINATE
THE LAST 12 INCHES WITH 1
1
⁄
2
(
PVC PIPE
ON 45,000 THROUGH 75,000 BTUH MODELS.
➄
INCREASE THE 12 IN. MINIMUM ABOVE
GRADE TO KEEP TERMINAL OPENINGS
ABOVE ANTICIPATED LEVEL OF SNOW
ACCUMULATION WHERE APPLICABLE.
➅
DETAIL “B”, INSTALL WIND DEFLECTOR
VANE IN 2 IN. PVC COUPLING IN VERTICLE
POSITION USING PVC SOLVENT.
THE COMBUSTION AIR TERMINATION MUST
BE IN THE SAME PRESSURE ZONE AS THE
EXHAUST TERMINATION.
3
(
12
(
4
(
4
(
SEE DETAIL A
VANE
2
(
PVC
COUPLING
12
(
MIN. ABOVE
GRADE LEVEL
➄
SEE DETAIL B
2
(
OR 3
(
TEE
W/DRAIN TRAP
RETURN AIR
TRAP
SUPPLY AIR
EXHAUST PIPE
COMBUSTION AIR PIPE
CONNECT
TO DRAIN
12
(
4
(
EXHAUST
INTAKE
OPTIONAL
INTAKE
DETAIL C
EXHAUST / INTAKE RELATIONSHIP
EXHAUST TERMINATION
➃
DETAIL A
COMBUSTION AIR TERMINATION
➅
DETAIL B
➀
➁
➂
I407
Summary of Contents for RGRA SERIES
Page 62: ...62...
Page 63: ...63...
Page 64: ...64 Rheem Manufacturing Company Air Conditioning Division Fort Smith Arkansas CM 1197...