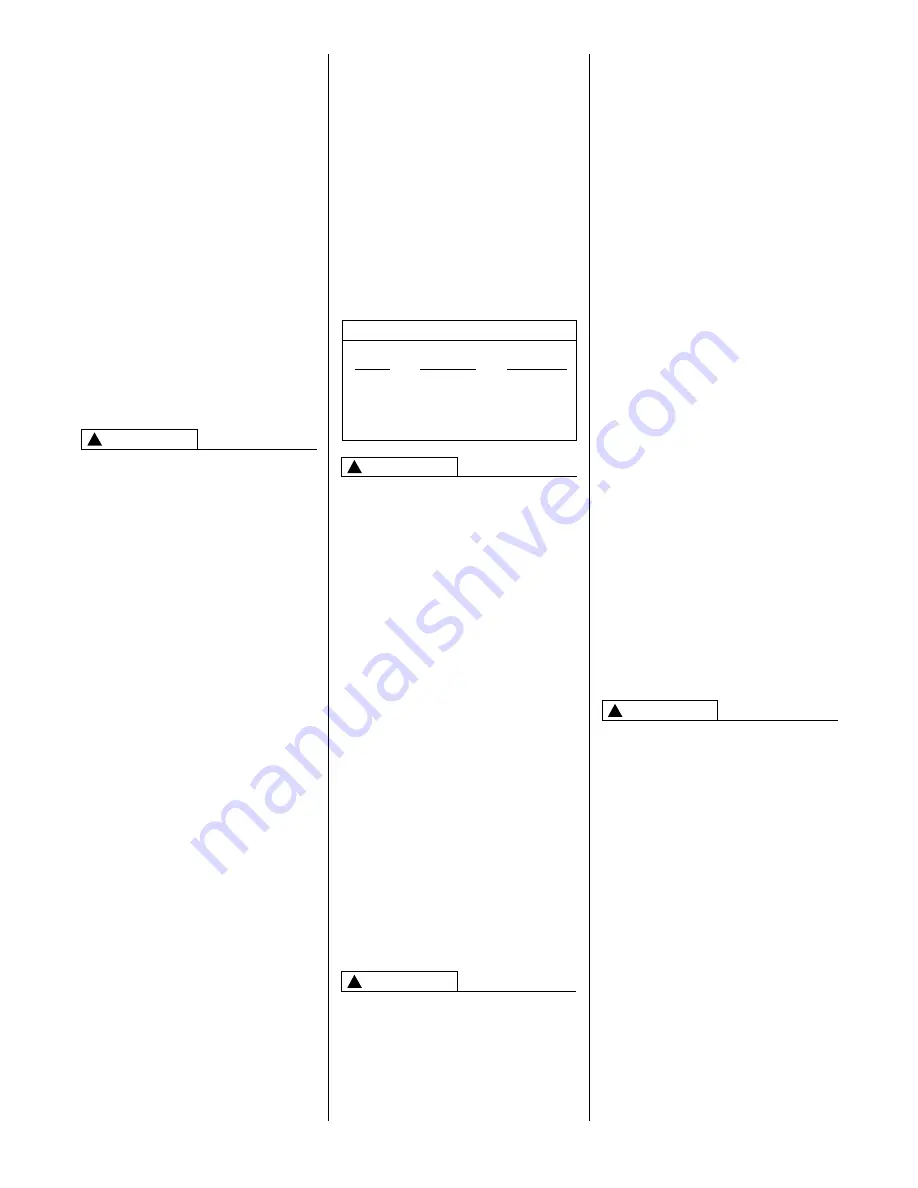
CLEARANCE –
ACCESSIBILITY
The design of forced air furnaces with
input ratings as listed in the tables on
the following pages are certified by
A.G.A. Laboratories and CGA for the
clearances to combustible materials
shown in inches.
See name/rating plate and clearance
label for specific model number and
clearance information.
Service clearance of at least 24 inches
is recommended in front of all furnaces.
ACCESSIBILITY CLEARANCES,
WHERE GREATER, MUST TAKE
PRECEDENCE OVER FIRE
PROTECTION CLEARANCES.
UPFLOW AND HORIZONTAL
INSTALLATION —
Certified for use on
combustible floor.
FURNACES MUST NOT BE
INSTALLED DIRECTLY ON
CARPETING, TILE OR OTHER
COMBUSTIBLE MATERIAL OTHER
THAN WOOD FLOORING.
INSTALLATION ON A
COMBUSTIBLE MATERIAL CAN
RESULT IN FIRE CAUSING
PROPERTY DAMAGE, SEVERE
PERSONAL INJURY OR DEATH.
UNIT DESIGN IS CERTIFIED FOR
INSTALLATION ON NON-
COMBUSTIBLE FLOOR. A SPECIAL
COMBUSTIBLE FLOOR SUB-BASE
IS REQUIRED WHEN INSTALLING
ON A COMBUSTIBLE FLOOR.
FAILURE TO INSTALL THE SUB-
BASE MAY RESULT IN FIRE,
PROPERTY DAMAGE, PERSONAL
INJURY OR DEATH. THIS SPECIAL
BASE IS OFFERED AS AN
ACCESSORY FROM THE FACTORY.
SEE THE CLEARANCE LABEL
LOCATED INSIDE THE FURNACE
FOR THE APPROPRIATE MODEL
NUMBER.
THE SPECIAL BASE IS NOT
REQUIRED WHEN THE FURNACE IS
INSTALLED ON TOP OF AN AIR
CONDITIONING PLENUM.
A gas-fired furnace for installation in a
residential garage must be installed so
that the burner(s) and the ignition
source are located not less than 18
(
above the floor and the furnace is
located or protected to avoid physical
damage by vehicles.
KEPT CLEAR AND FREE OF ALL
COMBUSTIBLE MATERIALS
INCLUDING GASOLINE AND OTHER
FLAMMABLE VAPORS AND
LIQUIDS. PLACEMENT OF
COMBUSTIBLE MATERIALS ON,
AGAINST OR AROUND THE
FURNACE JACKET CAN CAUSE AN
EXPLOSION OR FIRE RESULTING
IN PROPERTY DAMAGE,
PERSONAL INJURY OR DEATH.
THE HOMEOWNER SHOULD BE
CAUTIONED THAT THE FURNACE
AREA MUST NOT BE USED AS A
BROOM CLOSET OR FOR ANY
OTHER STORAGE PURPOSES.
DUCTING
Proper air flow is required for the
correct operation of this furnace. Too
little air flow can cause erratic
operation and can damage the heat
exchanger. The duct system must
carry the correct amount of air for
heating and cooling if summer air
conditioning is used.
Size the ducts according to acceptable
industry standards and methods. The
total static pressure drop of the entire
system should not exceed 0.5
(
w.c.
IMPORTANT:
Some high efficiency
filters have a greater than normal
resistance to air flow. This can
adversely affect furnace operation. BE
SURE TO CHECK AIR FLOW if using
any filter other than the factory-
provided filter.
NEVER ALLOW PRODUCTS OF
COMBUSTION OR THE FLUE
PRODUCTS TO ENTER THE
RETURN AIR DUCTWORK, OR THE
CIRCULATING AIR SUPPLY. ALL
RETURN DUCTWORK MUST BE
ADEQUATELY SEALED AND
SECURED TO THE FURNACE WITH
SHEET METAL SCREWS, AND
JOINTS TAPED. WHEN A FURNACE
IS MOUNTED ON A PLATFORM,
WITH RETURN THROUGH THE
BOTTOM, IT MUST BE SEALED
AIRTIGHT BETWEEN THE FURNACE
AND THE RETURN AIR PLENUM.
THE RETURN AIR PLENUM MUST
BE PERMANENTLY ENCLOSED.
NEVER USE A DOOR AS A PART OF
THE RETURN AIR PLENUM. THE
FLOOR OR PLATFORM MUST
PROVIDE SOUND PHYSICAL
SUPPORT OF THE FURNACE,
WITHOUT SAGGING, CRACKS,
UPFLOW UNIT DESIGN REQUIRES
A SOLID METAL BASE PLATE (SEE
TABLE ON PAGE 8 OR FURNACE
CLEARANCE LABEL FOR PART
NUMBER) MUST BE IN PLACE
WHEN THE FURNACE IS
INSTALLED WITH SIDE OR REAR
AIR RETURN DUCTS. FAILURE TO
INSTALL A BASE PLATE COULD
CAUSE PRODUCTS OF
COMBUSTION TO BE CIRCULATED
INTO THE LIVING SPACE AND
CREATE POTENTIALLY
HAZARDOUS CONDITIONS,
INCLUDING CARBON MONOXIDE
POISONING.
When coils are used with air handlers
or furnaces and installed above a
finished ceiling or living area, it is
recommended that an auxiliary sheet
metal condensate drain pan be
fabricated and installed under entire
unit. Failure to do so can result in
property damage.
SITE SELECTION
1. Select a site in the building near the
center of the proposed, or existing,
duct system.
2. Give consideration to the vent
system piping when selecting the
furnace location. Be sure the venting
system can get from the furnace to
the termination with minimal length
and elbows.
3. Locate the furnace near the existing
gas piping. Or, if running a new gas
line, locate the furnace to minimize
the length and elbows in the gas
piping.
4. Locate the furnace to maintain
proper clearance to combustibles as
shown in the preceding tables.
COMBUSTIBLE MATERIAL MUST
NOT BE PLACED ON OR AGAINST
THE FURNACE JACKET OR WITHIN
THE SPECIFIED CLEARANCES OF
THE VENT PIPE. THE AREA
AROUND THE FURNACE MUST BE
8
CAUTION
!
WARNING
!
WARNING
!
WARNING
!
TABLE 1
FURNACE
BASE
BASE
WIDTH
PLATE NO.
PLATE SIZE
14
(
RXGB-D14
11
5
⁄
8
(
x 23
9
⁄
16
(
17
1
⁄
2
(
RXGB-D17
15
1
⁄
8
(
x 23
9
⁄
16
(
21
(
RXGB-D21
18
5
⁄
8
(
x 23
9
⁄
16
(
24
1
⁄
2
(
RXGB-D24
25
5
⁄
8
(
x 23
9
⁄
16
(
Summary of Contents for RGDG
Page 35: ...35 FIGURE 31 FILTER RETAINING RODS SIDE RETURN FIGURE 32 DOWNFLOW FILTER INSTALLATION...
Page 43: ...FIGURE 36 FOR MODELS WITH UTEC 1012 920 OR HONEYWELL S9201E2001 INTEGRATED FURNACE CONTROL 43...
Page 44: ...44 FIGURE 37 FOR MODELS WITH WHITE RODGERS 50A62 101 INTEGRATED FURNACE CONTROL...
Page 45: ...45 FIGURE 38 FOR MODELS WITH UTEC 1012 925 INTEGRATED FURNACE CONTROL...
Page 46: ...46...
Page 47: ...47...
Page 48: ...48 CM 398 Rheem Manufacturing Company Air Conditioning Division Fort Smith Arkansas...