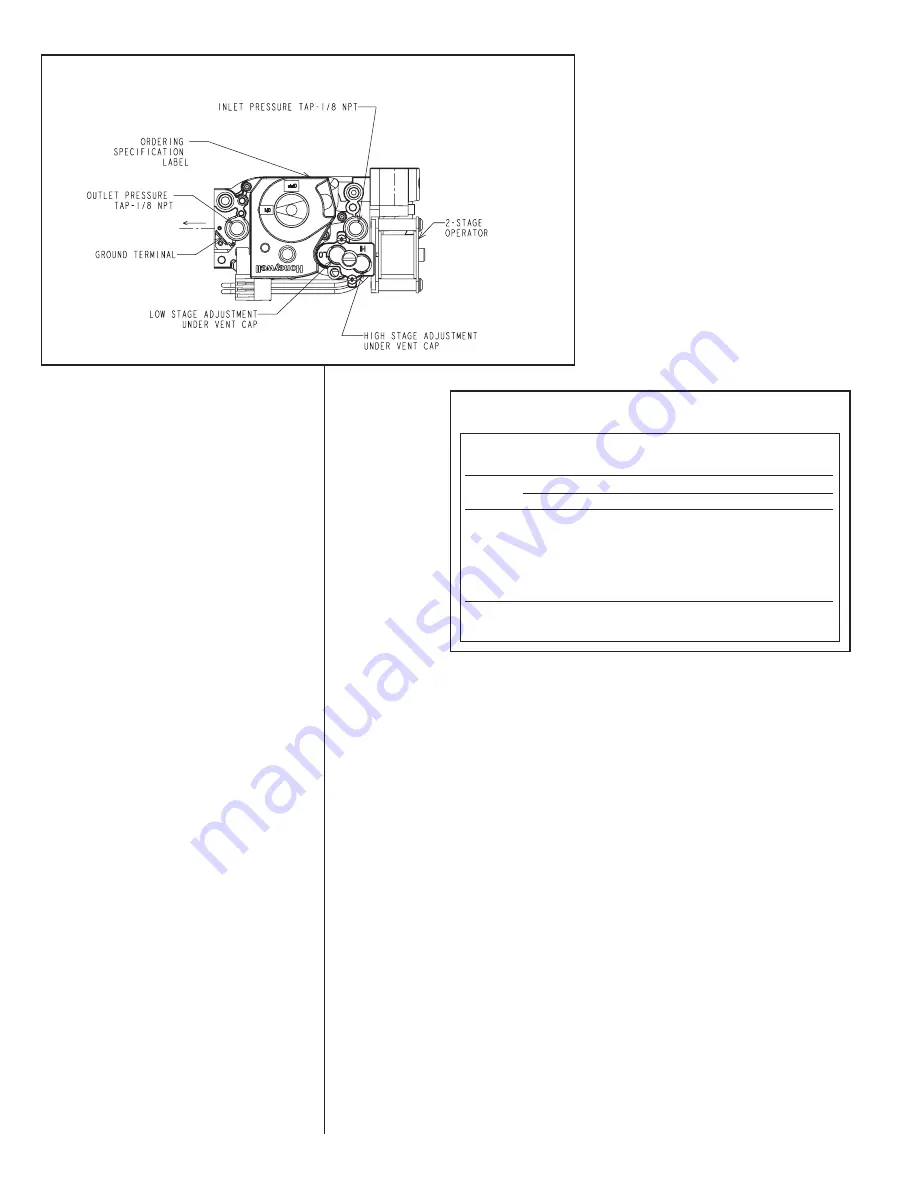
18
Maximum capacity of pipe in thousands of BTU per hour of undiluted liquefied petroleum
gases (at 11 inches water column inlet pressure).
(Based on a Pressure Drop of 0.5 Inch Water Column)
TABLE 2
LP GAS PIPE CAPACITY TABLE (CU. FT./HR.)
Nominal
Iron Pipe
Size, Inches 10 20 30 40 50 60 70 80 90 100 125
150
275 189 152 129 114 103 96 89 83 78 69 63
567 393 315 267 237 217 196 182 173 162 146 132
1,071 732 590 504 448 409 378 346 322 307 275 252
2,205 1,496 1,212 1,039 913 834 771 724 677 630 567 511
3,307 2,299 1,858 1,559 1,417 1,275 1,181 1,086 1,023 976 866 787
6,221 4,331 3,465 2,992 2,646 2,394 2,205 2,047 1,921 1,811 1,606 1,496
1/2
3/4
1
1-1/4
1-1/2
2
Length of Pipe, Feet
Example (LP): Input BTU requirement of unit, 150,000
Equivalent length of pipe, 60 ft. = 3/4
”
IPS required.
FIGURE 18B
HONEYWELL VR8305Q4120 TWO STAGE GAS VALVE
C. ADJUSTING OR CHECKING FURNACE INPUT
– Natural Gas Line Pressure 5
”
- 10.5
”
W.C.
– LP Gas Line Pressure 11
”
- 13
”
W.C.
– Natural Gas Manifold Pressure 3.5
”
W.C.
– LP Gas Manifold Pressure 10
”
W.C.
Supply and manifold pressure taps are located on the gas valve body 1/8” N.P.T.
and on the manifold. See Figure 18B.
Use a properly calibrated manometer gauge for accurate gas pressure readings.
Only small variations in the gas flow should be made by means of the pressure
regulator adjustment. Furnaces functioning on LP gas must be set by means of the
tank or branch supply regulators. The furnace manifold pressure should be set at 10”
W.C. at the gas control valve.
To adjust the pressure regulator, remove the regulator vent cover and turn the
adjustment screw clockwise to increase pressure or counterclockwise to decrease
pressure. See Figure 18B.
Then replace the regulator vent cover securely.
Any necessary major changes in the gas flow rate should be made by changing the
size of the burner orifices. To change orifice spuds, shut off the manual main gas
valve and remove the gas manifold.
For elevations up to 2,000 feet, rating plate input ratings apply. For high altitudes
(elevations over 2,000 ft.), see conversion kit index 92-21519-XX for derating and
orifice spud sizes.
Check of input is important to prevent over-firing of the furnace beyond its
design-rated input. NEVER SET INPUT ABOVE THAT SHOWN ON THE RATING
PLATE. Use the following table or formula to determine input rate.