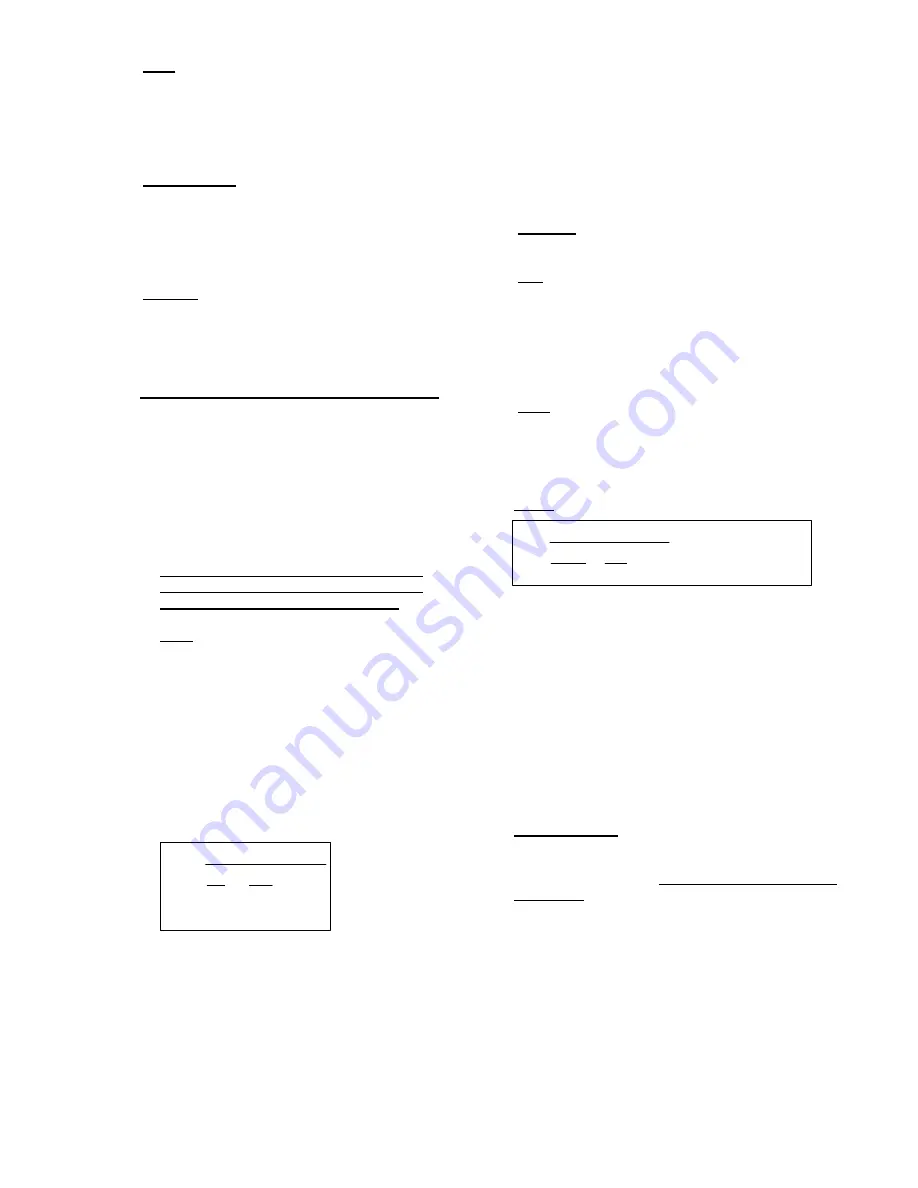
0710RHC8-JLNLEN
24
/
36
1
1
2
1
2
+
⎟
⎠
⎞
⎜
⎝
⎛
−
×
=
V
V
x
x
V
V
tot
tot
HS
)
/
³
13068
(
/
³
.
3
1
1
.
2
.
5
.
357
200
.
5
63
99
00
90
00
h
m
s
m
V
HS
=
+
⎟⎟
⎠
⎞
⎜⎜
⎝
⎛
−
×
=
Note
In this case 2.
99
m³/s
(= 10750m³/h)
flows through
the heat exchanger enclosure.
The remaining 2.
01
m³/s
(=7250m³/h)
flows through
the by-pass duct
(5.
00
m³/s – 2.
99
m³/s = 2.
01
m³/s)
C) Pressure loss :
In this case the total pressure loss over the RHC
module with by-pass can be extracted from figure
12. The airflow through the heat exchanger
enclosure must be applied to determine the total
pressure drop.
Example :
- Airflow through the heat exchanger
enclosure = 2.
99
m
³
/s (10750 m
³/
h
)
- Total pressure drop = 50 Pa (approx.).
11.3 Calculation of alternative by-pass dimension
Due to space restrictions it may not be possible
to use the above mentioned maximum
dimension by-pass.
In this case a smaller by-pass can be applied.
Obviously, this smaller by-pass will result in
higher portion of the total air flow through the
heat exchanger enclosure and consequently in a
higher total pressure drop
A) To calculate this air flow through the
heat exchanger enclosure, following
interpolation rule should be applied
:
With
:
V2
=
Recommended air flow
(Table 7) (m³/s)
V
tot
=
Total air flow (m³/s)
x
1
=
Recommended by-
pass (dim A or C) (as
calculated in section
11.1).
x
2
=
Applied by-pass dim.
(mm)
Then V
HS
(air flow through heat exchanger
enclosure can be calculated as :
As explained above, the air flow V
HS
through
the heat exchanger enclosure must be used in
figure 12
to extract the correct total pressure
drop over the RHC module with by-pass.
The air flow V
HS
may not exceed the
maximum airflow allowed according to section
4.1.2 to avoid super cooling of the flue gases.
B) Example
.
RHC 8075 09 RJL
with :
- Total air flow : 5m³/s (18000m³/h)
- Expected min. inlet temperature : -5°C
- Recommended max. dim C = 357.
90
mm
(see above 1B)
- Dimension X = 400mm
- Applied by-pass dim. C = 200mm
Then :
x1
= 357.
90
mm
x2 = 200mm
Vtot = 5m³/s
V2 = 2.
99
m³/s (10750m³/h)
(see table 7)
Result
:
Consequently, 3.
63
m³/s (13068 m³/h) flows through
the heat exchanger enclosure and the remaining
1.
37
m³/s
(=4932m³/h)
(= 5.
00
m³/s – 3.
63
m³/s) flows
through the by-pass channel.
From section 4.1.2 the maximum allowable airflow
through the heating module enclosure is 16850
m³/h (for this example).
We notice the 13068 m³/h is still below this
maximum allowable figure. Consequently there is
no probability of condensation forming within the
tubes.
C) Pressure drop :
The total pressure drop can be derived from figure
12. Use the air flow through the heat exhanger
enclosure to determine the total pressure drop.
(@13068 m³/h)
Result : 75Pa (approx)