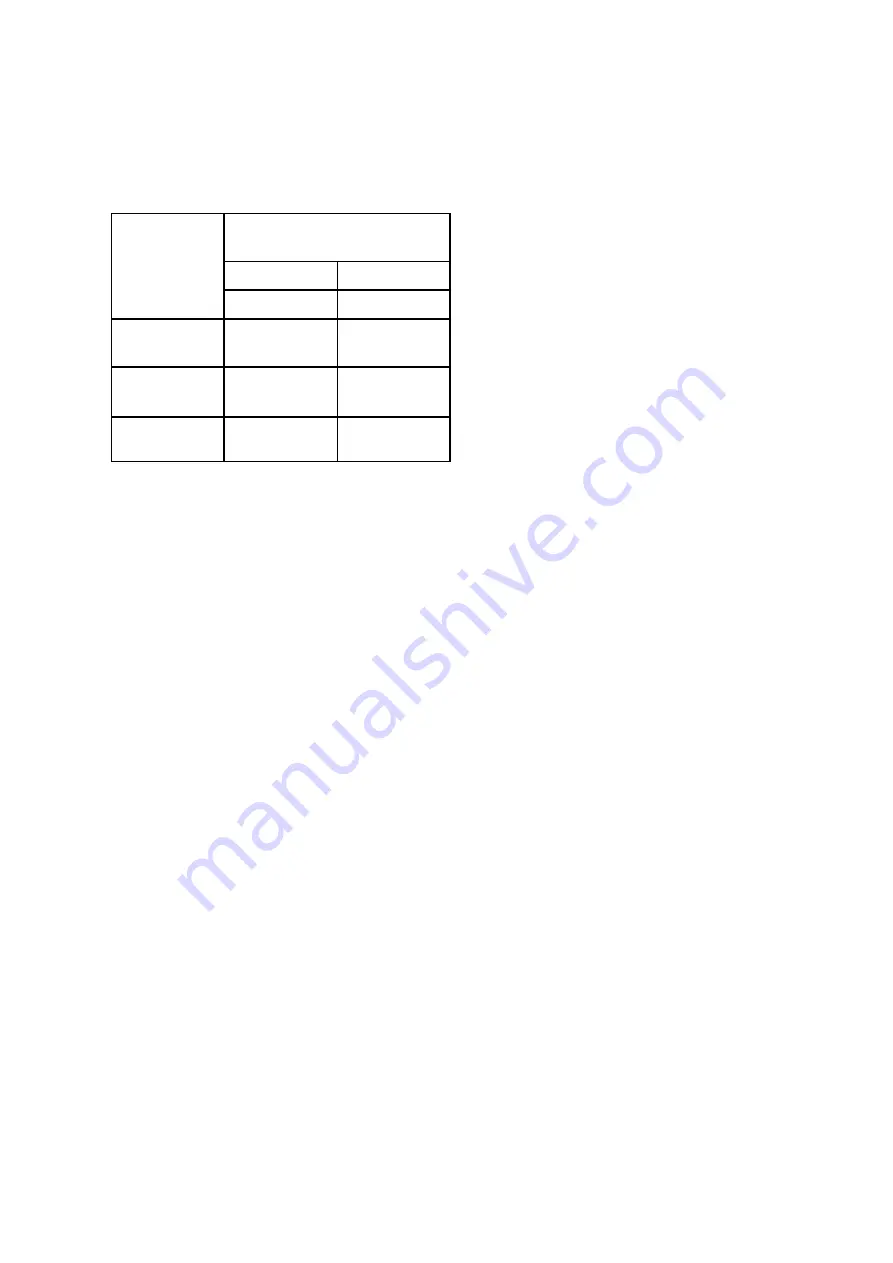
10
be within 1000 mm of floor level for natural
gas and ideally at floor level for lpg gas
installations but in any event no higher than
250 mm.
2.4.1.2 Mechanical Ventilation to the
Heated Space
The table below provides specific data for
each heater model as -
In the event that the heater(s) are to be
installed without the positive connection of
combustion ductwork within a heated space
and where that heated space has a design
air change of less than 0.5 air changes per
hour and that the installer prefers to
mechanically ventilate the heated space
rather than provide ventilation openings then
-
The heated space needs to be
mechanically ventilated so that the
design air change is 0.5 air changes
per hour or greater.
It is a requirement that the mechanical
ventilation shall be of the !input! Type
with either natural or mechanical
extraction
Systems of mechanical extraction with
a natural inlet shall not be used
It is necessary to provide an automatic
means to safely inhibit heater(s)
operation should mechanical air
supply fail for any reason
2.4.2 Heaters Installed within a Plant
Room or Enclosure
A plant room means a room housing the
heater plant and probably other items of
building service plant and would generally
have generous space for maintenance.
An enclosure is where the heater is installed
within a compartment or confined area
where space is limited.
Where heaters are installed within a plant
room or enclosure then provision for both
combustion air and / or air for general
ventilation will be required by means of high
and low level ventilation openings (sections
2.4.2.1 and 2.4.2.2 refer to plant room
applications and sections 2.4.2.3 and
2.4.2.4 refer to enclosure applications).
Alternatively the plant room or enclosure
may be mechanically ventilated (section
2.4.2.5 refers).
2.4.2.1 Natural Ventilation Openings
to Plant Rooms for Room Sealed
Heaters
For plant room applications the minimum
free area of ventilation opening will depend
upon whether the heater(s) is installed in
room sealed mode (ie with a positive
connection to atmosphere of both flue and
combustion air)
Or with flue only (ie without the positive
connection to atmosphere of a combustion
air duct).
Where the heater(s) is installed in a plant
room and in room sealed mode (ie with a
positive connection to atmosphere of both
flue and combustion air ) the minimum free
area of ventilation opening needs to be
At high level 5 cm
2
for each kW of
rated heat input.
At low level 5 cm
2
for each kW of rated
heat input.
The high level ventilation opening should be
sited on an external wall and positioned as
high as is practical and always within the top
MODEL
Minimum Free Area Of
Ventilation Opening
High Level
Low Level
cm
2
cm
2
95
None
211
120
None
263
145
None
315