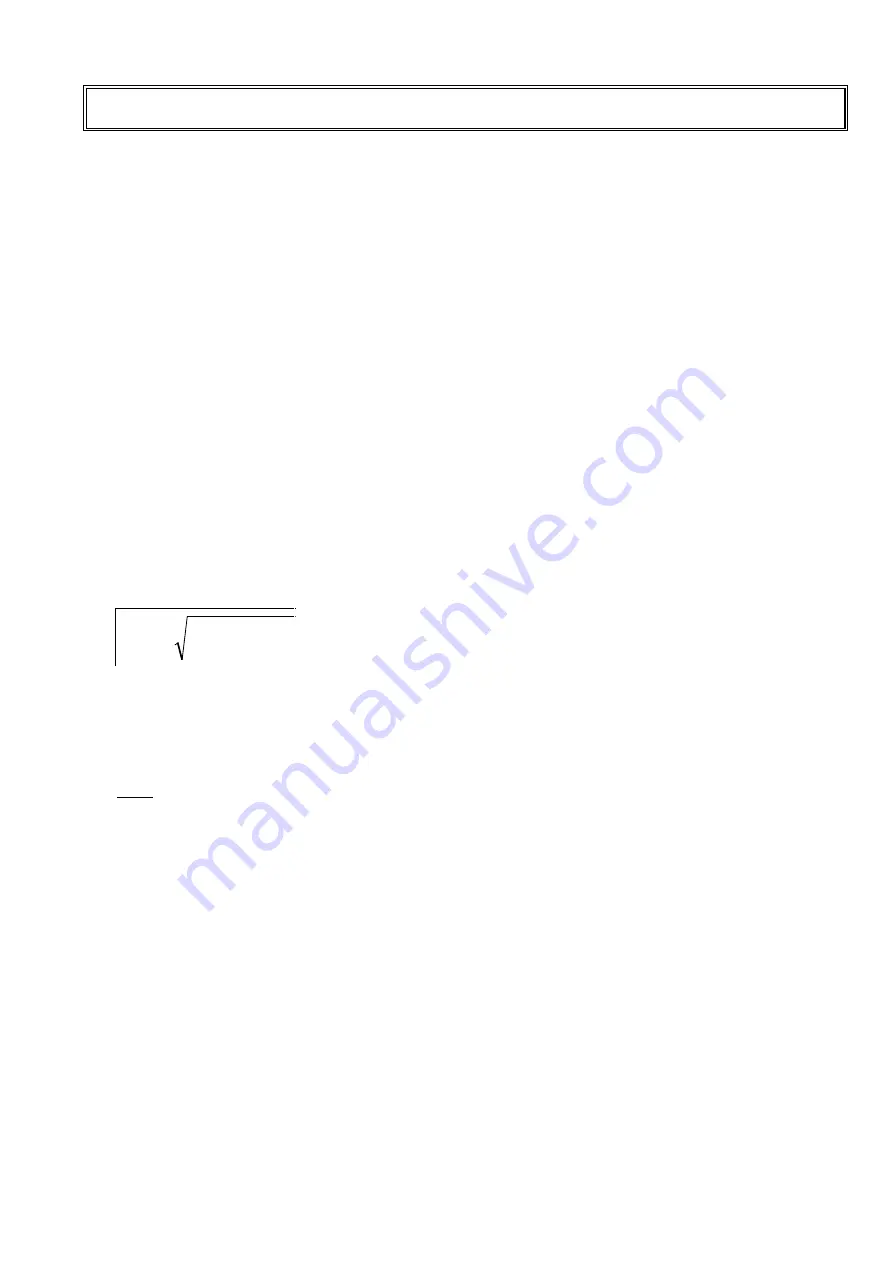
0108X1DHGBEN
11
D
0.5
+
D
2
2
=
D1
SECTION 5 FLUE SYSTEM
5.1 EURO-X air heaters must be connected to a flue
system venting the products of combustion directly
to outdoors.
Flue systems must be installed in accordance with
the rules in force taking into account the location of
flue termination relative to the construction
elements of the building, i.e. windows, roof levels,
etc., and in accordance with statutory
requirements.
5.2 The products of combustion may reach a
temperature of 230
°
C. Reznor recommend that
appliances are connected to individual flues sized in
accordance with the diameter appropriate to the
appliance flue connection socket.
Flues must be terminated with an approved
terminal fitting.
5.3 A minimum length of 2.0 m is required to
ensure a good flue draught condition.
5.4 Where it is necessary to flue more than one
appliance into a common flue as fig.9 then the flue
should be sized in accordance with the following
formula:
Where:
D
1
= new flue size required
D
2
= diameter of largest flue
D
3
= diameter of additional flue
Never
connect an additional flue to a main stack at a
90
°
angle an inverted
Y
piece must be used.
5.5 It is not recommended to install the flue directly into
the appliance flue socket but to use a stopped tee
piece following a bend off of the air heater. This
practice prevents ingress of water into the appliance
and affords the facility to connect to a drain to
evacuate water and condensation should this occur.
Figure 7 shows the method recommended.
5.6
If it is necessary to include horizontal runs of flue
within the system, then the horizontal section of flue
should be installed with a positive rise away from the
appliance of at least 1
°
or 17 mm per metre run until
the vertical section.
A vertical rise from the appliance to the terminal point
of 2.0 X the horizontal length must be maintained as
indicated in figure 6.
5.7 The use of twin wall flue should be considered if
condensation in the flue system is a possibility.
5.8 Difficult flue systems may incorporate a Reznor
"EUROVENTER".