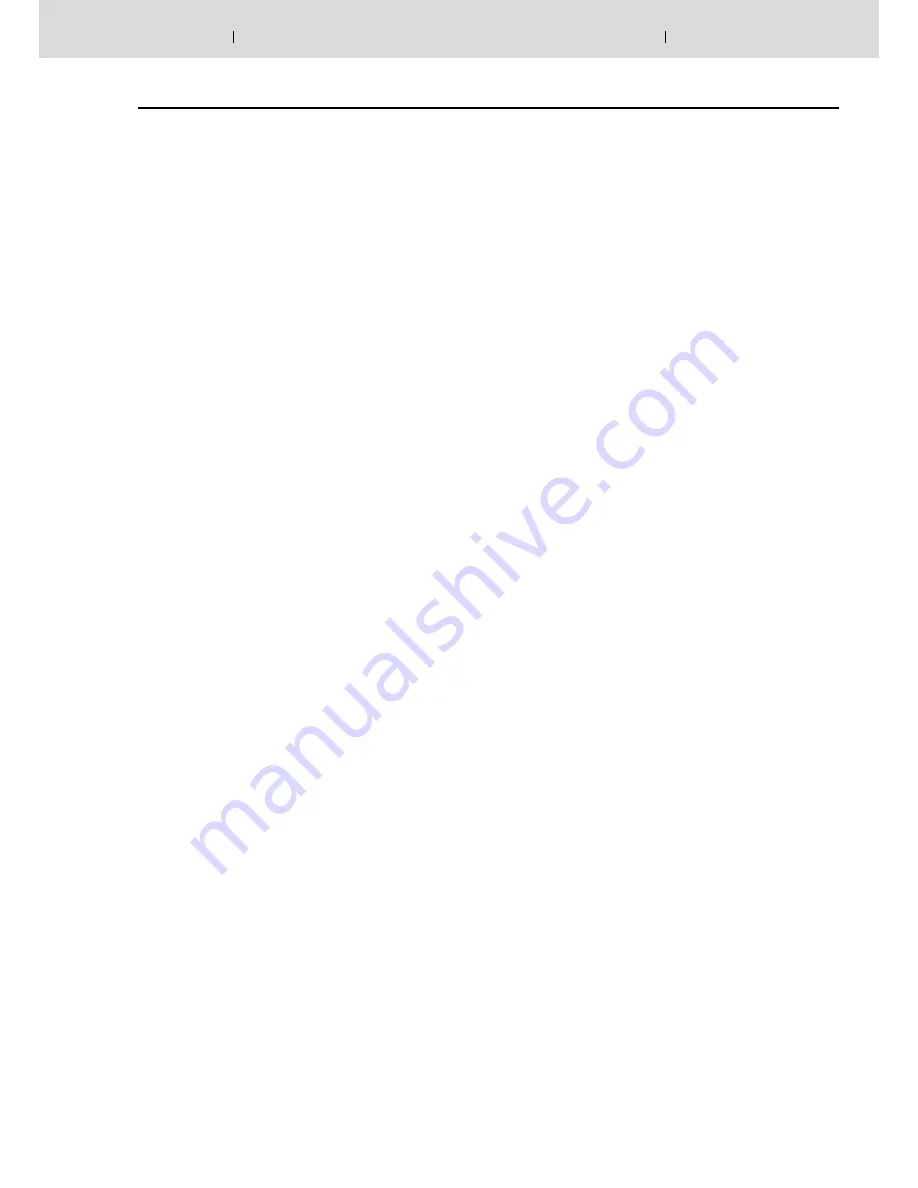
Hydraulics
Bosch Rexroth AG
RE 51421/07.11 245LEN0040 - 0400; 245LE0130, 0150
15
/16
Installation, commissioning and maintenance
Installation of the filter
Verify operating overpressure with name plate information.
Remove the blanking plugs in the filter inlet and outlet. Screw
the filter head (1) to the fastening device, considering flow di-
rection (direction arrows) and servicing height of the element.
Make sure that the components are assembled in a stress-
less form. The housing must be grounded.
The filter must preferably be installed with the filter bowl (2)
downward. The maintenance indicator must be arranged in a
well visible way.
Connection of the electronic maintenance indicator
Basically, the filter is equipped with mechanical optical main-
tenance indicator (4). The electronic maintenance indicator is
connected via the switching element (6) with 1 or 2 switching
points, which is attached to the mechanical optical mainte-
nance indicator and held by means of the locking ring.
When must the filter element be exchanged or
cleaned respectively?
– After initial start-up of the system, the filter element is to
be exchanged.
– Upon start-up in cold condition, the red pushbutton of the
optical maintenance indicator (4) may jump out and an
electrical signal is output via the switching element. Only
push the red pushbutton in again after the operating tem-
perature has been reached. If it jumps out again immedi-
ately or if the electrical signal has not gone out at operat-
ing temperature, the filter element must be exchanged or
cleaned respectively after the end of the shift.
– The filter element should be replaced or cleaned after max.
6 months at the latest.
Element exchange
– Switch off the system and discharge the filter on the pres-
sure side.
– Screw off the filter bowl (2) by anticlockwise rotation. Clean
the filter housing in a suitable medium.
– Remove the filter element (3) from the spigot in the filter
head by turning it slightly.
– Check the seal ring in the filter bowl for position and dam-
age. If necessary, these parts are to be renewed.
– Replace filter elements H...XL, clean filter elements G....
– The efficiency of the cleaning process depends on the type
of dirt and the amount of the pressure differential before
the filter element exchange. If the differential pressure after
the filter element exchange exceeds 150 % of the value of
a brand-new filter element, the G… element also needs to
be replaced.
– Check whether the type designation or material number on
the replacement element corresponds to the type designa-
tion/material number on the name plate of the filter.
– Install replaced or cleaned filter element on the spigot again
by slightly turning it.
– Now screw in the filter bowl to stop (torque 50 Nm
+10 Nm
).