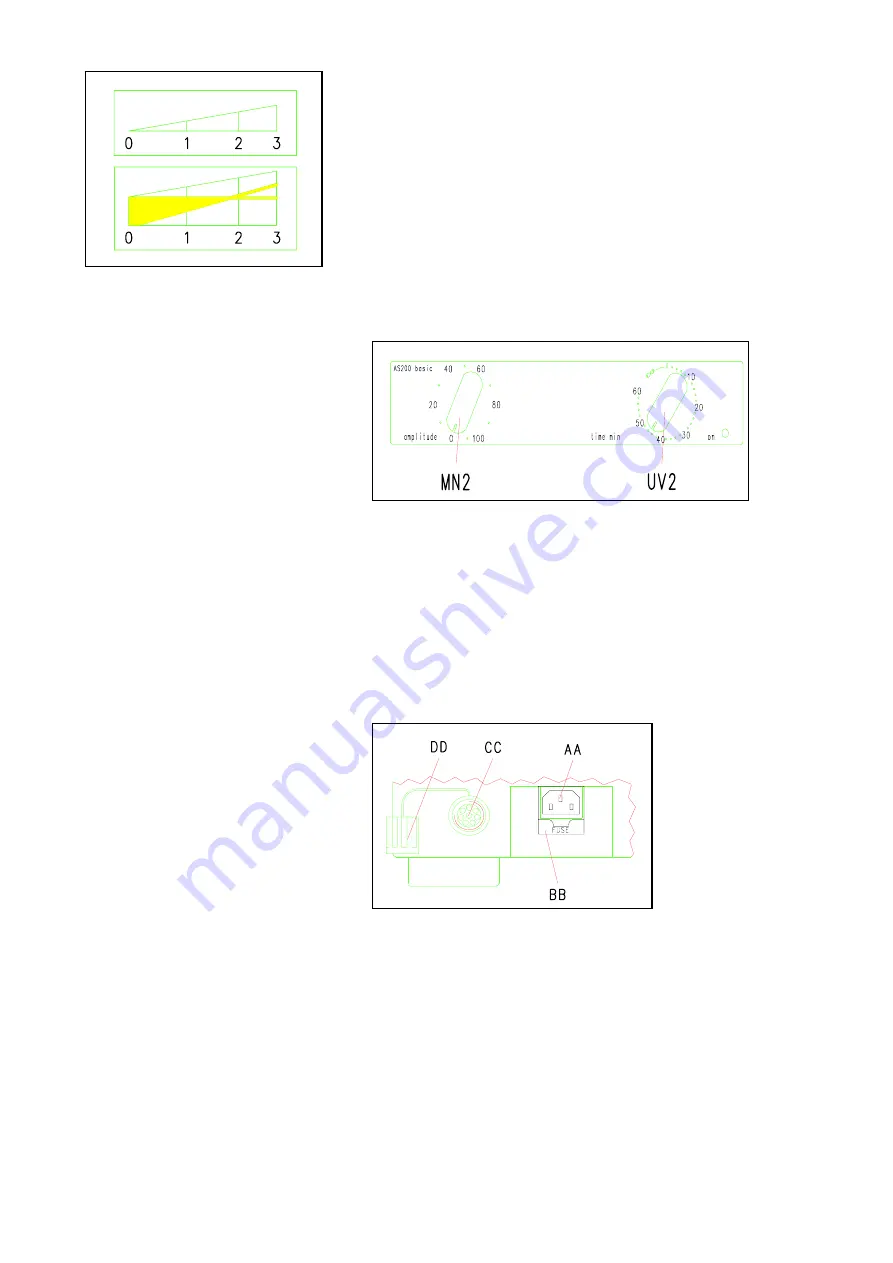
21.11.2001
Retsch GmbH
23
Doc. No E98.014-016.9999 A
Reading the vibration height: Fig. 16
The vibration height is shown optically, on the front of the sieve
plate.
The intersection of the two lines shows the vibration height when
the machine is running.
In the illustration at the left the value is 1.8 mm.
Naturally, your AS200 can only achieve the vibration heights
which are within the values shown in the loading diagram.
Fig. 16
Setting the time
Fig. 17
Setting the time for 1 to 60 min.: Fig. 17
* Turn the knob
UV2
to the right to set the desired running
period.
Switching on continuous operation: Fig. 17
* Turn the knob
UV2
to the left to the
∞
symbol
Replacing the fuses – All AS200 models
Fig. 18
Two glass tube micro-fuses, 4 A, slow-blow (5
×
20 mm),
will be required for all AS200 models.
Replacement: Fig. 18
* Disconnect the line power cord.
* Pull out the fuse holder
BB.
* Replace the fuses.
* Push the fuse holder
BB
back into normal position.