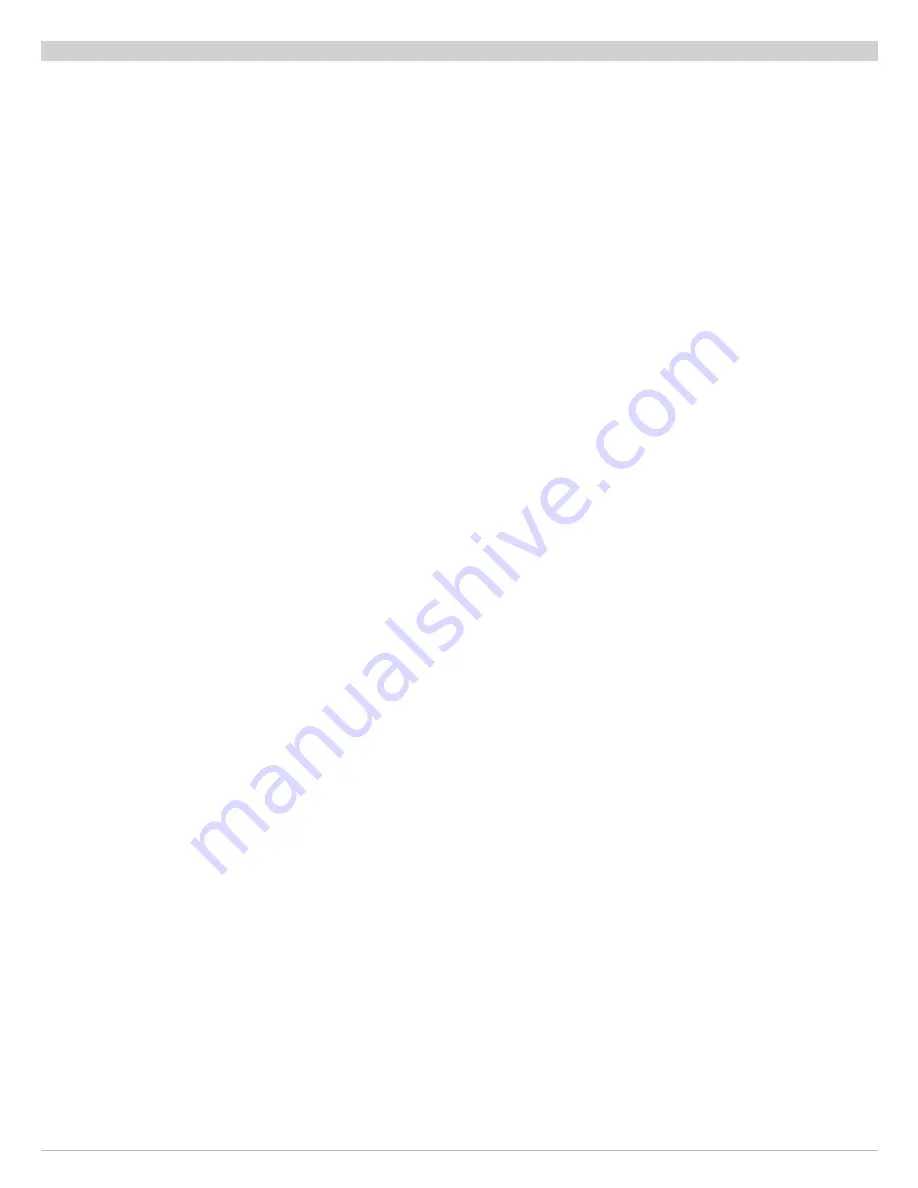
SEQUENCE OF OPERATION
5.
If cooler room temperature is desired, adjust
thermostat to cooler temperature setting until electric
heater turns off. Fan will stop.
6.
Place the thermostat or system switch to OFF position.
All operation should stop.
Heating Cycle — Hydronic Option
Verify the motorized valve is rated for correct voltage.
• Most RetroAire units with unit mount controls will power
hydronic valve that is same voltage as unit (ex: unit
rated 208/230V will power a 208/230V).
• Check the wiring diagram (located on the unit) and
voltage application for the speci
fi
c unit.
• Other valve con
fi
gurations and voltage options are
available. Consult Technical Service if unit voltage does
not match your valve application.
Room temperature must be below 85°F (29°C) for
hydronic heater to operate.
1.
Place thermostat or system switch in HEAT position.
2.
Adjust thermostat to warmer temperature. Following
occurs
–
Motorized valve should open and allow hot
water to run through coil.
–
Indoor fan will run, blowing air through hydronic
coil.
–
Signal to water valve continues until room
temperature rises above setpoint by 3°F (2°C).
3.
After unit starts running and area warms, adjust
thermostat to cooler temperature, hydronic valve closes
and indoor fan switches off.
4.
If warmer room temperature is desired, adjust
thermostat to warmer temperature setting, which
opens hydronic valve and turns on the indoor fan.
5.
If cooler room temperature is desired, adjust
thermostat to cooler temperature setting. Hydronic
valve will close and fan stops.
6.
Place thermostat or system switch to OFF
position.
All operation should stop.
Heat Pump Water Source Console Units
Unit is equipped with a reversing valve that is energized for
cooling and de-energized in heating mode.
Cooling Cycle — Heat Pump Units
Room temperature must be above 65°F (29°C) for
compressor to operate in cooling mode on Water
Source Console Units with unit-mounted controllers.
1.
Place thermostat or system switch to COOL.
2.
Adjust thermostat to cooler temperature until indoor
fan starts running. Compressor will turn on and cold
air begins to
fl
ow from the unit. Allow unit to continue
operating cooling the room and remove humidity.
3.
After unit starts running and space gets cooler, adjust
thermostat to warmer temperature until compressor
cycles off.
4.
If colder room temperature is desired, adjust
thermostat to cooler temperature setting, turning
compressor and fan back on.
5.
If warmer room temperature setting is desired, adjust
thermostat to warmer temperature. Cooling mode
ceases and compressor and fan stop.
6.
Place thermostat or system switch to OFF.
All operation should stop.
Heating Operation — Heat Pump Units — Entering
Water Temperature Above 60°F (16°C)
Room temperature must be below 85°F (29°C)
for the compressor to operate in heating mode on
Water Source Console Units with unit-mounted
controllers.
1.
Place thermostat or system switch to HEAT position.
2.
Adjust thermostat to warmer temperature setting until
compressor and fan start running. Warm air will
begin to
fl
ow from unit.
3.
After unit starts running and space warms, adjust
thermostat to cooler temperature until fan and
compressor turn off.
4.
For warmer room temperature, adjust thermostat
to warmer temperature setting turning fan, and
compressor back on.
5.
If cooler room temperature is desired, adjust
thermostat to cooler temperature setting. Heating
mode ceases and compressor and fan will stop.
6.
Place thermostat or system switch in OFF position.
All operation should stop.
The Right Fit for Comfort
17
Made in USA