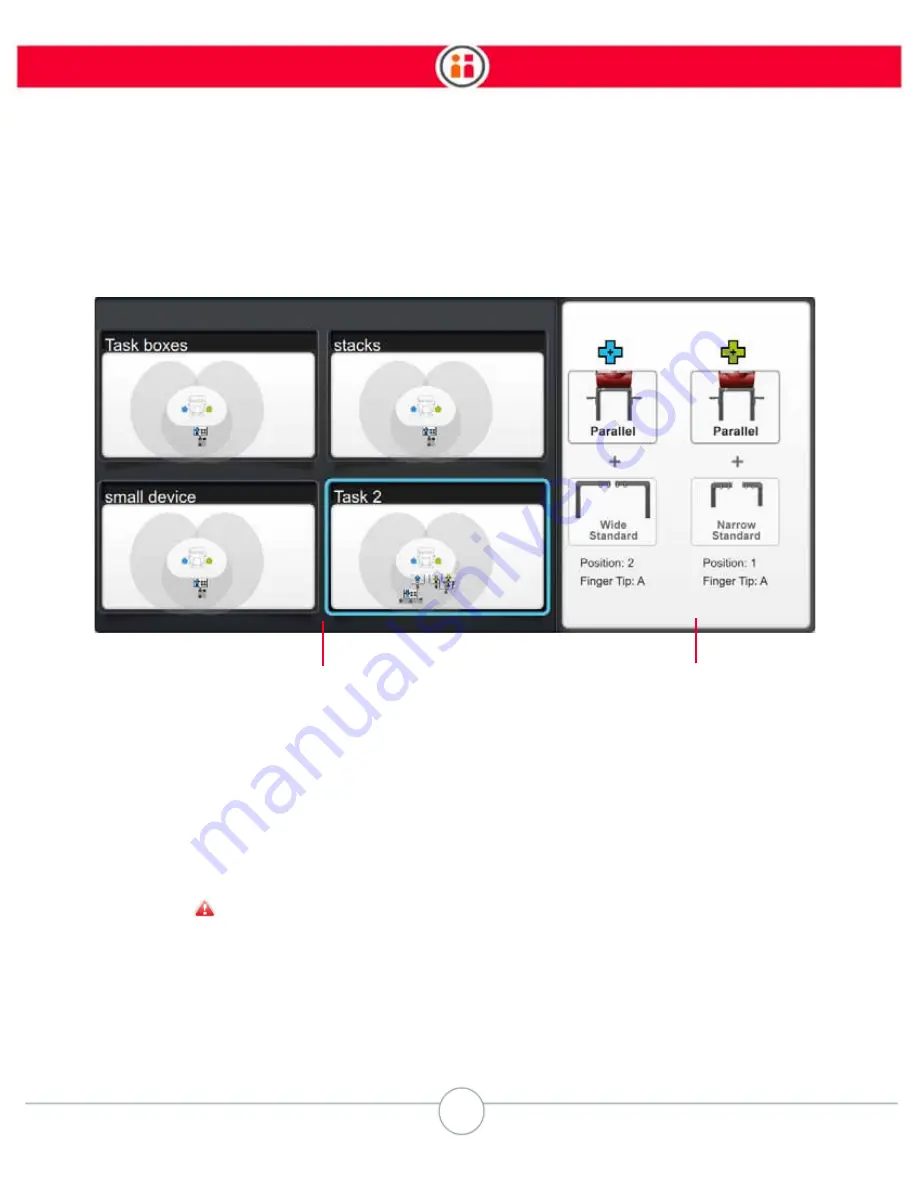
33
Intera 3.2
Training and Managing Tasks
Task Gallery
The Task Gallery is accessible from the main screen, when you select the Tasks button from the
button bar. Use the task gallery to view the details of and select, copy, delete a trained task. You
can also delete all the tasks on the robot from here.
1. Displays a visual list of all saved tasks, each with the name of the task and a
small preview image of the task map.
Note:
If a task name exceeds 21 characters, only the first thirteen and last thirteen
characters of the name, separated by ellipses, will appear. On the Task Map, the task
name will trail off on either side.
2. Displays details about the selected task.
•
Gripper specifics
- This symbol indicates a mismatch between the installed gripper and
the one used in the viewed task.
Note:
The task gallery cannot be empty. If you delete all tasks, an empty task is created
automatically.
1
2