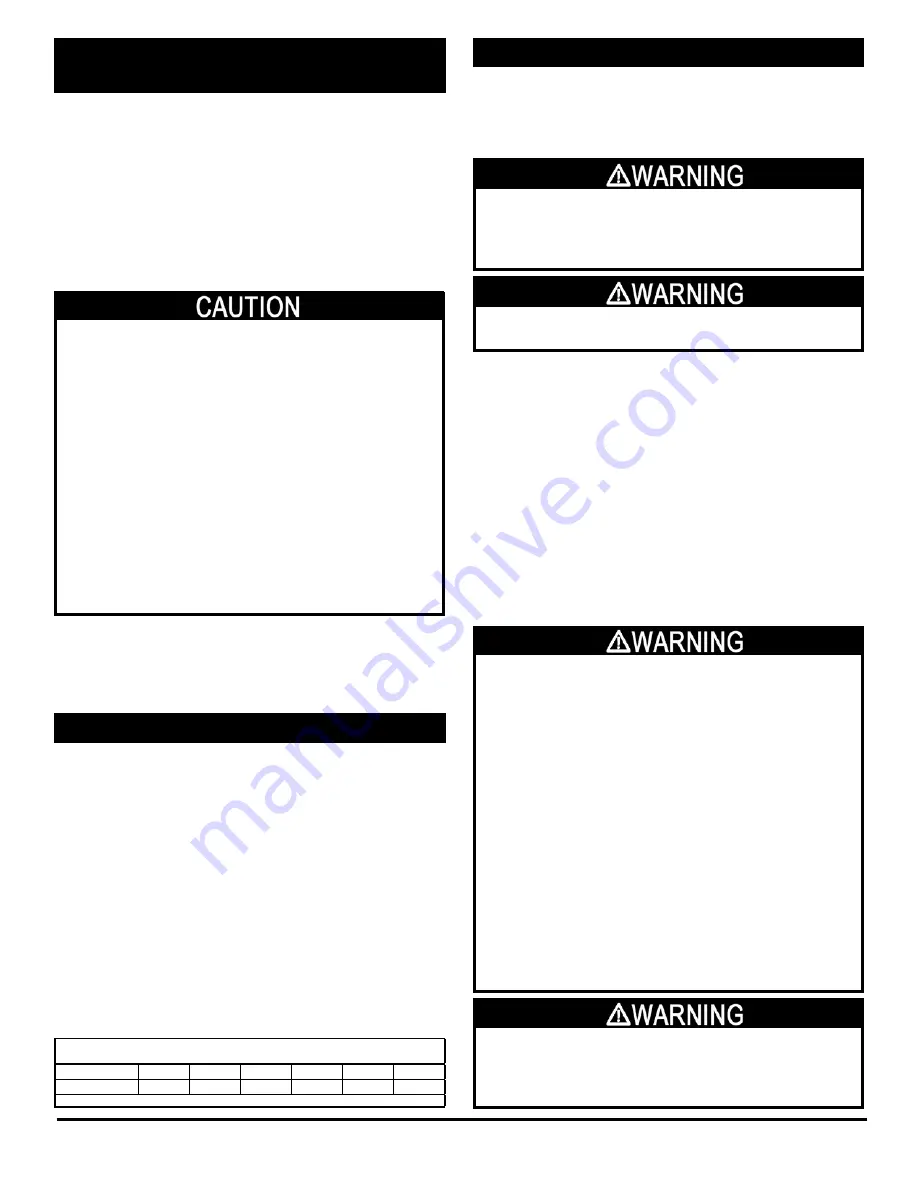
HE4XRT
Due to continuing product development, specifications are subject to change without notice.
© 2012 RenewAire LLC
134775_005 HE4XRTMan_Jan12.indd Revised 01/2012 www.renewaire.com
Page 8
OBSERVE THESE LIMITS TO WIRE LENGTH AND GAUGE,
in order to ensure reliable operation of the control system.
Wire Gauge
#22
#20
#18
#16
#14
#12
Circuit Length
100’
150’
250’
400’
700’
1000’
“Circuit Length” is distance from ERV to Control Device.
How to Reset the 24VAC Circuit Breaker
If the transformer is subjected to an excessive load or a short
circuit, the circuit breaker will trip to prevent the failure of the
transformer. When it trips the circuit breaker’s button pops up.
Shut off the primary-side power to the unit, and remove the
excessive load or the short. The circuit breaker can be reset
about fifteen seconds after it trips by pressing in the button.
NOTE:
INSTALLING CONTRACTOR:
If primary-side voltage is 230VAC, move black primary-side lead
from transformer’s “208V” terminal to the transformer’s terminal
marked “240V” (“230V” in some units).
Do not move the black primary-side lead that is connected to the
transformer’s “COM” terminal.
Limits of Power Output
If limits on wire gauge and length are observed, you may connect
control devices that draw up to 8VA to the blue and red wires.
More than one device can be connected as long as total steady-
state load does not exceed 8VA.
This ERV is provided with a Class II 24VAC power supply system that
operates the unit’s contactor(s) for EV450 and HE1X. The ERV’s
24VAC Power Supply can also be used to power the externally-
installed controls system: up to 8VA of power is available.
The unit’s power supply system includes isolation relay(s) so you
can use external controls whose contact ratings are as low as 50mA
(1.2VA). Also, it is possible to operate the isolation relays with 24VAC
power from an external source (with proper wiring connections).
A built-in circuit-breaker prevents damage to the transformer and other
low-voltage components in the event of a short-circuit or overload. In
extreme cases, the transformer itself is designed to fail safely.
24VAC Power Supply
Provided with this ERV Unit
1. Connect only to components intended for use with 24VAC
power.
2. Do not undersize the low-voltage wires connected to this
device. Observe the wire length and gauge limits indicated
in this manual.
3. Do not overload this unit’s 24VAC power supply system.
Confirm that the power requirements of devices you connect
to this power supply system do not exceed 8VA in total.
4. If an external source of 24VAC power is used to control the
unit, consult the wiring schematics and connect the external
power only to the specified terminals in order to avoid
damaging the unit or external controls. Connect only CLASS
II power to the control terminals of this unit.
5. Unit is not equipped to receive analog signals (such as
1-10vdc or 4-20mA).
6. Unit is not equipped to communicate directly with Building
Management Systems (such as BACNET, LONWORKS, etc.).
However, the unit can be controlled by powered or non-
powered contacts operated by any kind of control system.
Specifications
• Nominal Output Voltage under load: 24VAC
• Typical Output Voltage at no load:
29-31V
• Minimum contact rating
for connected control device:
(50mA (1.2VA)
• Circuit Breaker Trip Point:
3A
Motor Starters
This unit uses IEC-style motor starters to protect the motors
against overload.
IEC-style motor starters use Overload Relays to detect excessive
current and interrupt the control circuit that engages the motor’s
contactors.
Overload Relays are sized to Full Load Amp (FLA) rating of the
protected motor. The Overload Relays can be adjusted to trip
(interrupt the control circuit) at a specific setting within a range.
Overload Relays should initially be set at the FLA rating of the
motor (see Unit Rating Label). If necessary to prevent nuisance
tripping at start-up, the Relays can be adjusted to trip no higher
than 115% of the motor’s FLA rating.
For safest operation, the overload relays should also be used in
manual reset mode with trip test capability.
NOTE: As factory-wired, if one blower motor is shut down due to
overload by its Motor Starter, the other motor will also be shut down.
NOTE: Terminals 96 & 97 of the Overload Relays and terminals 14
& 13 of the Contactors are normally-open dry contacts that may
be used to signal that the contactors are closed and/or that the
Overload Relays have tripped.
DANGER OF INJURY OR DAMAGE.
The motors in this unit must not be run at an amperage
that exceeds the motor’s rated full load amps and
overload relays on the motor starters must be set at
or below motor full load amps. For safest operation,
the overload relays should also be used in hand reset
mode with trip test capability.
It is the installer’s responsibility to measure the
operating amperage of each motor. If the full load amp
rating is exceeded, the amp draw must be reduced by
substituting a smaller motor pulley or by adjusting
the variable sheave. Continue these adjustments
until the actual amperage is no more than the motor’s
faceplate full load amps.
Failure to make this adjustment may result in
unsafe motor winding temperatures or tripping of
the supplied motor starter’s overload relay motor
protection devices set at full load amps.
DANGER OF INJURY OR DAMAGE.
The relay must be set for correct FLA rating depending
on the motor horsepower. See Unit Rating Label on
motor for HP and FLA specifications.
Adhere to applicable local codes when adjusting the
dial setting of the overload relays.
The Overload Relay output contacts 95 & 96 must
remain in series with the low-voltage control circuit!
Altering this will create a hazardous situation in
which the motor is not protected against overload!