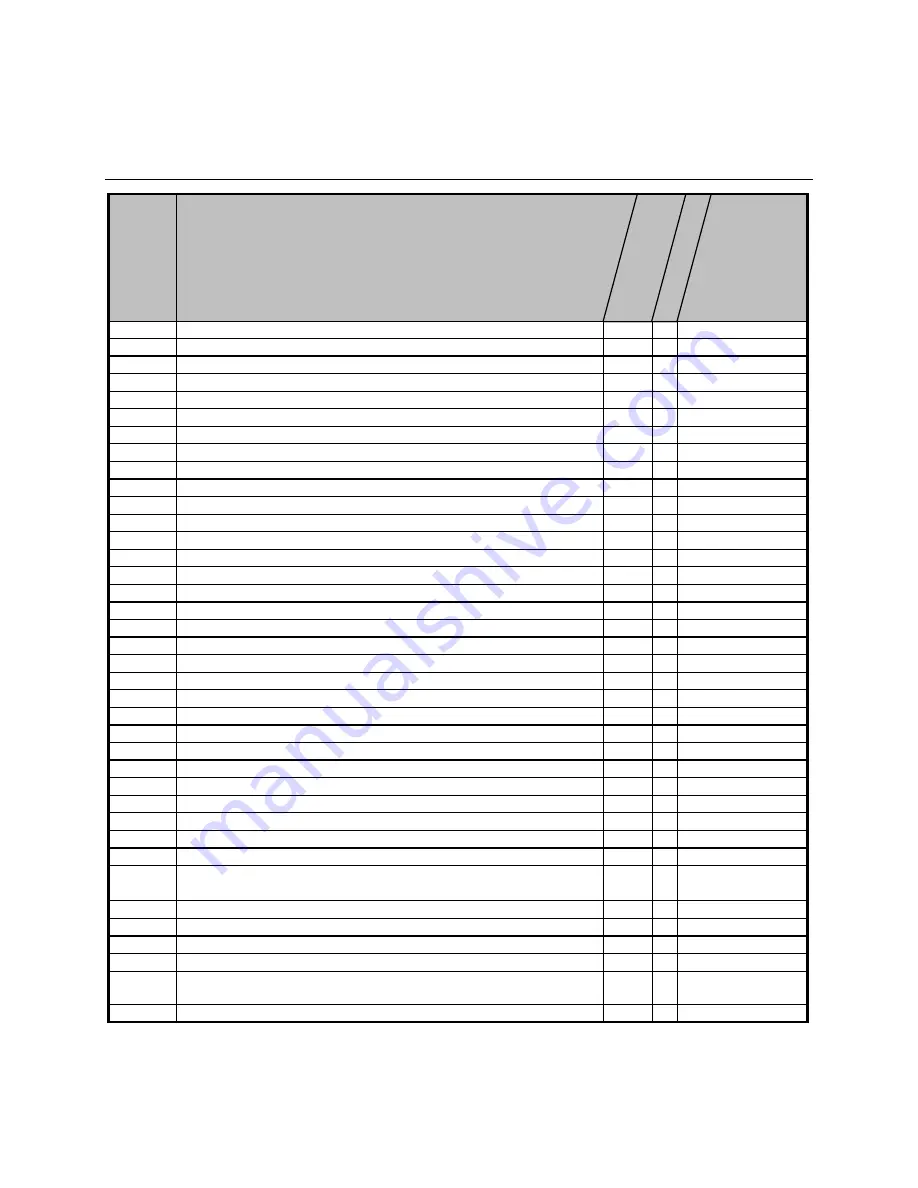
66
Maintenance
Inspection overview
Pos. Nr.: Inspection check list -
R40
ECO
Ev
er
y
4.
00
0
hr
s.
o
r
at
le
as
t o
nc
e
a
ye
ar
Ac
tiv
ity
d
on
e
Remarks
√
Switch off power supply to the boiler and close the gas valve!
1
Air box/Boiler cover
1.0.1
Remove boiler cover
1.0.2
Check boiler cover/air box sealing on wear
1.0.3
Necessary cleaning
2
Gas pipes
2.0.1
Check all gas pipes on leaks
2.0.2
Check all gas fittings on leaks
2.0.3
Check all gas pipes and parts on corrosion and damage
2.0.4
Check static and dynamic gas pressure
3
Pressure parts
3.0.1
Check fill and drain valve on its function
3.0.2
Check system pressure
(Plausibility check)
3.0.3
Check pre-pressure of expansion vessel and adjust if necessary
4
Checking parts on damage, corrosion, function and leaks:
4.0.1
Gas valve / Venturi
4 0 2
Automatic de-aerator
√
√
√
√
√
√
√
√
√
√
√
√
√
4.0.2
Automatic de-aerator
4.0.3
Hydraulic connections
4.0.4
Siphon and condensate drain
4.0.5
Ignition and ionisation block
4.0.6
OSS heat exchanger
4.0.7
Condensate tray
5
Boiler/Burner in operation without air box/boiler cover:
5.0.1
Check flame
5.0.2
If flame is not stable - check adjustments and burner
5.0.3
Commissioning O
²
/CO
²
and Ionisation current
6
Additional checks:
6.0.1
Check all parts under over-pressure
6.0.2
Check combustion air intake
6.0.3
Check gas flow
(Plausibility check)
6.0.4
Check O
²
/CO
²
6.0.5
In case of multiple units - All activities should be carried out on all units!
6.0.6
Reassemble boiler cover
7
Boiler/Burner in operation with air box/boiler cover:
7.0.1
Check function central heating
7.0.2
Check function DHW
7.0.3
Check desired temperature and actual flow temperature (Plausibility
check)
7.0.4
Write down running hours from MMI and reset counter
√
√
√
√
√
√
√
√
√
√
√
√
√
√
√
√
√
√
√
Änderungen vorbehalten.
Stand: 18.04.2013