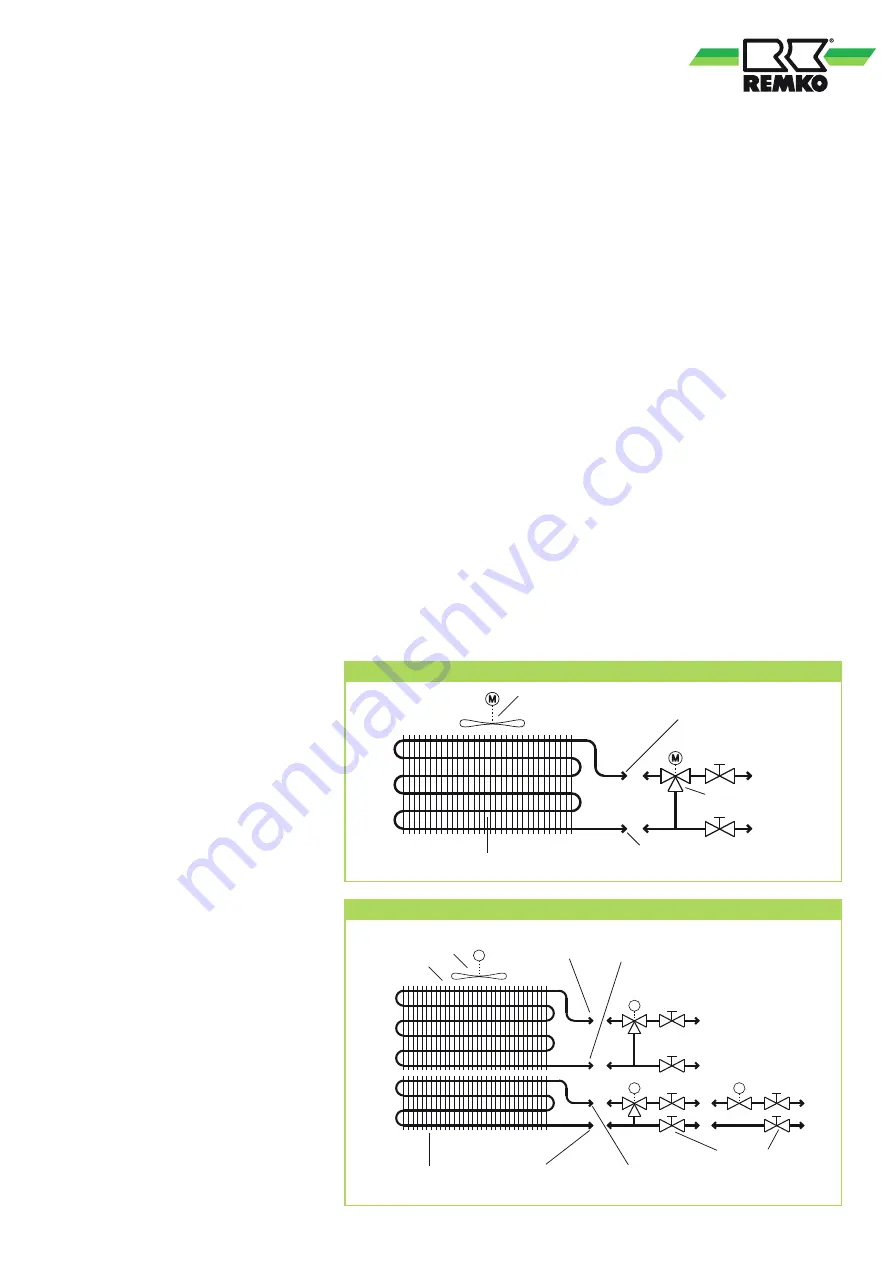
Guarantee
As a prerequisite for any
guarantee claims to be considered,
it is essential that the ordering party
or its representative complete and
return the "Certificate of warranty"
to REMKO GmbH & Co. KG at the
time when the units are purchased
and commissioned.
The guarantee conditions are
listed in the "General terms and
conditions". Furthermore, only
the parties to a contract can
conclude special agreements
beyond these conditions.
In this case, contact your
contractual partner in the first
instance.
Unit description
In cooling mode the unit (chilled
water outlet) extracts the heat
from the interior room to be
cooled into the fin register
and passes it on to the cold
operating medium - water or
a mix of water and glycol - within
a closed medium cycle. As a result
of the heat exchange, the medium
heats up and the emergent
air cools the room down.
In heating mode, a warm
operating medium warms
the room to be heated.
The medium cools down as a result
of the heat exchange.
A valve assembly, which routes
the operating medium through
the register (energy is given up)
or past the resister (energy is
not given up), is used to control
the cooling or heating capacity.
The unit is designed for use
indoors in the lower wall area
(vertical installation) and for ceiling
installation (horizontal installation).
Operation is either individually
or in groups using a room
temperature controller or via
the building management system.
The unit consists of a fin heat
exchanger, circulation fan,
controller and two condensate
trays for horizontal and vertical
installation.
The available accessories
include room temperature
controllers for installation in
the unit or on the wall, heating
coil for connection to a 4-wire
system, valve assembly cooling,
fan modules, air inlet plinth,
duct parts, grille and condensate
pumps.
M
M
Diagram of a 2-conductor system medium cycle
Medium inlet
connection
Valve assembly
(accessories)
Medium outlet
connection
Recirculating fan
Cooling register
Diagram of a 4-conductor system medium cycle (with heating register)
M
M
M
M
Cooling register connection
Recirculating fan
Heating register
(accessory)
Medium inlet Medium outlet
Heating register connection
Medium inlet Medium outlet
Cooling
register
3-way or 2-way
valve assembly
heating (accessory)
Cooling valve
assembly (accessory)
Intended use
Depending on the model and
the equipment, the units are only
intended to be used as a cold
water drain to cool or warm
the operating medium water
or a water-glycol mixture within
a closed medium cycle.
Any different or additional
use is a non-intended use.
The manufacturer / supplier
assumes no liability for damages
arising from non-intended use.
The user bears the sole risk in such
cases.
Using the equipment as
intended also includes working
in accordance with the operating
manual and installation
instructions and complying with
the maintenance requirements.
5