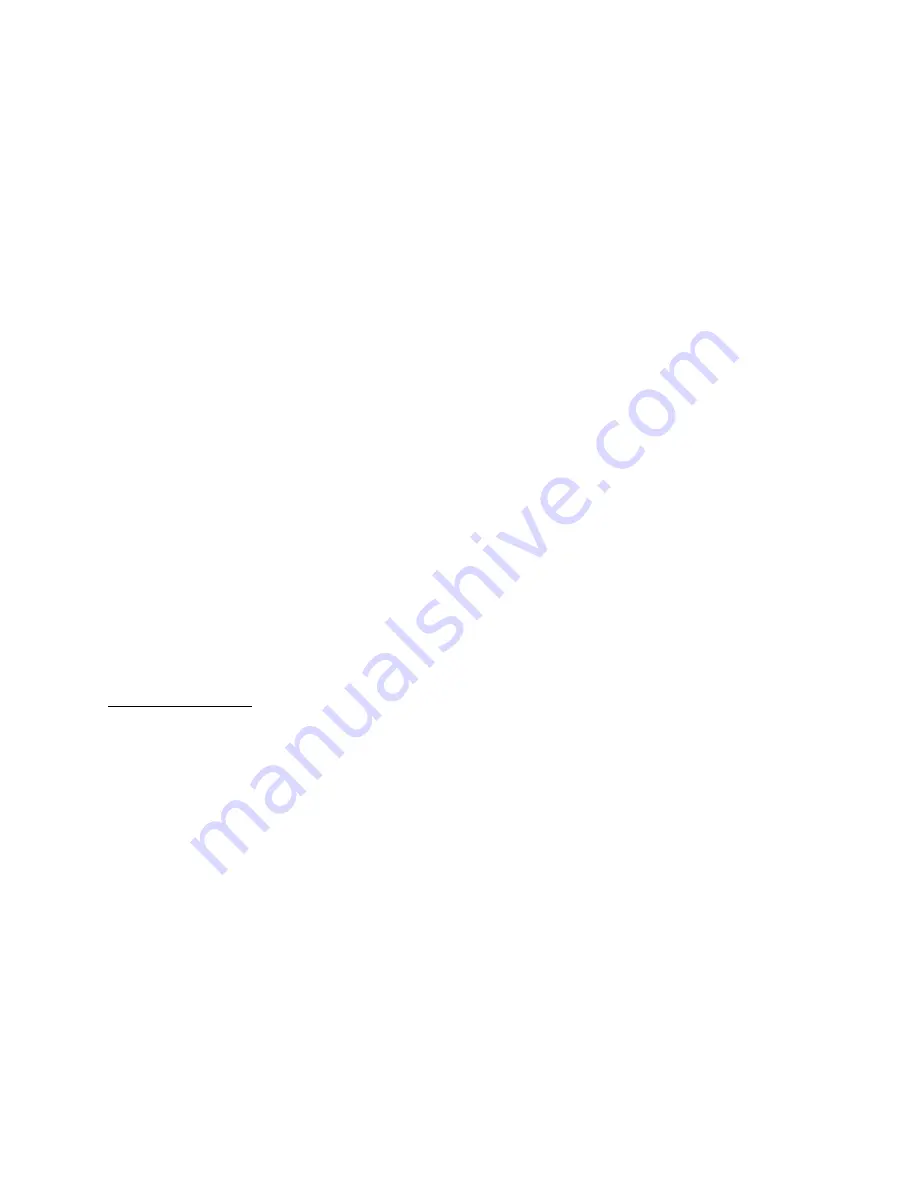
21
91626
b.
VOM on RX100,000 scale - no continuity - replace capacitor (open).
E. Overload (TP) 1 & 3 - no continuity - replace TP (open).
F.
Compressor C & shell - continuity replace compressor (grounded motor).
G. Check the continuity of the wires removed and reconnect to the proper terminals.
H. If all of the above tests prove satisfactory and compressor still fails to operate properly, change the
start relay as the new relay will eliminate and faulty electrical characteristics, such as improper pick-up
or drop-out which cannot be determined by the above tests. If the new relay fails to correct the difficul-
ty, the compressor shall be considered to be inoperative because of internal defects and must be re-
placed.
To replace the compressor, the following items are needed: vacuum pump, refrigeration manifold with gauges,
charging cylinder, brazing equipment and various hand tools. The procedure is as follows:
1. Disconnect electrical power to the unit and remove wires from the compressor terminals.
2. Release refrigerant charge from the system.
3. Unbraze discharge (next to service port) and suction lines.
4. remove mounting bolts (4) and hardware from old compressor.
5. Install new compressor following the above steps in reverse order.
6. Evacuate and recharge system to nameplate specifications.
7. Run icemaker and perform the following items:
A. Check that suction/discharge pressures are in the normal operating ranges. Nominal discharge pres-
sure 300 PSIG and suction pressure 17-35 PSIG at 70
°
F ambient air temperature and 50
°
F water
temperature.
B. Check ice production capacity (see ice thickness adjustment section for procedure).
Hot Gas Valve (HGV)
There are three situations to monitor for determining the proper functioning of the HGV. Install suction and dis-
charge pressure gauges on the access ports removing the front, left and right side panels. First, observe the
suction/discharge pressures during the icemaking cycle. the suction pressure (greater than 40 PSIG) range and
a low discharge pressure (less than 115 PSIG) indicate a leaking valve set problem and the HGV must be re-
placed. Secondly, observe the suction pressure during the hot gas portion of the harvest cycle. The minimum
suction pressure is 70 PSIG; pressures less then this indicate the HGV is not operating properly and must be
replaced. The third situation to analyze is the valve coil. If there is voltage but and audible “click”is not heard at
the valve, replace the HGV (defective coil - valve not opening). /The minimum suction pressure would also not
be attained in this third case.
To replace the HGV, the following equipment is needed: vacuum pump, refrigeration manifold with gauges,
charging cylinder, brazing equipment and various hand tools.
The replacement procedure is as follows:
1. Disconnect electrical power to the unit and the leads to the valve.
2. Release the refrigerant charge from the system.
3. Unbraze the line connections at the valve. Remove the nut that attaches the valve to the mounting bracket.
4. Install new valve.
5. Evacuate and recharge system to name plate specifications.