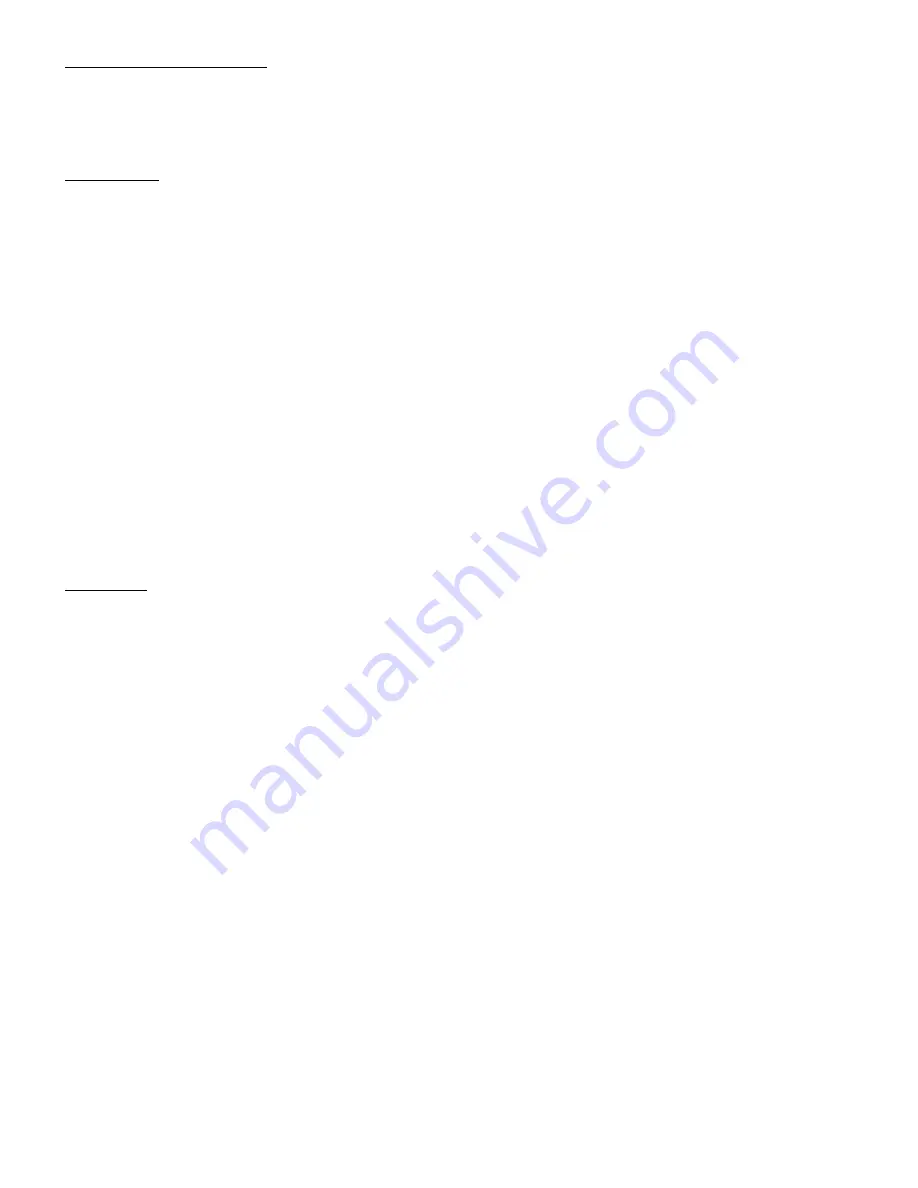
20
91626
Expansion Valve TXV (Cont’d)
4. Observe that the unit functions normally in both the icemaking and harvest cycle; specifically that suction
and discharge pressures are in the range of 37-17 PSIG and 200-280 PSIG.
water fill valve
The water fill valve is located on the condensing unit assembly base, behind the compressor. To check for prop-
er operation, put the “stop/run”switch in the “stop”position. Depress the fill switch and hold. Water should over-
flow out the evaporator and to the overflow tube and collector drain. If water doesn’t flow out the evaporator and
to the overflow tube and collector drain. If water doesn’t overflow and the water supply has been checked, then
the fill valve is defective.
To replace the fill valve:
1. Disconnect electrical power to the unit.
2. Disconnect the electrical wires from the solenoid.
3. Remove the water outlet line from the valve.
4. Remove the two (2) screws securing the valve to the condensing unit assembly base. Remove the valve.
5. With the valve “free”, remove the inlet fitting assembly (garden hose).
6. Install the inlet fitting assembly on the new valve. Repeat the above procedure in the reverse order to com-
plete installation of the fill valve.
Compressor
The compressor can exhibit basically two types of malfunctions. It will run but the refrigeration system produces
little or no ice. In this case, check the suction and discharge pressures. A high suction pressure (greater than
the normal range of 17-35 PSIG) and low discharge pressure (less than the norma range of 200-280 PSIG) indi-
cates an internal valve problem and loss if compression. The second type of failure is characterized b y the fact
that the compressor will not run but there is voltage at the terminals. The cause is a defective motor (check for
open or grounded windings).
In the case where the compressor is not operating, the electrical system can be checked as follows (a VOM
type instrument is required):
1. Remove the front panel and the compressor electric box cover.
2. Put the “stop/run”switch in the “run”position.
3. Verify that there is voltage at the compressor.
4. Disconnect electrical power to the unit.
5. disconnect wires so that continuity can be checked on the compressor electrical components.
6. Check continuity across the following:
A. Relay coil: If there is none, replace relay.
B. Compressor C & S - no continuity - replace compressor (open start winding).
C. Compressor C & R - no continuity - replace compressor (open run winding).
D. Start capacitor terminals
a.
VOM on RX1 scale - continuity replace capacitor (shorted).