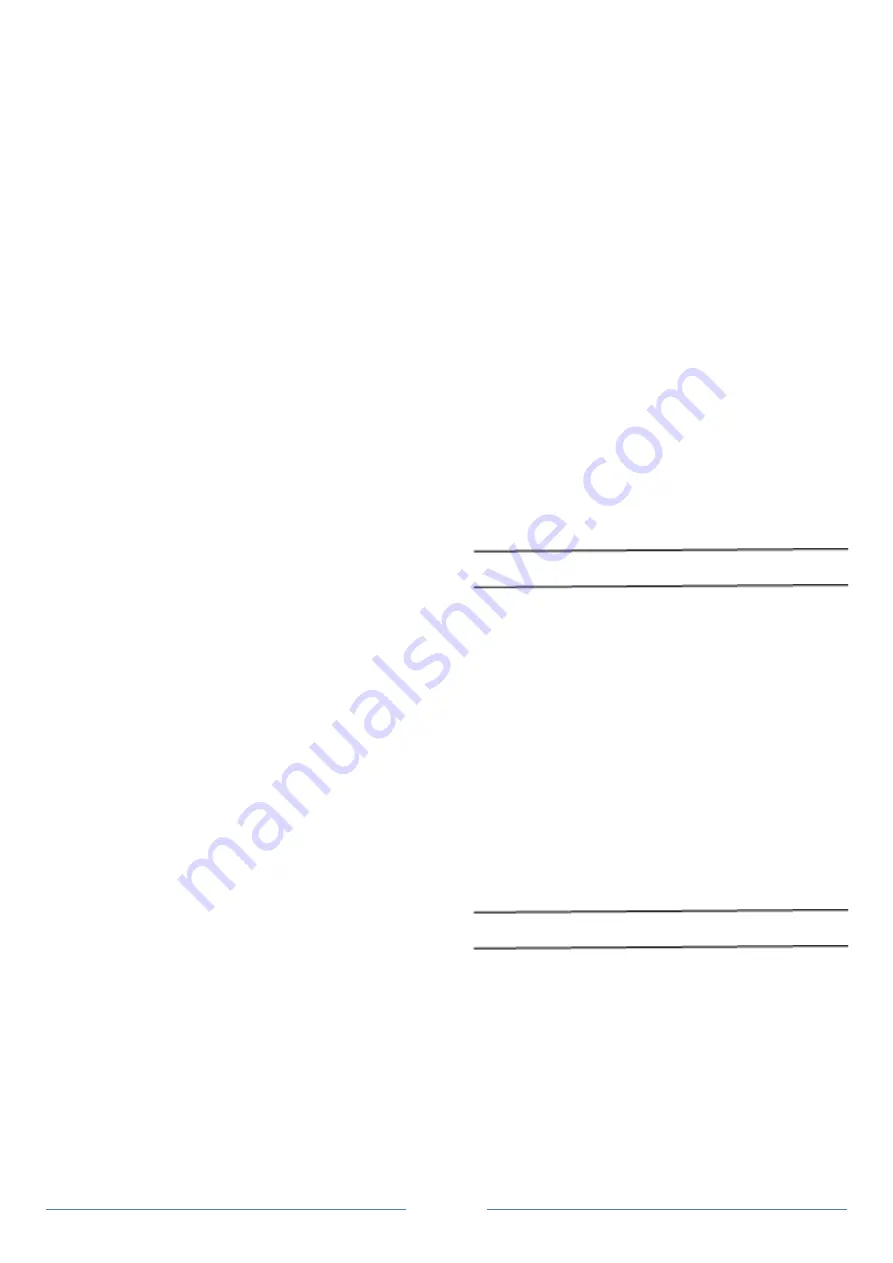
Page 76
To remove the carburettor
1.
Remove the air cleaner from the air intake and the fuel pipe
from the inlet boss on the float chamber
2.
Disconnect the throttle operating arm from the throttle
lever and disconnect the choke cable by releasing the outer
casing clip and slackening the swivel in the choke lever.
3.
Pull off the vacuum advance pipe from the tube protruding
from the carburettor fixing flange. (If fitted – Not all Rebels
have this feature).
4.
Unscrew the two 5/16” UNF nuts and lock washers securing
the carburettor to the inlet manifold.
To dismantle the carburettor (Figure 4)
1.
Unscrew five screws and spring washers retaining the float
chamber cover and gasket to the lower body.
2.
Inside the float chamber cover is the needle valve which
controls the entry of fuel to the float chamber. This is a
screw fit.
3.
The hook shaped pump jet, which consists of a hexagonal
base and an “O” ring seal, sits on the lower body and is
easily lifted out. Adjacent to the pump jet is the air
correction jet, which has the emulsion tube attached and is
a screw fit. The slow running jet, with gauze sheath, can be
lifted out.
4.
The casting which forms the main discharge assembly can
be seen in the throat of the carburettor and is located by
means of a grub screw.
On no account try to remove or
loosen this screw.
5.
To gain access to the main jet, lift out the plastic float
complete with its pivot pin and unscrew the hexagon plug,
with plain washer, located in the base of the float chamber.
Through the plug aperture, unscrew the main jet using a
suitable sized screwdriver.
6.
Inspection of the accelerator pump diaphragm, spring and
passages can be achieved by laying the carburettor on its
side with the pump uppermost. Remove the four fixing
screws, whilst holding the cover in position. Now carefully
swing away the cover on the operating rod, taking care to
release the spring tension prior to final removal. On
reassembly, first position the spring in the main casting,
followed by the diaphragm which is fitted with a spigoted
centre portion outwards (towards the cover). When
refitting the pump cover ensure that the spring is correctly
located in the centre of the diaphragm before refitting the
fixing screws.
7.
To check the economy device, remove the three retaining
screws and lift off the assembly, including gasket. Behind
the gasket is situated the economy jet which can be
removed using a suitable screwdriver. Access to the
economy spring and diaphragm can be gained by removing
the two screws of the sub-assembly, holding the cover and
carefully releasing the spring tension before lifting off.
When replacing the diaphragm, spring and cover, first
locate the diaphragm on the body, place the spring in the
cover and bring the two parts together with the soring
locating in the centre cup of the diaphragm. To refit the
assembly, locate the gasket, then position the assembly in
the main body of the carburettor and replace the three
screws.
To reassemble the carburettor
Before reassembly of the unit, ensure that all jets are correctly
replaced.
1.
First lower the base of the plastic float into the float
chamber and locate the pivot pin in the rcess of the body
flange.
2.
Place the gasket in position and, holding the choke cam in
the closed position, locate the upper body to the lower
body and secure with the five fixing screws, Tighten evenly
and firmly from the centre outwards.
To refit
Follow the reverse procedure for removing the carburettor.
Servicing
When investigating faulty carburation, first check that the correct jet
sizes are fitted (see specification chart at the end of this section). It is
also imperative to ensure that the electrical side, particularly ignition
settings, contact breaker gap and spark plugs are operating correctly
and they the tappets are adjusted to the right clearances. Faults in any
of these components will upset the performance and can be wrongly
diagnosed as “carburettor problems”.
Difficult starting (cold engine)
Ensure that there is petrol in the float chamber, for sediment or gum
can cause the float needle to stick in the closed position, preventing
the entry of fuel. The fuel in the float chamber tends to evaporate as
the engine cools after running. Check also that the fuel pump is
operational.
If a sticking needle is suspected, remove the upper body of the
carburettor and operate the needle with a finger. A tendency for the
valve to stick in the closed position can usually be overcome by rinsing
it in methylated spirit. This will dissolve any gum deposits and wash
off sediments.
Ensure that the choke flap is completely closed when the choke knob
is pulled fully out. Maladjustment or fault here could cause the choke
to remain partially open which will lead to difficulty in starting from
cold. Also check that the throttle screw is correctly adjusted.
Difficult starting (hot engine)
First check that the needle valve is of the correct size. Having cleaned
the assembly, replace it with the correct washer and ensure that it is
screwed tightly in position.
Examine the float for damage and see that it moves freely on the pivot
pin. If petrol floods into the manifold after switching off the engine it
is possible that there is excessive pressure from the fuel pump.
A additional washer under the needle valve may be effective in
preventing flooding and could be tried prior to replacing the pump. A
flooded engine can be started by holding the throttle fully open whilst
cranking the engine
Summary of Contents for Rebel 700 1967
Page 8: ...Page 8 Section A Chassis Frame ...
Page 9: ...Page 9 ...
Page 14: ...Page 14 ...
Page 19: ...Page 19 ...
Page 24: ...Page 24 Section F Engine ...
Page 41: ...Page 41 Section G Early Models prior to Chassis No 941001 3 Synchro Gearbox ...
Page 43: ...Page 43 ...
Page 47: ...Page 47 ...
Page 52: ...Page 52 ...
Page 55: ...Page 55 ...
Page 57: ...Page 57 Section K Rear Axle ...
Page 68: ...Page 68 ...
Page 72: ...Page 72 Section P Fuel System ...
Page 75: ...Page 75 ...
Page 84: ...Page 84 ...
Page 85: ...Page 85 ...
Page 89: ...Page 89 Section R Interior ...
Page 94: ...Page 94 ...
Page 95: ...Page 95 ...
Page 105: ...Page 105 ...
Page 107: ...Page 107 ...
Page 109: ...Page 109 ...
Page 110: ...Page 110 ...
Page 112: ...Page 112 ...
Page 113: ...Page 113 ...