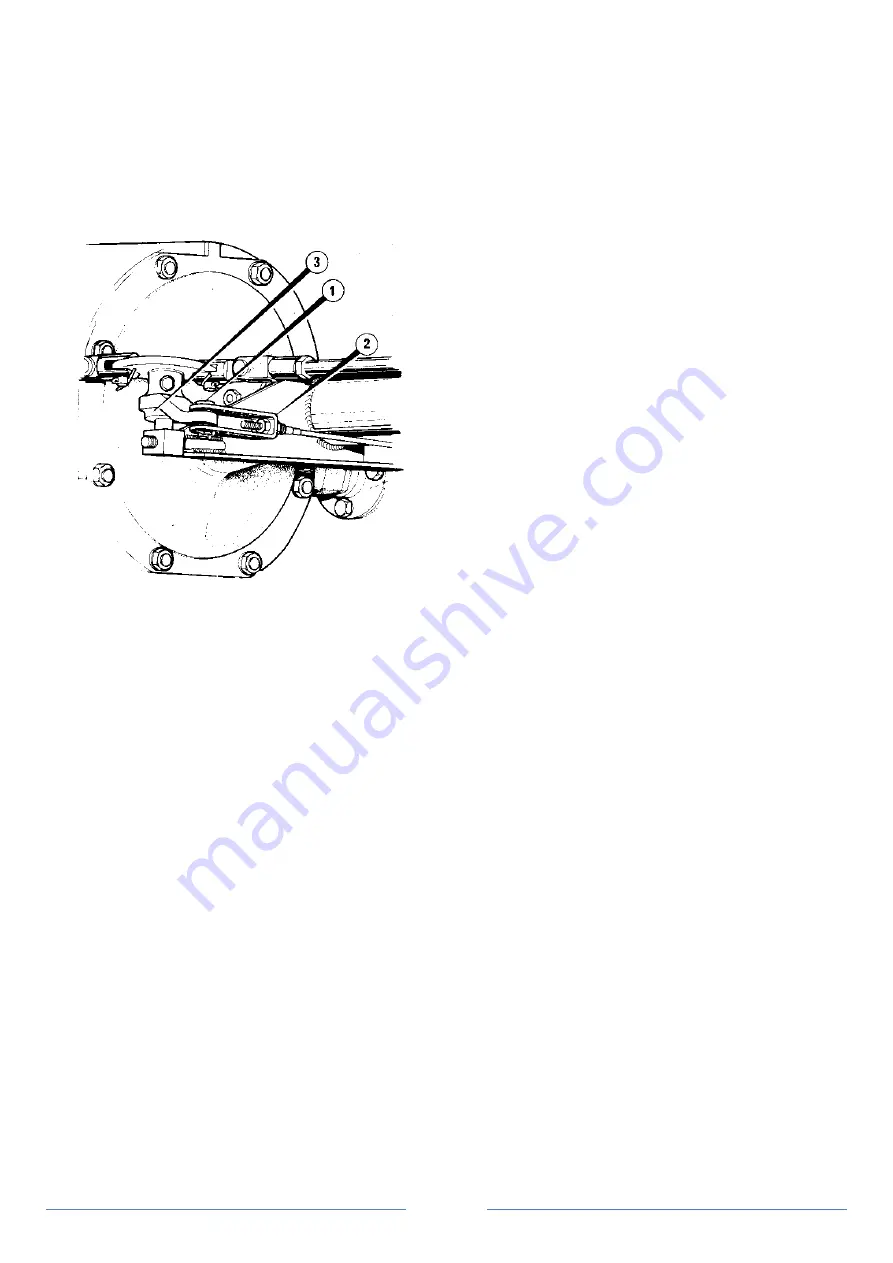
Page 65
Handbrake adjustment
Before adjusting the handbrake cable, ensure that the rear brakes are
correctly adjusted.
1.
Ensure that the handbrake lever is in the fully "
off
" position
and the cable is slack.
2.
Remove the split pin from the clevis pin (
Figure 3
) at the
rear of the brake cable. Adjustment is achieved by means of the clevis
on the end of the adjuster screw. Adjust until the clevis pin slides
easily in to the clevis and balance lever.
Figure 3 Handbrake compensator
1.
Clevis pin
2.
Clevis
3.
Balance lever
Handbrake lubrication
The handbrake cable is greased on assembly but the cable inner
should be greased by means of the grease nipple (where fitted). In
adverse weather conditions especially it is wise to grease the exposed
sections of cable. The handbrake compensator must also be greased
periodically.
The hydraulic system (Figure 6)
The hydraulic brake master cylinder is situated below the right-hand
driver's foot well. Access to the reservoir is achieved after lifting the
carpet and removing the access cover plate. Before checking or
replenishing the system, wipe the sides of the reservoir to prevent dirt
entering the system when the cap is unscrewed. Top -up the reservoir
as and when necessary using a recommended hydraulic fluid - see
Lubrication
chart page 13. Do not use other fluids, otherwise the seals
may be damaged causing brake failure. Ensure that the breather hole
in the filler cap is clear before replacing the cap.
Bleeding the hydraulic system
Bleeding - elimination of air from the hydraulic system, should only be
necessary when any part has been disconnected or if the fluid level in
the master cylinder has been allowed to fall so low that air has been
drawn in to the system. This is usually indicated by the need to
"pump" the brake pedal to obtain efficient braking. The system must
then be bled.
The apparatus needed to bleed the hydraulic system consists of a
clean glass jar containing some brake fluid and a rubber tube of
sufficiently small diameter to fit tightly over a bleed nipple. An
assistant will be required to pump the brake pedal.
1.
Locate the bleed nipple on the nearside rear wheel brake
back plate (
Figure 2
). Remove the dust cover and fit the rubber tube
over the nipple. Immerse the other end of the tube in the brake fluid
in the glass jar.
2.
Unscrew the nipple about a quarter of a turn.
3.
Pump the brake pedal. The operation of the brake pedal is
important. The pedal must be pushed down firmly through the full
stroke, followed by three short rapid strokes and the pedal should be
allowed to return quickly to its stop with the foot right off.
4.
Repeat this operation until the fluid expelled is free from air
bubbles. Tighten the bleed nipple during a down stroke of the brake
pedal.
5.
Remove the bleed tube from the nipple and replace the
dust cover. The above procedure must be carried out on all wheels in
the order: Nearside rear - offside rear - nearside front and offside
front.
Always check that the stroke of the brake pedal is not impeded by
floor mats or other obstructions.
Note:
Throughout the above procedure, keep the master cylinder
topped up with fresh clean brake fluid. Never re-use old fluid.
Scrupulous cleanliness must be observed at all times.
6.
Check the operation of the brakes on road test.
Important:
at 36,000 miles or three years the fluid should be changed.
Brake fluid is hygroscopic so will absorb moisture over time, lowering
the boiling point leading to fade or even failure of the brakes.
Front brakes - fitting new shoes (Figure 4)
Always fit Reliant replacement shoes, including a new set of return
springs.
To remove
1.
Jack up the vehicle and place on suitable stands.
2.
Remove the front road wheel, the countersunk screw and
the brake drum. It might be necessary to back off the brake adjusters
to enable the drum to be withdrawn.
3.
Remove the steady post pins (if fitted) and, using a large
screwdriver, prise both the shoes from the grooves in the wheel
cylinder pistons.
4.
Remove both shoes and return springs.
Note: To prevent loss of fluid, slip a rubber band over each wheel
cylinder to hold the pistons in place.
5
.
Clean the back plate using a vacuum cleaner or wipe out
with a damp cloth. Remove all traces of dust. The old-established
practice of blowing off with an air line is
NOT
recommended as it
represents a potential health hazard.
6.
Check the adjusters for correct operation and lubricate. Use
only a proprietary brake grease.
To replace
1.
Attach new return springs to the new shoes, ensuring the
springs are correctly located and positioned such as they are between
the shoe webs and the brake plate on assembly (Figure 4)
Note:
Try not to touch the lining material and avoid contact with
grease and other contaminants.
2.
Remove the rubber bands from the wheel cylinders.
3.
Place the shoes in place with the springs attached, against
the back plate locating the tongues of the shoes in to the grooves of
the wheel cylinder bodies.
4.
Locate a screwdriver under the web of one shoe against the
back plate and lever the shoe over the adjuster spindle and into the
wheel cylinder piston groove. Refit the steady posts.
5.
Repeat for the remaining brake shoe.
Summary of Contents for Rebel 700 1967
Page 8: ...Page 8 Section A Chassis Frame ...
Page 9: ...Page 9 ...
Page 14: ...Page 14 ...
Page 19: ...Page 19 ...
Page 24: ...Page 24 Section F Engine ...
Page 41: ...Page 41 Section G Early Models prior to Chassis No 941001 3 Synchro Gearbox ...
Page 43: ...Page 43 ...
Page 47: ...Page 47 ...
Page 52: ...Page 52 ...
Page 55: ...Page 55 ...
Page 57: ...Page 57 Section K Rear Axle ...
Page 68: ...Page 68 ...
Page 72: ...Page 72 Section P Fuel System ...
Page 75: ...Page 75 ...
Page 84: ...Page 84 ...
Page 85: ...Page 85 ...
Page 89: ...Page 89 Section R Interior ...
Page 94: ...Page 94 ...
Page 95: ...Page 95 ...
Page 105: ...Page 105 ...
Page 107: ...Page 107 ...
Page 109: ...Page 109 ...
Page 110: ...Page 110 ...
Page 112: ...Page 112 ...
Page 113: ...Page 113 ...