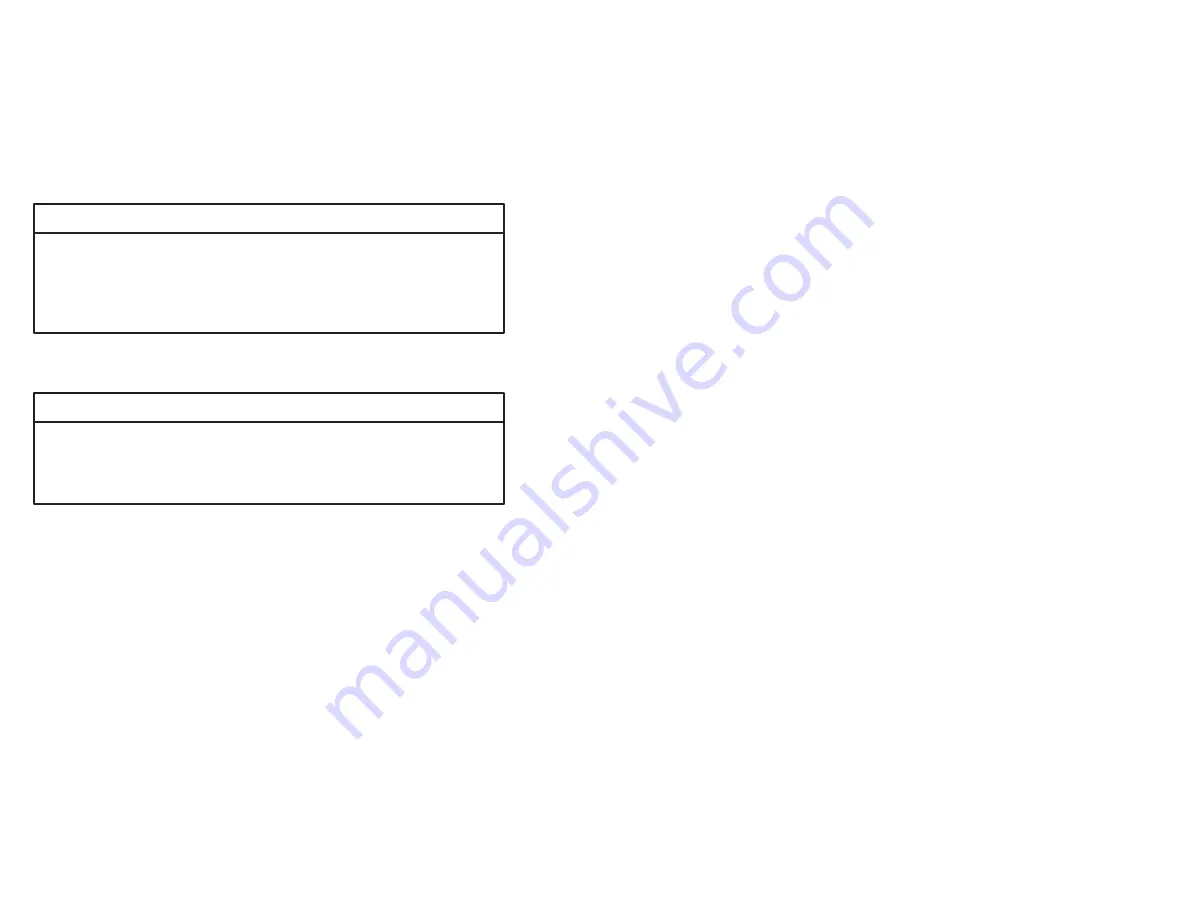
6Ć2
If the Processor in the master rack fails or issues a BOARD RESET
command (clears all outputs in the rack), the entire image in the
master's dual port memory will be cleared. All Remote I/O slave
drops will detect that the master has failed. Their response to this will
be to clear all AutoMax module outputs in remote drops. The remote
drops will then wait for the master to reĆestablish communication.
The failure of a slave drop to communicate with the master can result
from a bus error or failure of the rack power supply or backplane. If a
Multibus slave drop fails, the Remote I/O module in the slave rack will
issue a BOARD RESET command. This command will clear all
outputs in the slave rack.
WARNING
FOREIGNI/O MODULES (NONĆRELIANCE MODULES) DO NOTRESPONDTOTHE
BOARD RESET COMMAND. THEREFORE, IF FOREIGN I/O MODULES ARE USED
IN AN AUTOMAX SYSTEM AND IT IS REQUIRED THAT THEIR OUTPUTS BE SET
TO A KNOWN STATE WHEN A FAILURE OCCURS, OTHER METHODS MUST BE
EMPLOYED TO SATISFY THIS REQUIREMENT. FAILURE TO OBSERVE THESE
PRECAUTIONS COULD RESULT IN BODILY INJURY.
If a Remote I/O Head slave drop fails, the Remote I/O Head will
attempt to clear all outputs at that drop. In this situation, the outputs
connected to the rails or Local Heads may not be cleared.
WARNING
IN APPLICATIONS WHERE IT IS IMPERATIVE THAT OUTPUT DEVICES BE
DISABLED OR DEĆENERGIZED WHEN THE DROP FAILS, POWER TO THE
OUTPUT DEVICES SHOULD BE ROUTED THROUGH THE READY RELAY ON THE
REMOTE I/O HEAD OR REMOTE DRIVE INTERFACE HEAD POWER SUPPLY.
FAILURE TO OBSERVE THIS PRECAUTION COULD RESULT IN BODILY INJURY.
If a Shark slave drop fails, the Shark Interface module in the slave
rack will issue a reset I/O command. This command will clear all
outputs in the slave rack.
When the master recognizes that a slave drop (Multibus, Shark,
Remote Drive Interface Head, or Remote I/O Head) has failed, it will
clear all inputs in its dual port memory and the status bit indicating
the slave drop's status will be turned off for a minimum of 120
milliseconds.
Monitoring registers 15Ć18 in the drop 0 area will indicate network
integrity. The master logs the error parameters (RECEIVE TIMEOUTS,
CRC, OVERRUN, and ABORT) for the entire network. A few errors
may accumulate over a period of time, such as a few days, but when
these parameter values increase consistently over a short period of
time, there is a problem with the integrity. If this occurs, monitor the
error parameters of each network drop using the Status command
(except for Shark racks) to isolate the problem.
Use the following general procedure to isolate the cause of a Remote
I/O network failure:
Step 1.
Verify that the drop number of each slave module is
unique and the thumbwheel switches are set correctly.
The thumbwheel switches are read only once at power up.
If any changes have been made to the thumbwheel
Summary of Contents for AutoMax 57C328
Page 1: ......
Page 7: ...VI Figure 5 1 Drop Status Monitoring 5 1 Figure 6 1 AutoMax Rail Fault LED Codes 6 5...
Page 14: ...fafadfdfdasfdsfdsdsdfdsfdsfdsfsdfdsa afdfdsfdsfdfdsfdsfsadfda asfdfaddfdd...
Page 16: ......
Page 47: ...4 0 4 0 0 2 0 0 0 0 0 0 2 2 0 0 0 0 0 1 0 0 3 0 0 4 1 2 0 0 0 2 1 2 2 0 4 0 0 0 0 0...
Page 70: ......
Page 84: ...fafadfdfdasfdsfdsdsdfdsfdsfdsfsdfdsa afdfdsfdsfdfdsfdsfsadfda asfdfaddfdd...
Page 97: ...Appendix B Block Diagrams Remote I O Communications Module M N 57C416 0 3...
Page 99: ...Appendix B Remote I O Head M N 57C328 and M N 57C330...
Page 100: ...Appendix B Remote Drive Interface Head M N 57C329...
Page 102: ...fafadfdfdasfdsfdsdsdfdsfdsfdsfsdfdsa afdfdsfdsfdfdsfdsfsadfda asfdfaddfdd...
Page 104: ...fafadfdfdasfdsfdsdsdfdsfdsfdsfsdfdsa afdfdsfdsfdfdsfdsfsadfda asfdfaddfdd...
Page 105: ...Appendix E Schematics Communications Passive Tap M N 57C380...
Page 106: ...Appendix E Continued Fiber Optic Rack Power Supply M N 57C368...
Page 110: ...fafadfdfdasfdsfdsdsdfdsfdsfdsfsdfdsa afdfdsfdsfdfdsfdsfsadfda asfdfaddfdd...
Page 114: ...fafadfdfdasfdsfdsdsdfdsfdsfdsfsdfdsa afdfdsfdsfdfdsfdsfsadfda asfdfaddfdd...
Page 118: ...0 0 0 0 0 0 0 0 0 0 0 0 0 0 0 0 0 0 0 0 0 0 0 0 0 0 0 0 0 0 0 0...
Page 142: ......
Page 143: ...fafadfdfdasfdsfdsdsdfdsfdsfdsfsdfdsa afdfdsfdsfdfdsfdsfsadfda asfdfaddfdd...