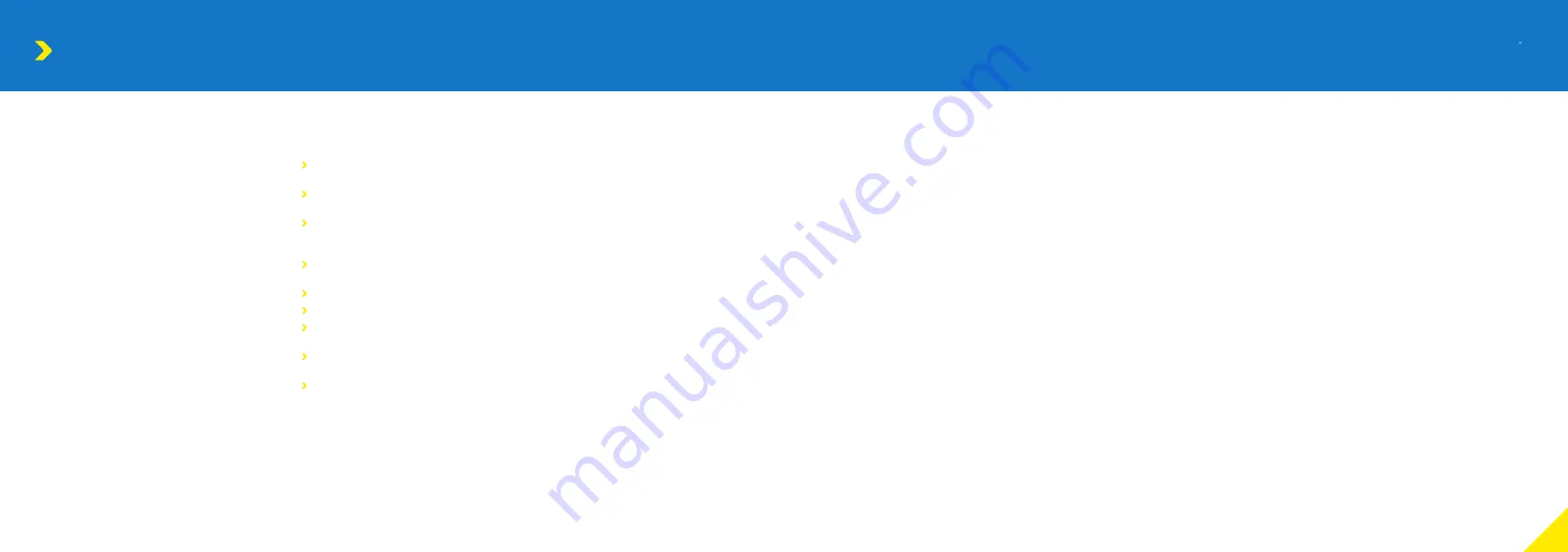
17
PORTA
BASE
It is recommended that once inspected or repaired,
the device is marked with the date of the next
inspection.
Inspections are instigated by the user. If detailed
information is required on inspection and test
criteria, please contact your supplier or REID Lifting.
The equipment Inspection Record can be found
on page 31.
If using the product in explosive atmospheres, see
additional section titled ATEX.
Maintenance & Repair
In order to ensure correct operation, the conditions
for inspection and maintenance must be complied
with. If any defects are found, stop using the
product immediately.
No alterations or additions to the equipment
beyond the replacement of standard parts by
an authorised representative should be made
without the written consent of the manufacturer.
Any necessary repairs identified during inspections
should only be carried out by an approved
specialist workshop using original spare parts. Any
repair must be carried out in accordance with the
manufacturer’s instructions.
It is recommended to maintain the equipment in a
clean and dry manner. Cleaning is suggested using
a sponge or cloth with warm, soapy water, rinsing
and allowing to dry.
This product must be assembled using metric
fixings of the same type and quality as those
supplied by the original manufacturer only. Failure
to do so could have an impact on the structural
performance and stability of the product. REID
Lifting and its resellers can supply these spare parts.
Storage & Transportation
When transporting the components, take note of
all the manual handling considerations.
Do not throw the product down or stack any
items on top of it.
Always place carefully and securely on the
ground to avoid damaging the equipment.
The following information is based on REID
Lifting’s recommendations and does not remove
the responsibility of the user to comply with the
relevant regulations and standards that are valid
in the respective countries and regions where the
system is being used.
Inspection & Maintenance
Before use, the product should be inspected for
visual defects using the checklist below:
Ensure all welds on the hub are free of cracks
or defects
Ensure levelling feet are not showing any signs
of deformation, corrosion or damage.
Ensure all adjustment pins are not distorted or
damaged. All pins shall be fully engaged before
using the product.
Ensure all bolts are correctly tightened and free
from excessive corrosion
Ensure all leg sections are free from indentation
Ensure the weight basket is retaining all weights*
Ensure the weight basket is fully engaged to the
tail before any lift*
Ensure the king pin for the davit is fully engaged
in the hub before applying a load.
Check the Davit in accordance with its
corresponding Assembly & Operation Guide.
*Only applicable to the counterbalance system
.
Inspections are instigated by the user, the above list
covers the main components on this product, any
accessories and third-party components must be
inspected following the corresponding instructions.
Regular Inspections
To ensure that the product’s frame remains in safe
working order it must be inspected regularly by a
competent or qualified person. We recommend
inspections every 6 months for personnel lifting
and every 12 months for goods only, unless
local regulations, adverse working conditions or
profile of use and risk dictate shorter periods.
The components of the system frame need to be
checked for damage, wear, corrosion or other
irregularities. It may be necessary to disassemble the
system frame in order to do this. Particular attention
should be paid to checking the profiles for denting,
making sure there is no wear or elongation on the
bolt holes.