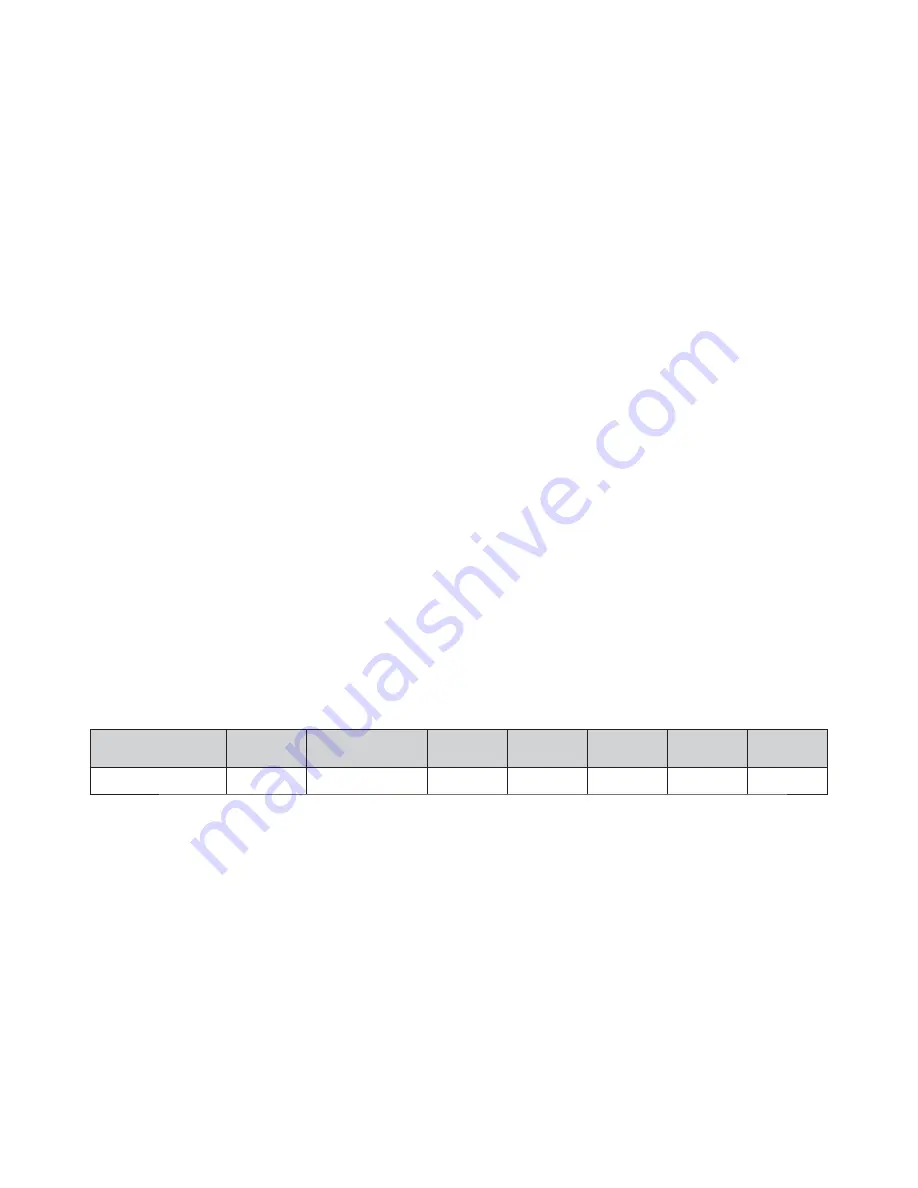
│
18
6 - Installation and Commissioning
Installation shall meet valid rules and may be done by quali
fi
ed staff only.
Defects caused by improper installation, use or handling are not covered by warranty.
After the tank is installed and connected to an existing heating system, it is recommended to clean
the entire heating system using a suitable cleaning agent, e.g. MR-501/R.
Anti-corrosion protective liquid should be also used, e.g. MR-501/F.
6.1 - Connecting heat sources
The tank shall be placed on the
fl
oor, as close to the heat source as possible. Mount the insulation,
see Chapter Mounting insulation onto the tank. Connect heating circuits to the inlets and outlets re-
specting the temperature distribution in the tank. Insulate all the connecting piping.
6.2 - Connecting a solar thermal system
This tank can be also connected to a solar thermal system. An extra
fl
ange and a tube heat ex-
changer (coil) will be needed, depending on the output of the solar thermal system. All connecting
pipes between the tank and solar collectors shall be insulated meticulously.
6.3 - Installing a heating element
The Thermal Store can be
fi
tted with two 3-phase electric heating elements with a longer non-heat-
ing end (ETT-C or ETT-L), 6 kW max. output each, or with two single-phase electric heating ele-
ments with a longer non-heating end (ETT-M), 3 kW max. output each. They can be wired directly to
the mains (heating elements equipped with own thermostat), or via a Controller for the entire heating
system.
All el. heating elements shall be installed together with a safety temperature limiter.
An el. heating element shall be wired by quali
fi
ed staff only.
6.4 - Connecting sanitary water piping
DHW piping shall be done according to valid rules. Installation of a pressure reducing valve to the
tank inlet is recommended. If the pressure from water mains exceeds 6 bar, a reducing valve is
necessary. Should the water be too hard, install a water softener before the tank. In case the water
contains mechanical impurities, install a strainer.
6.5 - Commissioning
The tank shall be
fi
lled up together with the heating system, respecting valid standards and rules.
In order to minimize corrosion, special additives for heating systems should be used. The quality of
heating water depends on the quality of
fi
lling water at commissioning, on the top-up water and on
the frequency of topping up. This has a strong in
fl
uence on the lifetime of heating systems. Poor
quality of heating water may cause problems like corrosion or incrustation, esp. on heat transfer
surfaces.
Hot water quality must meet the conditions shown in the Table of limit values for total dis-
solved solids in hot water on this page.
Fill the heating circuits with the appropriate
fl
uids and air-bleed the entire system. Check all connec-
tions for leaks and verify the system pressure. Set the heating controller in compliance with the docu-
mentation and manufacturer’s recommendations. Check regularly proper function of all control and
adjusting elements.
Table of limit values for total dissolved solids in hot water
Description
pH
Total dissolved
solids (TDS)
Ca
Chlorides
Mg
Na
Fe
Max. value
6,5 - 9,5
600
mg/l
40
mg/l
100
mg/l
20
mg/l
200
mg/l
0,2
mg/l