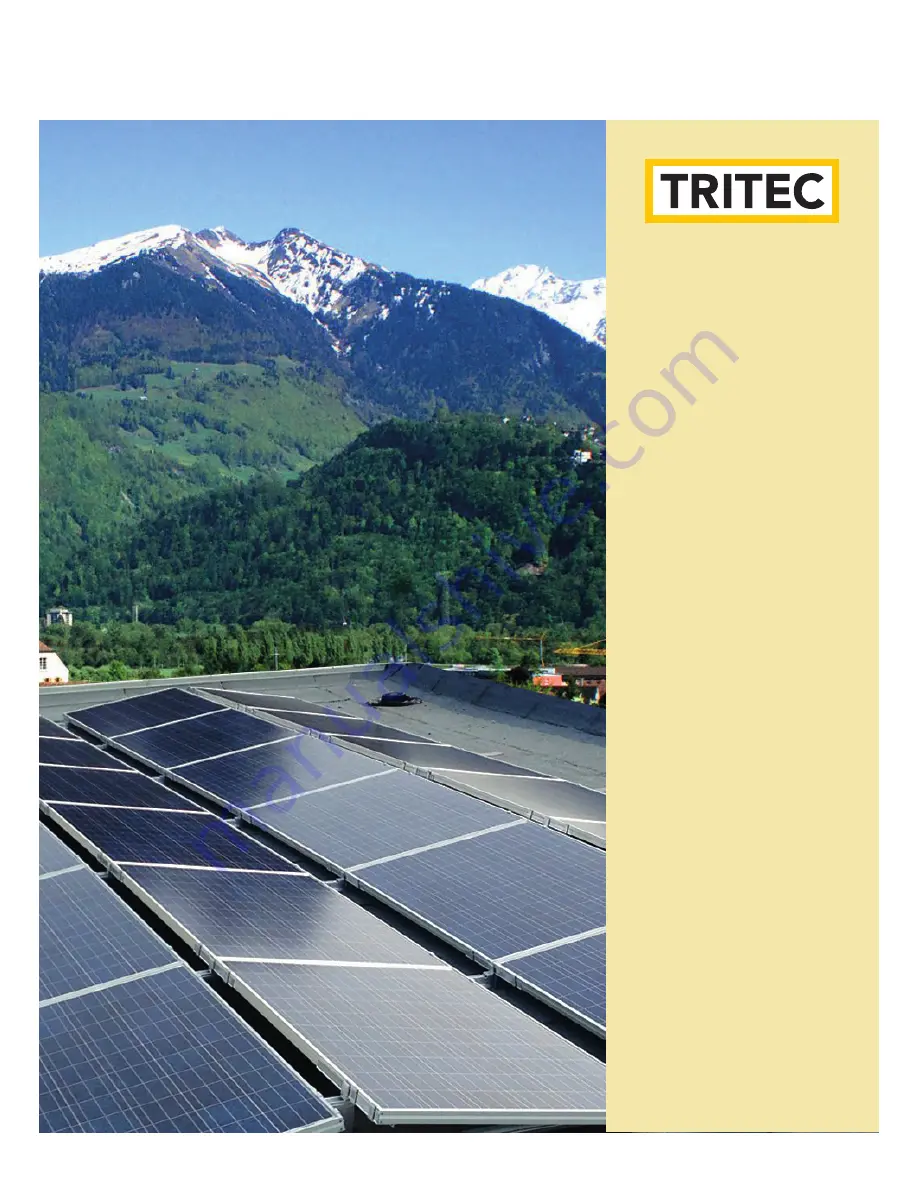
energy for a better world
INSTALLATION
INSTRUCTIONS
TRI-FLAT EAST-WEST
Ballast- and transport-optimized flat
roof installation system for PV
systems with east-west exposure
• no-drill and no-screw installation
• Fast and easy module clipping
using a click system
• Easy warehousing, fast and
economical transport
Summary of Contents for TRI-PLAT EAST-WEST
Page 2: ......