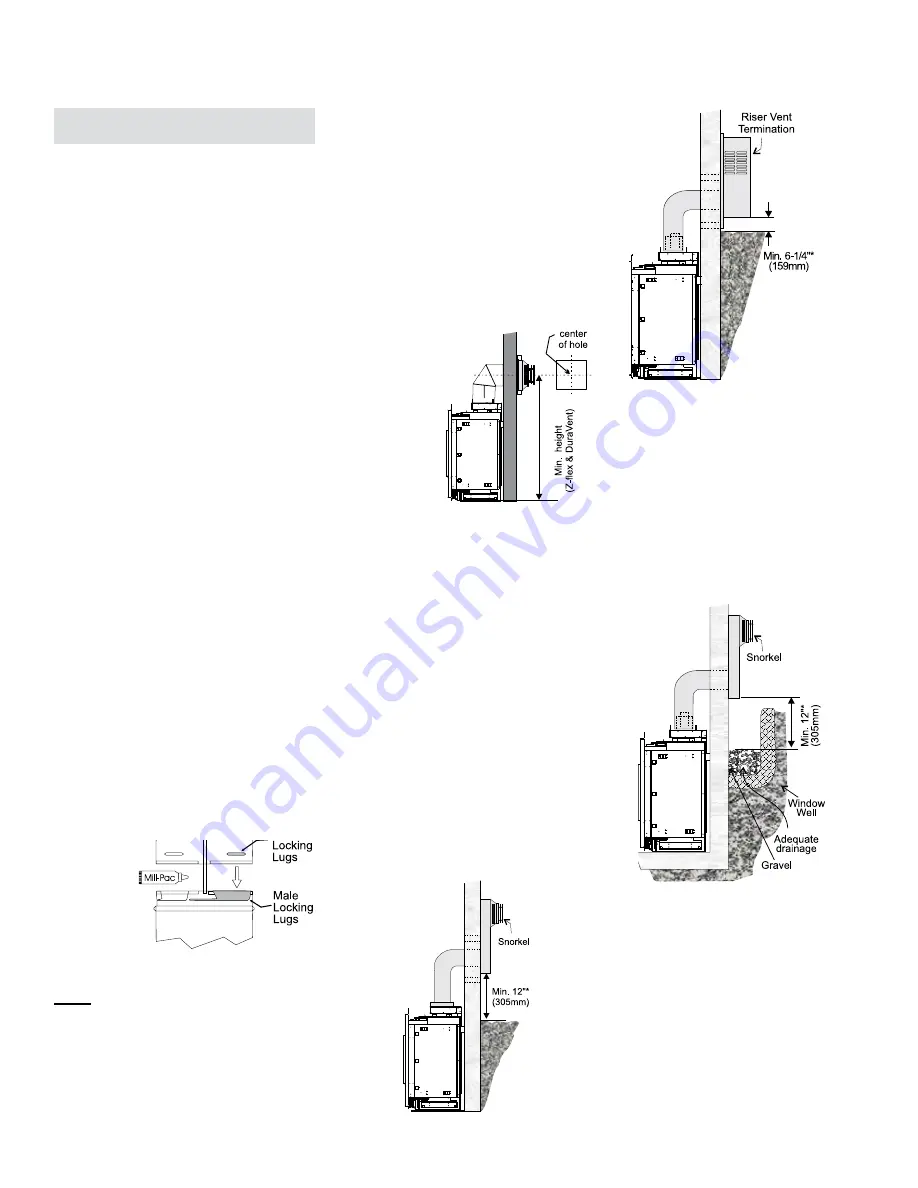
64
|
City Series CC40E-12
installation
56-1/4” (1429mm)
Diagram 4
6)
The arrow on the vent cap should be
pointing up.
Insure that the 1-1/2" clearances
to combustible materials are maintained
(Diagram 4). Install the termination cap.
The four wood screws provided should be
replaced with appropriate fasteners for stucco,
brick, concrete, or other types of sidings.
NOTE: For Snorkel terminations in
ABOVE grade installations,
follow national or local code
requirements.
Below Grade Installation
If the Snorkel Termination must be installed below
grade, i.e. basement application, proper drainage
must be provided to prevent water from entering
the Snorkel Termination. Refer to Diagram 4. Do
not attempt to enclose the Snorkel within the wall,
or any other type of enclosure.
*Diagrams 3 & 4: As specified in CGA B149
Installation Code. Local codes or regula
-
tions may require different clearances.
Dura-Vent Horizontal
Terminations
Install the vent system according to the
manufacturer's instructions included with
the components.
1)
Set the unit in its desired location. Check to
determine if wall studs or roof rafters are in
the way when the venting system is attached.
If this is the case, you may want to adjust the
location of the unit. Rough in the gas preferably
on the right side of the unit and the electrical
(junction block is on the left side) on the left.
2)
Direct Vent pipe and fittings are designed with
special twist-lock connections to connect the
venting system to the appliance flue outlet.
A twist-lock appliance adaptor is an available
option that must be used in conjunction with
the Simpson Dura-Vent Direct Vent system.
3)
Put a bead of Mill-Pac inside the outer section
of the adaptor and on the inner collar. Slip the
adapter over the existing inner and outer flue
collar and fasten to the outer collar only with
the 3 supplied screws (drilling pilot holes will
make this easier). Level the fireplace and fasten
it to the framing using nails or screws through
the nailing strips.
4)
Assemble the desired combination of pipe and
elbows to the appliance adaptor and twist-lock
for a solid connection.
Note:
a) T
wist-lock procedure: Four indenta
-
tions, located on the female ends of pipes
and fittings, are designed to slide straight
onto the male ends of adjacent pipes and
fittings, by orienting the four pipe indenta
-
tions so they match and slide in to the four
entry slots on the male ends, Diagram 1.
Push the pipe sections completely together,
then twist-lock one section clockwise ap
-
proximately one-quarter turn, until the
two sections are fully locked. The female
locking lugs will not be visible from the
outside, on the Black Pipe or fittings. They
may be located by examining the inside of
the female ends.
Diagram 1
b)
Horizontal runs of vent must be supported
every three feet. Wall straps are available
for this purpose.
5)
Mark the wall for a 10" x 10" square hole.
The center of the square hole should line
up with the centerline of the horizontal
pipe. Cut and frame the 10 inch square hole
in the exterior wall where the vent will be
terminated. If the wall being penetrated is
constructed of non-combustible material, i.e.
masonry block or concrete, a 7"(178mm)
dia. (7-1/2"(191mm) dia. for flex) hole is
acceptable.
Diagram 2
Note:
a)
The horizontal run of vent must be level,
or have a 1/4 inch rise for every 1 foot of
run towards the termination. Never allow
the vent to run downward. This could cause
high temperatures and may present the
possibility of a fire.
b)
The location of the horizontal vent
termination on an exterior wall must meet all
local and national building codes, and must
not be blocked or obstructed. For External
Vent Terminal Locations, see the "Exterior
Vent Termination Locations" section.
c)
Snorkel Terminations:
For installations requiring a vertical rise on
the exterior of the building, 14-inch and 36-
inch tall Snorkel Terminations are available,
as well as the standard Riser Vent. Follow
the same installation procedures as used
for standard Horizontal Termination. NEVER
install the snorkel upside down.
Diagram 3a
Note: Riser Vent
is only for use in
above grade ter
-
minations.
NOTE:
For best results and optimum perfor
-
mance with each approved venting system,
it is highly recommended to apply “Mill-
Pac” sealant (supplied) to every inner pipe
connection. Failure to do so may result in
drafting or performance issues not covered
under warranty.
Summary of Contents for City Series CC40LE-LP12
Page 104: ...104 City Series CC40E 12 warranty ...
Page 105: ...City Series CC40E 12 105 notes ...
Page 106: ...106 City Series CC40E 12 notes ...
Page 107: ......