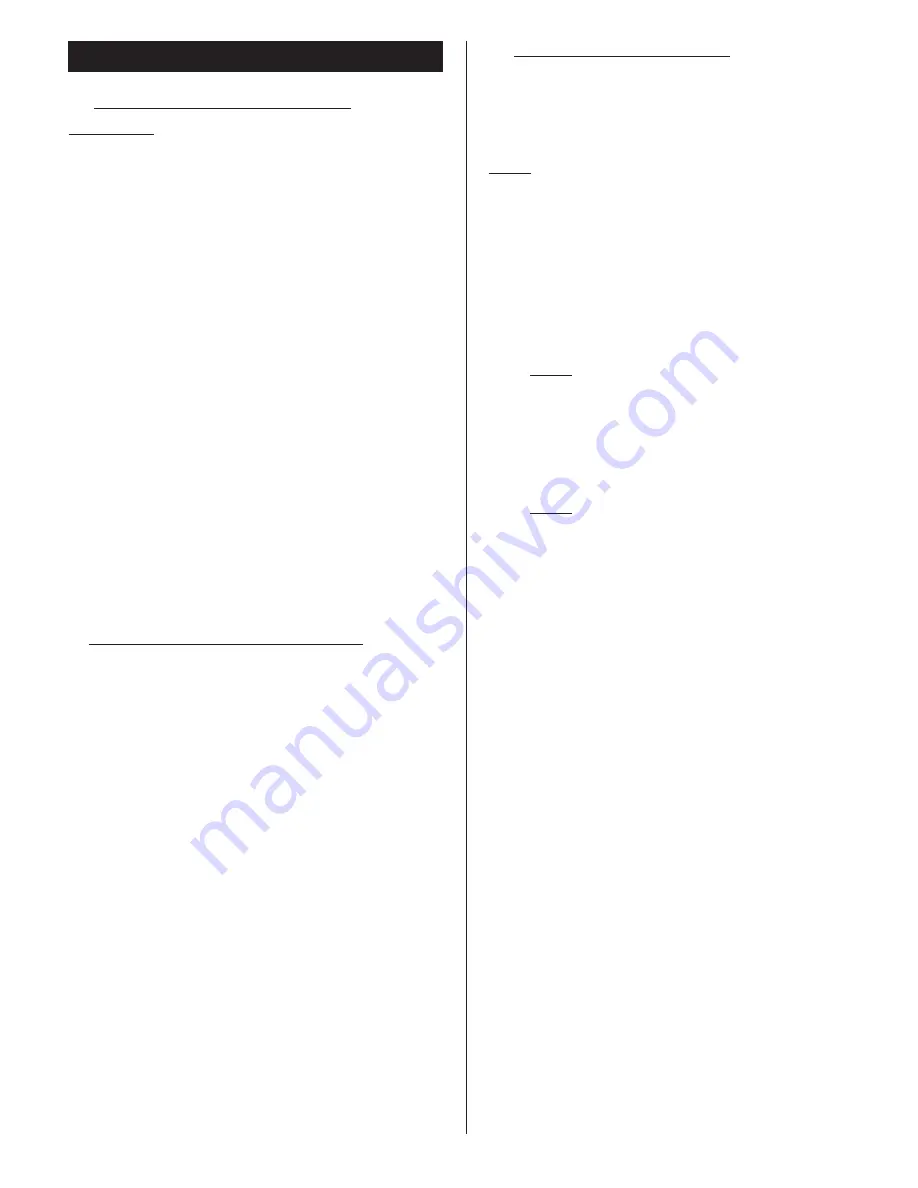
A) CALIBRATING THE ANALOG INPUT
IMPORTANT: The preferred Flow and/or Residual Units
and Ranges MUST be preset in the Configuration Mode
prior to calibrating the analog input(s).
The 4-20 mA analog Input (
AIN 1
) has been factory calibrated.
If re-calibration becomes necessary, an accurate 4-20 mA
signal generator is required. To begin calibration, enter the
Engineering Mode and proceed as follows:
1) In the Junction Box located on the left side of the Main
Enclosure, connect the 4-20 mA signal generator to
Terminals
#1
(positive) and
#2
(negative).
2) Scroll to the
CAL AIN1 (FLOW)
parameter.
3) Apply 4.0 milliamps to the input terminals and then
press the
ADJ
(adjust) button.
4) The displayed value should be
0.00
, representing zero
water flow. Press
ZERO
which will then establish the
4mA signal as the zero value.
5) Now apply 20.0 milliamps to the terminals. Press the
SPAN
button. Use the
UP
and
DOWN
buttons to set the
maximum water flow value. Then press
ENTER
.
6) This completes the calibration process.
7) Press
ESC
(escape) to return to the Engineering parameter
list. Press
ESC
a second time and
SAVE CHANGES
to
return to the main operating screen.
B) CALIBRATING THE ANALOG OUTPUT
The analog output has been factory calibrated. If re-calibration
proves necessary, an accurate digital VOM (volt ohm meter) is
required. Proceed as follows:
1) In the junction box located on the left side of the Main
Enclosure, connect the VOM to Terminals
#4
(positive)
and
#5
(negative).
2) Scroll to the
CAL AOUT
(calibrate analog output)
parameter and press
ADJ
(adjust).
3) Press the
4mA
keypad button and the digital display on
the VOM should also read
4.00
mA.
4) If the values do not match, use the
UP
and
DOWN
buttons until the VOM displays
4.00
mA. Then press
ENTER
to accept.
5) Press the 20 mA keypad button and the VOM digital
display should read 20.0 mA.
6) If values do not match, use the
UP
and
DOWN
buttons
until the VOM displays 20.0 mA. Then press
ENTER
to
accept. Calibration is complete.
7) Press
ESC
(escape) to return to the Engineering
parameters list. Press
ESC
a second time and
SAVE
CHANGES
to return to the main operating screen.
C) SETTING MECHANICAL ZERO
(See Drawing No. 8 for Model 7001 or No. 9 for Model 7006).
The mechanical zero valve plug position has been set at the
factory and should not need resetting unless the SMARTVALVE
is being serviced or a change in the system capacity is neces-
sary.
NOTE:
An 11/32” open end wrench is needed to set the
mechanical zero valve plug position.
To change the valve plug position, enter the Engineering Mode
as explained in Section 4.0 and then proceed as follows:
1) Scroll to the
CAL VALVE
parameter and press the
ADJ
(adjust) button.
2) After the motor stops turning and the SMARTVALVE
displays a “
0
” PPD gas feed rate, the metering tube ball
float will still be floating or fully rested on the bottom float
stop.
NOTE:
Confirm that the Zero Voltage reading on the
TOP LINE of the display falls in the acceptable range of
0.41
to
0.49
volts. If it falls outside the range, do not
proceed further. Contact Chlorinators Incorporated.
3) After the zero voltage has been confirmed, loosen the
lock nut (#7139) that is holding the valve plug (#7105 or
7506) in position on the lead screw shaft (#7109).
NOTE:
The top of the valve plug is also squared to
accommodate the 11/32” wrench.
4) IF THE BALL IS FLOATING, use the wrench to turn the
valve plug to the LEFT which will move it DOWN the
lead screw shaft. The ball will begin to drop slowly. Just
as it touches and comes to rest on the bottom stop of
the metering tube, STOP turning the valve plug. This is
the mechanical zero valve plug position. Carefully hold
the valve plug in position and secure it using the lock nut.
OR
IF THE BALL IS ALREADY RESTING on the bottom
float stop, turn the valve plug to the RIGHT to move it
UP the lead screw shaft. Keep turning it until the ball
begins to lift off of the bottom stop. Then slowly turn the
valve plug back to the LEFT until the ball just touches
and comes to rest on the float stop. Carefully hold the
valve plug and tighten the lock nut. Mechanical zero is
now set.
5) After mechanical zero is set, follow the remaining steps
under
CAL VALVE
to complete LINEARIZING THE
SMARTVALVE as explained in Section 6.0 (System Startup).
13
8.0 MAINTENANCE