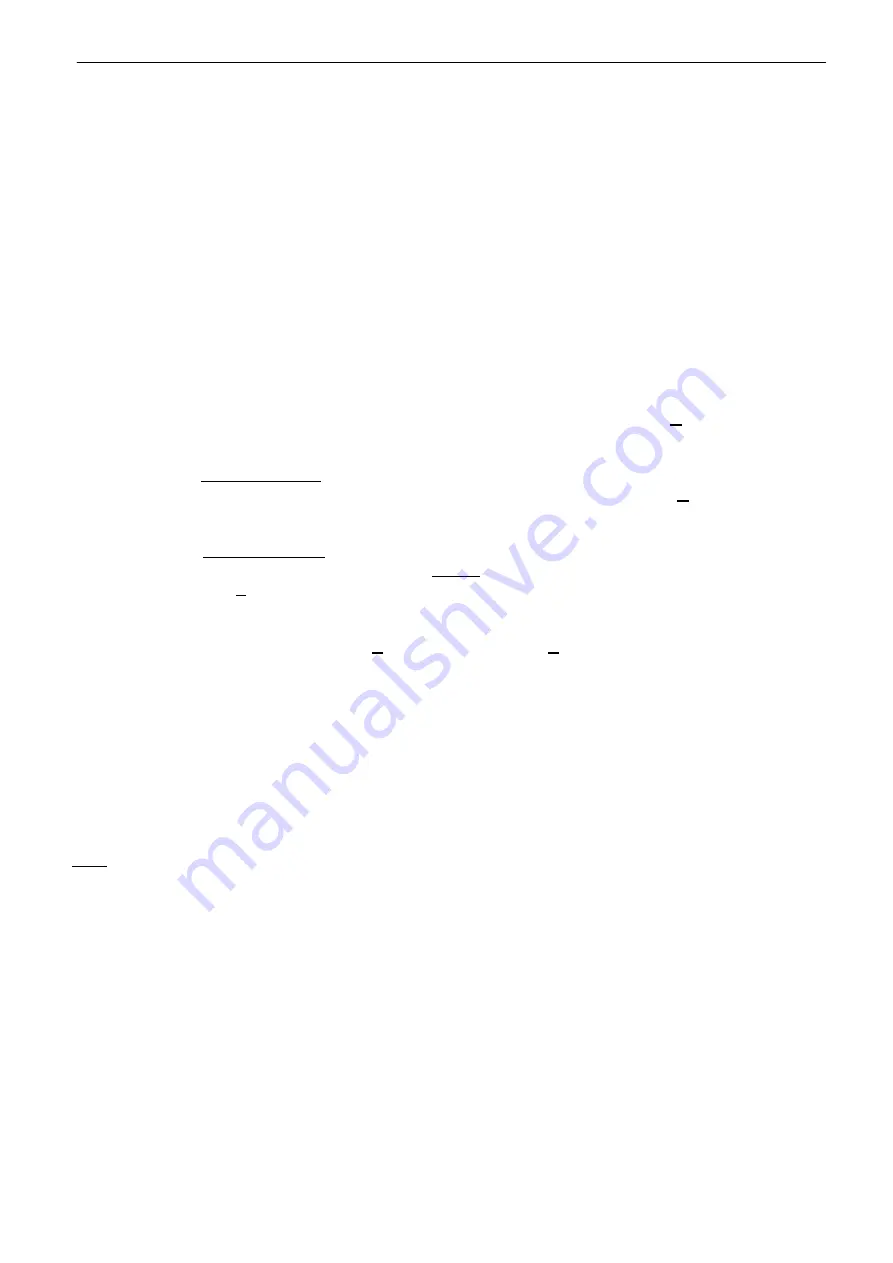
STR 0PA
23
-
after the calibration procedure is finished, the EA is prepared for its operation and starts to
response to control inputs
-
if changes to some parameters would be necessary, proceed please according to the
instructions given in the separate attachment No. 74 1053 02.
3.5
Putting an EA into operation when it is necessary to do a change to the stroke (setting
new end positions), and the other parameter setting done by the producer suits to your
needs
When an EA is delivered from the producer without armature, and the setting of other parameters
done by the producer suit to your needs, and it is necessary to do a change to the EA stroke, proceed
as follows:
- connect the EA with the armature to be controlled (according to chapter 2) and fit this assembly
into the specified technology complex,
- connect the EA electrically according to the wiring diagram and chapter Electrical connection... ,
- turn on the power supply, without connection of the control signals fed into ES (input control
signal - ES reports error/warning No.2 - no binary input),
- set the ES (
using manual control*
) to end position
closed
and push button
C for at least 2s,
until LED ERROR (red), LED MENU (green) and LED PAR (red) come on – the
closed
end
position is thus recorded in memory – see description in separate annex
No. 74 1053 02
,
- release the
C
setting button,
- set the ES (
using manual control*
) to end position
opened
and push button
O for at least 2s,
until LED ERROR (red), LED MENU (green) and LED PAR (red) come on – the
opened
end
position is thus recorded in memory – see description in separate annex
No. 74 1053 02
,
-
release
the
O
setting button,
-
introduce
the EA into an half position (see
Note 2
presented above),
- by pressing the
P
pushbutton on the control unit
for at least 2s
activate the EA calibration until
LED ERROR (red), LED MENU (green) and LED PAR (red) come on – see also description of
the procedure in separate annex
No. 74 1053 02,
- release the adjustment pushbutton
P -
upon release of the
P
pushbutton, the calibration process
is started,
- turn on the control signals, EA is ready for operation and responds to control inputs,
- if any of the parameters need to be changed, proceed according to the instructions in separate
annex
No. 74 1053 02,
* This
This applies to
setting of EA to be controlled by 2P and 3P or 3P/2P switched by I2, at the same time
with standard setting of menu 9 FAILURE REACTION: STOP!
If the input control signal is set to one of the ranges starting from 0 mA, it is necessary to change the range to a
different one. If this is not the case and a control signal is not supplied, the servodrive output component will
take up the position corresponding to 0 mA. After recording the new limit positions change the value of the input
control signal and response to error to the required parameters.
Note: in cases where the sequence is implemented using a PC in the EHL Explorer programme or using local
control, neither the change of response to error nor disconnection of the control signals is required.
3.6 Setting other parameters
If changes to some parameters would be necessary, proceed please according to the instructions
given in the separate attachment
No 74 1053 02
.
3.7 Gear unit adjustment
Switching-off thrusts for the „Opening“ direction (S1 power switch) and for the „Closing“ direction
(power switch S2) as well are set by the producer to a certain value with a
±
10% tolerance. These
values are given in the specification table No.1.
It isn’t possible to set and change the gear unit to different thrust values without using
a test equipment for measuring the thrust
. When overloaded, EA switches off in any position of the
stroke beyond the set range of the blocking of the switching-off from thrust in the stroke end positions.
The blocking of the switching-off from thrust can be chosen for a certain range of the stroke starting
from the stroke end position, for a period from 0 up to 20 s (see setting the
MENU 3
in the separate
attachment No.
74 1053 02
).
Summary of Contents for Rematic
Page 9: ...STR 0PA 7 Fig 1 6 2 1 4 3 5...
Page 30: ...28 STR 0PA 6 Enclosures 6 1 Wiring diagrams...
Page 32: ...30 STR 0PA 6 2 Dimensional drawings...
Page 33: ...STR 0PA 31...
Page 34: ...32 STR 0PA...
Page 35: ...STR 0PA 33...
Page 36: ...34 STR 0PA...
Page 37: ...STR 0PA 35...
Page 38: ...36 STR 0PA...
Page 39: ...STR 0PA 37...
Page 40: ...38 STR 0PA...
Page 41: ...STR 0PA 39...
Page 42: ...40 STR 0PA...
Page 43: ...STR 0PA 41...