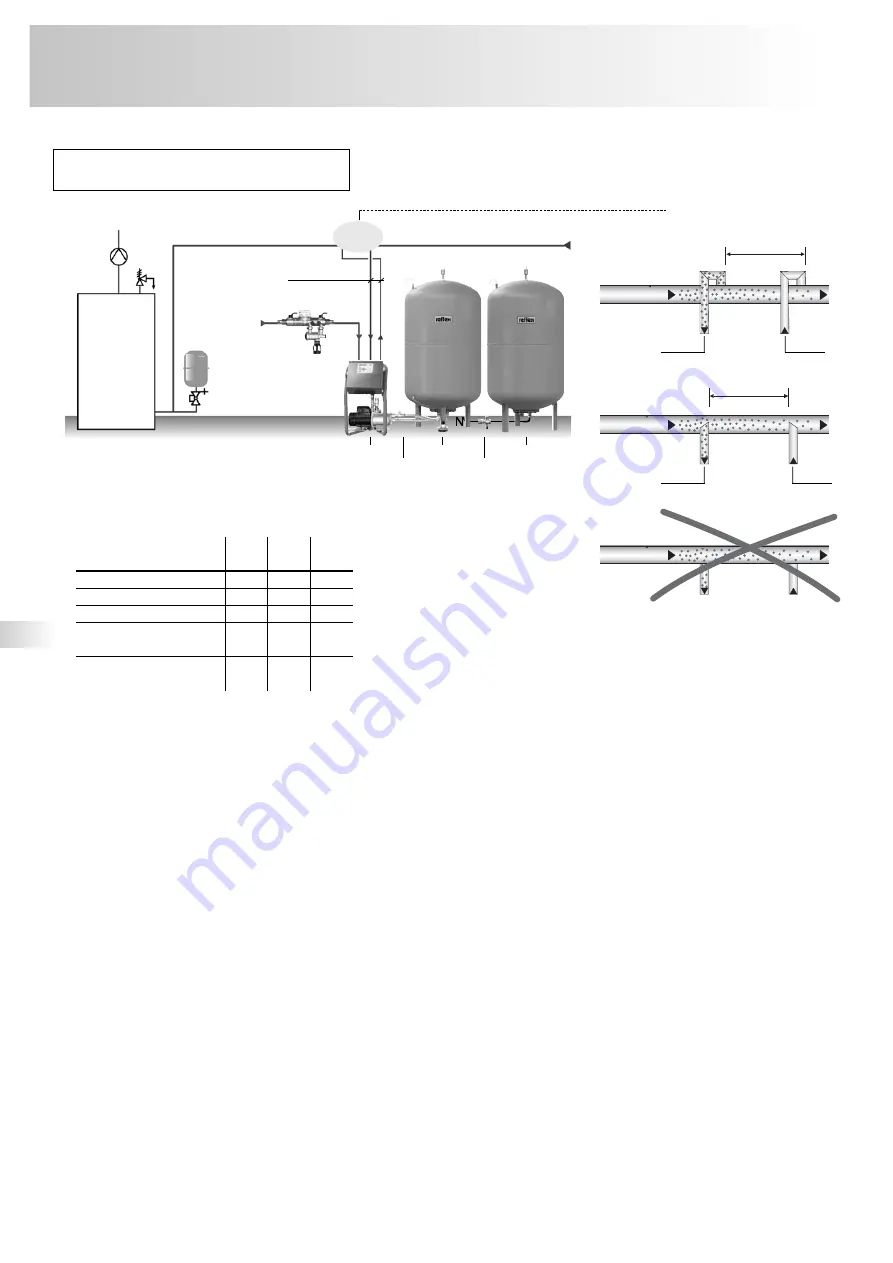
The additional degassing function means that two expansion
lines (O, P) must always be installed for the ’variomat’.
Regardless of the ’variomat’ nominal connection width, the
size of the expansion lines must at least correspond to the
values specified in the table.
Integrate the overflow line (O) ahead of the pump line (P)
seen in the direction of flow of the system.
Integrate the ’variomat’ in a representative main flow of
the system.
Max. medium temperature at the integration point 70 °C,
max. glycol content 50%.
To avoid coarse dirt entering and overloading the ’variomat’
dirt trap, integration must be performed according to the
above diagram (see “Close-up of integration point”). Flush
the pipelines of the heating system and the potable water
make-up unit prior to start-up.
In the case of water heating systems according to DIN 12828
(formerly DIN 4751 P2), it must be ensured that only
protected shut-off facilities or none at all are installed
between ’variomat’ and the heat generators. Otherwise the
heat generators must be individually protected
(recommended for ’variomat’).
Individual protection:
Owing to the sound degassing
performance of the ’variomat’, it is recommended even
with single boiler systems to install a diaphragm pressure
expansion vessel (for instance ’reflex N’) at the heat
generator to minimise the switching frequency.
Connection line for make-up:
If the make-up
line is connected directly to a potable water system, reflex
’fillset’ (shut-offs, system separator, water meter, dirt trap)
must be installed upstream. If reflex ’fillset’ is not installed,
a dirt trap with a mesh size
≤
0.25 mm must at least be
installed to protect the make-up solenoid valve. Keep the
line between the dirt trap and the solenoid valve as short as
possible and flush.
If the automatic make-up facility is not connected, the
connection (WM) of the make-up line must be sealed with
a R ½ plug.
Note:
If manual make-up is not performed in time, the
’variomat’ pressure-maintaining station will switch to an error.
The normal pressure at the ’variomat’ make-up solenoid
valve must not exceed 6.0 bar. Install a pressure reducer
upstream if required.
- p
0
= minimum operating pressure,
→
p. 15
- expansion lines > 10 m length install one
size larger
Connection of the ’variomat’ control unit,
expansion lines
Expansion lines (O, P)
≥
500
Main flow V
circuit water
≥
500
Main flow V
circuit water
rich in gas
low in gas
rich in gas
low in gas
Main flow V
circuit water
Close-up of integration point
from above
from below as
immersion tube or
from the side
butt-welded
from below -
not permitted
DN
DN
DN
DN
25
32
40
50
variomat 1
x
variomat 2-1/...
x
variomat 2-2/35
x
variomat 2-2/...
x
p
0
≤ 3.5 bar
variomat 2-2/...
x
p
0
> 3.5 bar
Water make-up
p
≤
6 bar
reflex ’fillset’
max. 70 °C
Control unit
VG basic vessel
VF secondary vessel
Connection set G 1
reflex ’SU quick
coupling’ R 1x1
Line DN 25 on site
Sizing of
expansion lines
WM O
P
Close-up of
integration
point
reflex ’variomat’
Assembly
10