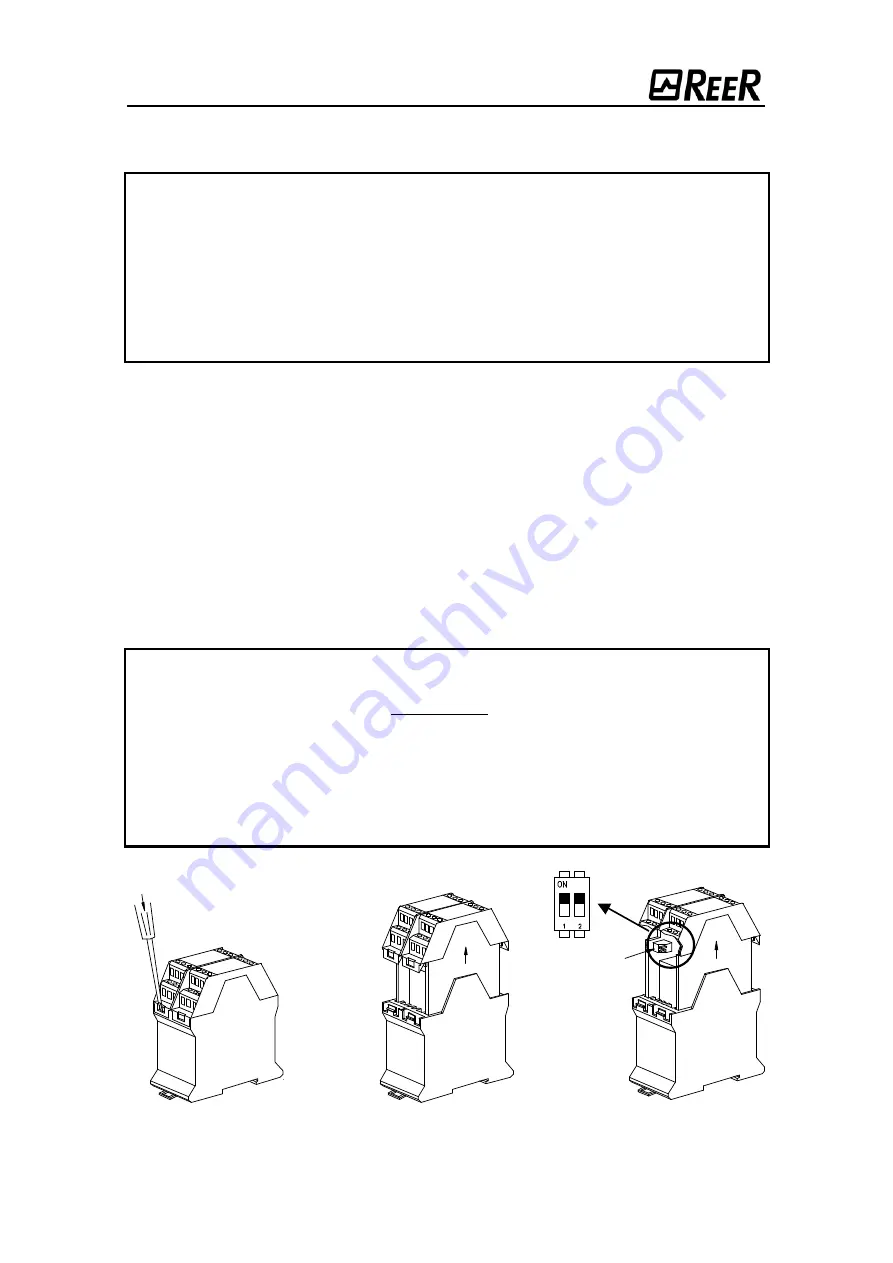
7
INSTALLATION AND ELECTRICAL CONNECTIONS
+
The AD SR2 safety interface must be installed in an environment with at least
IP54 protection.
+
The voltage supplied to the AD SR2 interface must be of the FELV (Functional
Extra Low Voltage) 24VDC
±±
20% type.
+
During installation, take care not to short-circuit terminals 7, 8, 10 and 11 on
the AD SR2 interface.
+
If connecting one barrier only, bring inputs that are not used (8 and 11)
to +24VDC.
The safety switch.
The system moves to
BREAK
status (output relays open) when the
safety switch
(e.g. emergency pushbutton, safety limit switch)
,
connected as illustrated in the electrical diagrams on pages 4, 5, 6,
is
opened.
The switch must respond to the following specifications:
•
2 N/C contact blocks connected mechanically.
•
Release action to control contact opening.
•
There must never be more than a 500msec delay between
both contacts in the switch closing; if that is not the case, the
interface moves to
FAIL.
The interface can only restart
(GUARD)
after resetting the switch (with
the barrier clear).
+
Should risk analysis regarding dangerous machinery authorize the use of a
safety switch with ONLY 1 N/C CONTACT (e.g. terminal 9 connected to +24VDC
or terminal 12 earthed), set both sections of the dip-switch (1) to ON (figure 5).
In that case, the test circuit for that specific safety switch will no longer
conform to EN 954-1 type 4.
+
If using a safety switch with ONLY 1 N/C CONTACT, terminal 9 must be used
(to +24VDC). Terminal 12 must be left open.
+
If the safety switch is not used, connect terminal 9 to +24VDC and terminal 12
to 0Vdc (dip-switch to OFF).
Figure 5
(1)
(PRESS LIGHTLY ON ALL
FOUR HOOKED COUPLINGS)
Summary of Contents for AD SR2
Page 2: ...2...