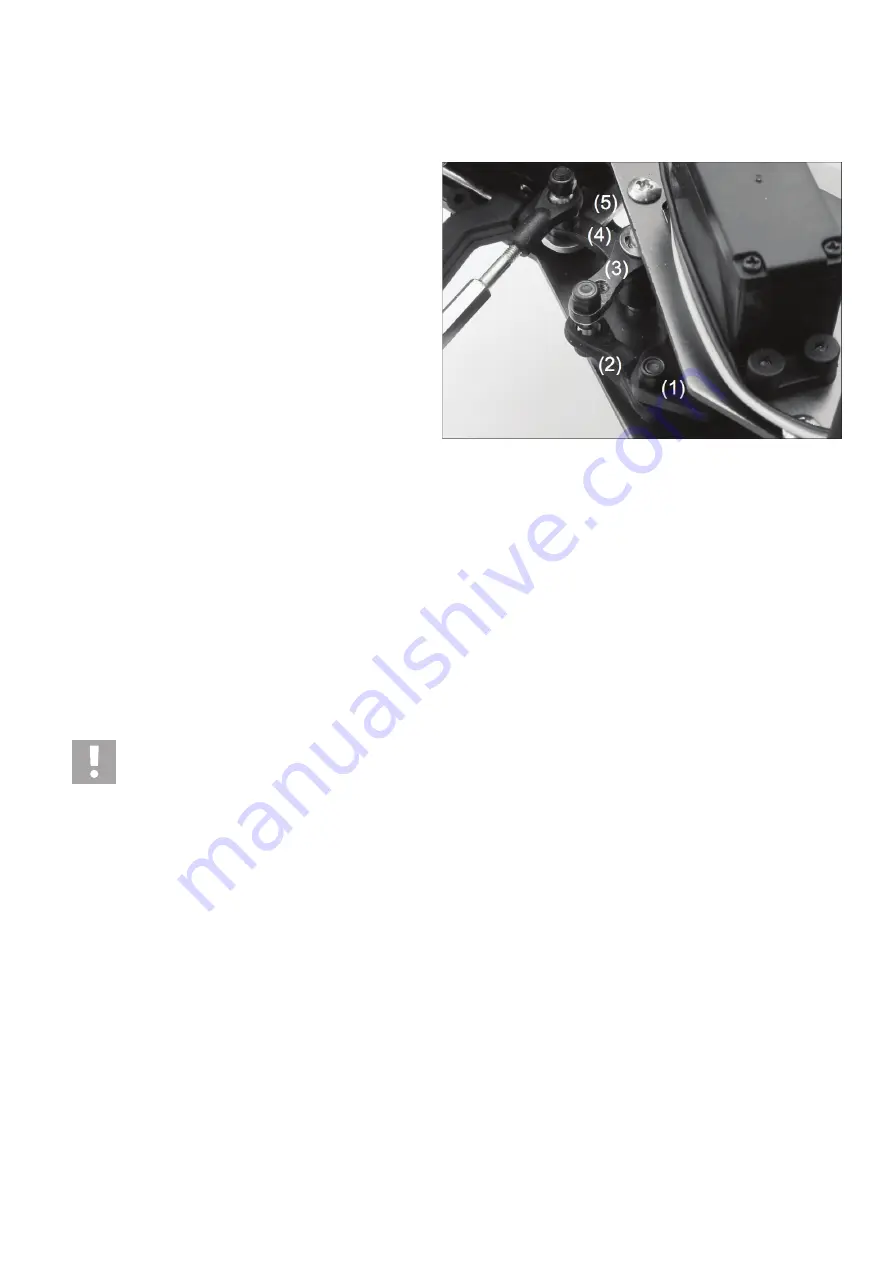
38
k) Function check of servos
Steering servo
The steering servo is connected to channel 1 of the remote control, i.e. to the steering control wheel.
Construction of steering
The steering of the vehicle is designed as an axle leg steering.
The steering knuckle arms are connected with the three-part steering
link. The pivoting movement of the servo control lever is transmitted via
the steering linkage (1) to one arm of the servo saver (2).
The servo saver consists of two levers at a 90° angle to each other,
which are not rigidly coupled but can be moved against each other via a
spring on a level with the steering linkage.
The second lever arm of the servo saver (3) steers the centre part of the
steering link, the steering plate (4) and in this way causes the wheels to
turn via the steering link (5).
When hard shocks are transmitted from the wheels into the steering link
during operation, they are not immediately transmitted to the steering
servo, but are absorbed by the resilient connection of the two lever arms
of the servo saver.
The effect of the servo saver can be adjusted with a knurled nut (6) by
modifying the contact pressure on the two lever arms. The steering ang-
le to the right and left is limited by a mechanical stop of the steering arm
against the axle leg support.
Function check
• Support the model at the front so that the wheels hang freely.
• Due to the wheels' good grip and the weight of the vehicle, the wheels would not directly respond to the remote control if the vehicle is on the ground. The
response is as it should be when driving.
• First switch on the transmitter, then the receiver.
• Move the steering control wheel (channel 1) to the right and the left.
• The wheels must turn to the right and the left!
• If the wheels turn in the opposite direction, switch the servo reverse on the remote control to the "REV" position (reverse).
• Release the steering control wheel. The wheels must turn back to straight-drive position. If the wheels do not exactly assume straight-drive position when the
steering control wheel is in neutral position, adjust the trim on channel 1. The end stops of the steering control wheel should cause the steering to fully go to
the right/left!
Servo saver
The servo saver has already been pre-adjusted. Before first use it has to be checked and might have to be set tighter (so that the control commands
of the steering servo are carried out when driving quickly).
Throttle/brake servo
The throttle/brake servo is connected to channel 2 of the remote control.
Mode of action and throttle/brake linkage settings
The throttle/brake linkage carries out two functions at the same time via two servo steering levers that are at a 90° angle to each other.
Moving the "carburettor slider" regulates the air supply to the engine via the throttle linkage. At the same time the idle jet needle (tapered needle of a needle
valve) is moved, which changes the amount of fuel flowing through the carburettor. If the throttle linkage is moved beyond neutral position (mechanical end stop
of the carburettor slider), the servo lever pushes against a spring stop.
Now the sphere of action of the brake linkage comes to effect, it presses the brake shoes of the disc brakes together via an eccentric tappet.
The positioning of the adjustment rings (the mechanical end stops) of the stop springs on the throttle linkage and the brake linkage are preset. They are adjusted
to the mechanical end stops of the carburettor and the disc brakes. The gas/brake linkage should not require any readjustments.
However, adjustment rings may become loose during operation and may have to be retightened.
If the brake drags, the brake pads and the brake disc wear out.
In order to ensure that the brake is completely released, make sure that the brake control lever is located at a distance of approx. 1 mm between the adjustment
rings on the brake linkage.
Summary of Contents for 23 69 90
Page 106: ...106 ...
Page 107: ...107 ...