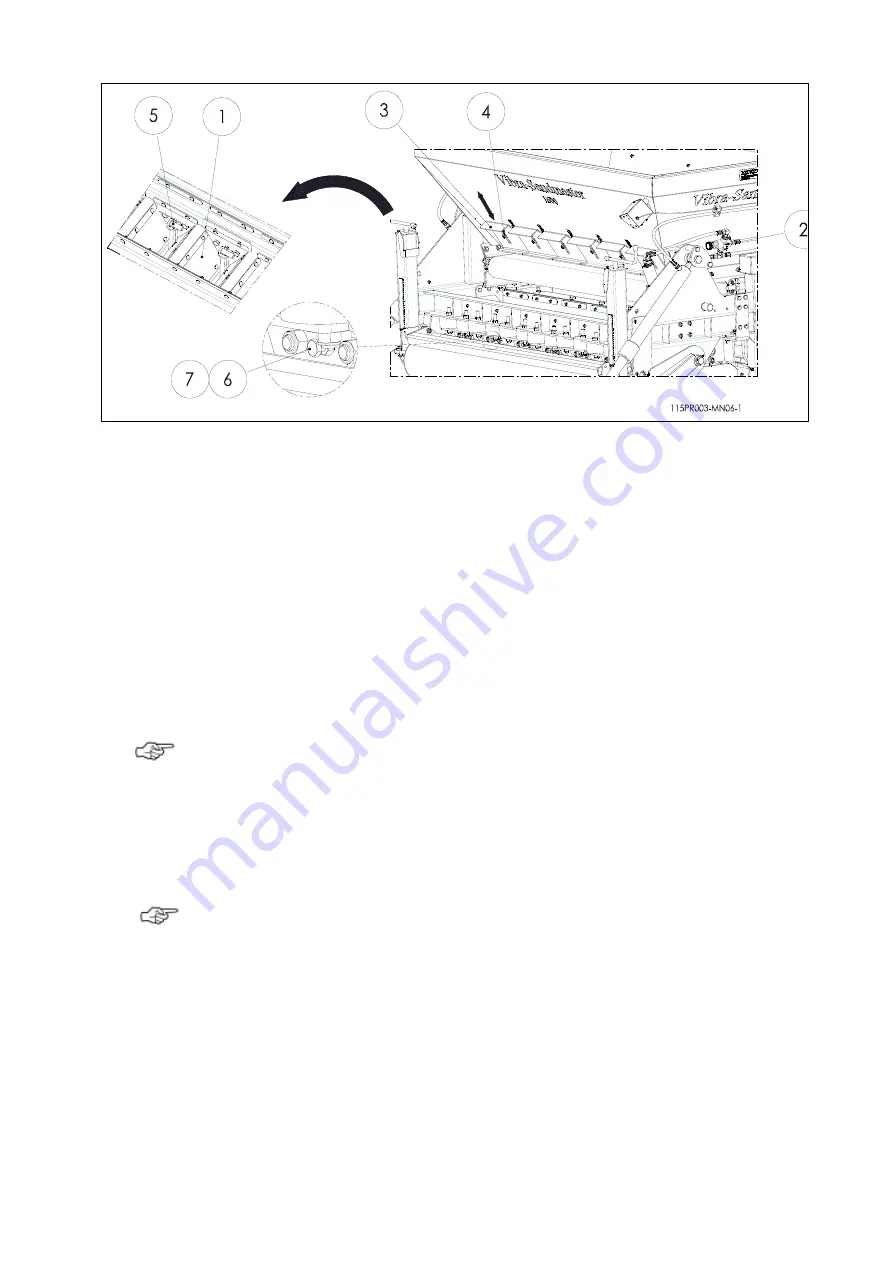
18
Fig.11
7.2 SETTING MATERIAL SUPPLY
The supply setting of the material that is fed to the grooves differs per type of material, operating
depth, speed, etc.
Due to the combination of these factors, the correct setting for the material used is a process of trial
and error.
Main point is that, when in operation, the filling coulters 1 must continue to be replenished without
running empty. This can be monitored via the camera screen onboard the tractor.
In order to set the material supply on the machine, you can choose from the following options:
Setting by adjusting the speed of the conveyor.
(Fig.11)
The speed of the conveyor can be adjusted by rotating choke 2 at the side of the hopper.
Clockwise = slower Anti-clockwise = faster.
Practical experience shows that the supply can be controlled most effectively
by switching on/off the conveyor as the filling funnels are running empty / full.
Setting per filling coulter.
(Fig.11)
Per filling coulter, a dosing slide 3 is fitted at the rear of the hopper.
This dosing slide can be adjusted by loosening nuts 4, putting dosing slide 3 in the desired
position and tightening nuts 4 again.
Practical experience shows that the outer dosing slides must be opened further
than the inner ones. In order to limit wear to the conveyor to a minimum, the
slides must be opened as far as possible, with the position depending on the
material.
Summary of Contents for Vibra-Sandmaster 1600
Page 10: ...10 Fig 7...