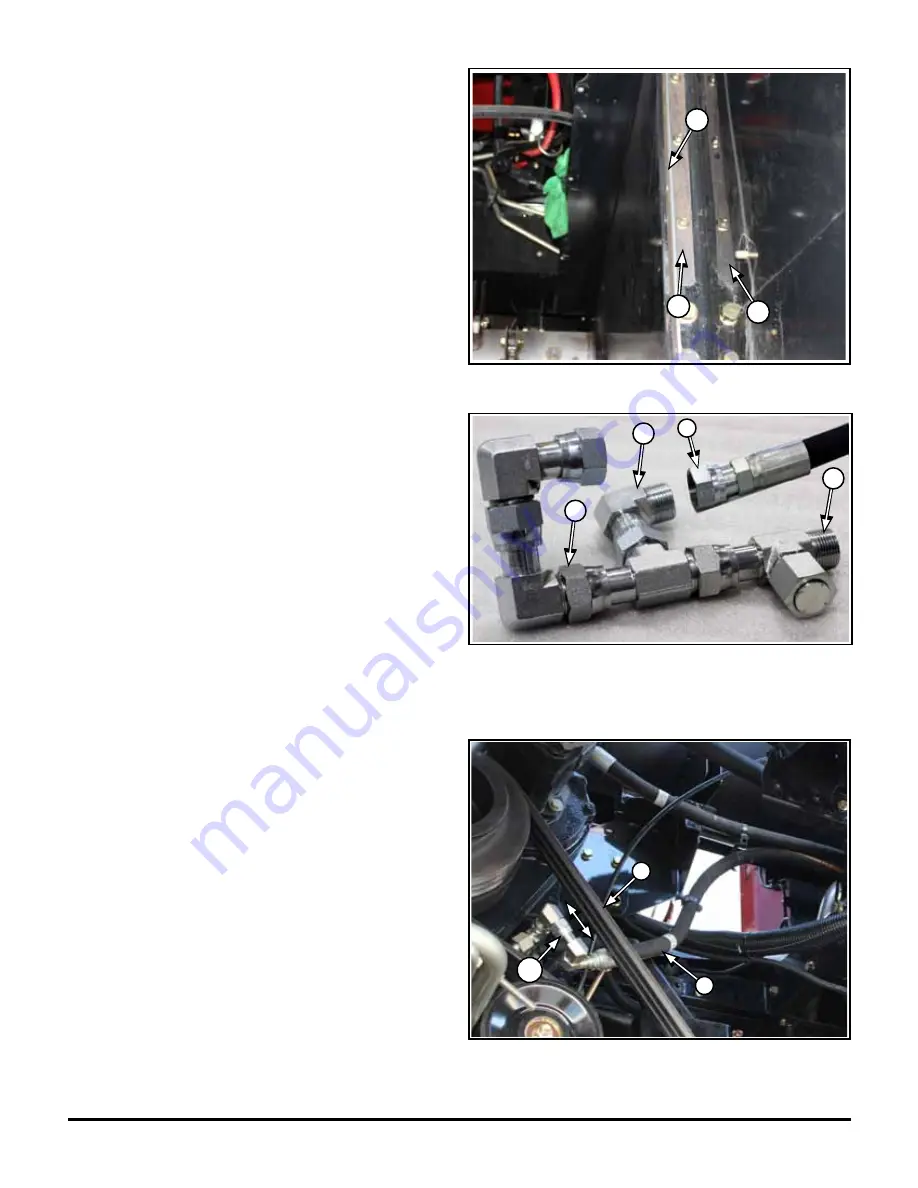
51
4.2.9
Connect new hydraulic rubber line (
F
) to new
hydraulic fitting assembly (
EA
) at end (
E2
)
4.2.9.1
Connect new hydraulic rubber line (
F
) to
hydraulic knifebar valve (
A
)
- use same routing as hydraulic steel line (
D
) just
removed
4.2.10
Connect hydraulic hose (
B
) from reservoir tank to
new hydraulic fitting assembly (
EA
) at end (
E4
)
- quickly remove plug (
B1
) from end of hose (
B
) and
connect to minimize oil leakage
F
E2
EA
E4
4.2.10.1
Orientate fittings (
EA
) in line with belt (
G1
)
EA
E2
F
EA
G1
B