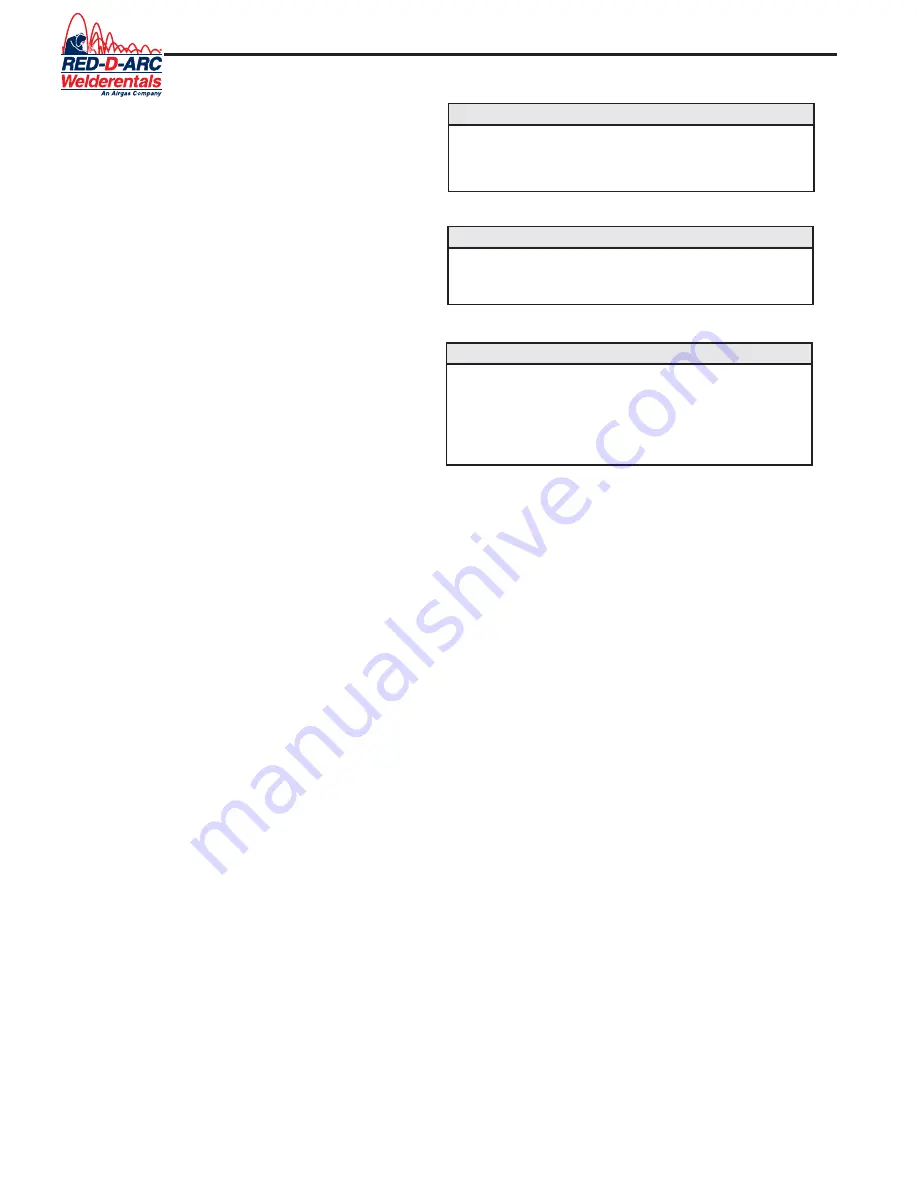
OPERATION
4
OPERATION
For best operating characteristics and longest unit life, take care in
selecting an installation site. Avoid locations exposed to high
humidity, dust, high ambient temperature or corrosive fumes. Make
sure that the ventilator openings are not obstructed.
• Connect welding machine to input voltage.
• Set INPUT CONTACTOR CONTROL ON/OFF SWITCH to ON
(UP) position.
• For LOCAL control, set the CURRENT CONTROL LOCAL/
REMOTE SWITCH to local (OFF) position. Adjust the welding
current by the CURRENT CONTROL potentiometer located on the
front panel.
• For REMOTE control, set the above switch to remote (ON)
position. Adjust the welding current by the potentiometer located in
the remote control.
For this mode of operation it will be necessary to use a Remote
Control Pendant plugged into the REMOTE CONTROL
RECEPTACLE.
• THE ARC FORCE CONTROL potentiometer varies the dynamic
slope of the volt-amp curves. It essentially charges the short-circuit
(arc) current and produces an increase of amperage when the arc is
shortened. Strong arc force is best suited for use with 6010
electrodes where there is a tendency for sticking, especially for
down hand welding.
MAINTENANCE
•
Lubrication
The fan motor is permanently lubricated and will never need oil or
grease. No other points require lubrication.
•
Cleaning
For uninterrupted satisfactory service from this welding machine, it
is necessary to keep the machine clean, dry and well ventilated.
At lease every two months or more often as necessary,wipe and
blow out all dirt from the machine's internal components with air
pressure of not over 25psi. Be sure to wipe the fan blades clean.
TECHNICAL DATA
DIMENSIONS
680 x 405 x 530 mm
(LxWxH)
26.8 x15.9 x20.9 in
NET WEIGHT
117kg / 258 lbs
DIMENSIONS
775 x 535 x 560 mm
( in frame)
30.5 x 21 x 22 in
NET WEIGHT
130kg / 285 lbs
(in frame)
CSA APPROVED
RATED OUTPUT
DC
Amperes
250
Volts
30
Duty cycle
60%
WELDING VOLTAGE AND CURRENT RANGE
Minimum current at 20Volt
20A
Maximum current at 34Volt
350A
INPUT 3 PHASE 60Hz - AT RATED LOAD
480V - AMPS - OPT
21
600V - AMPS - OPT
17
PRIMARY KW
1l