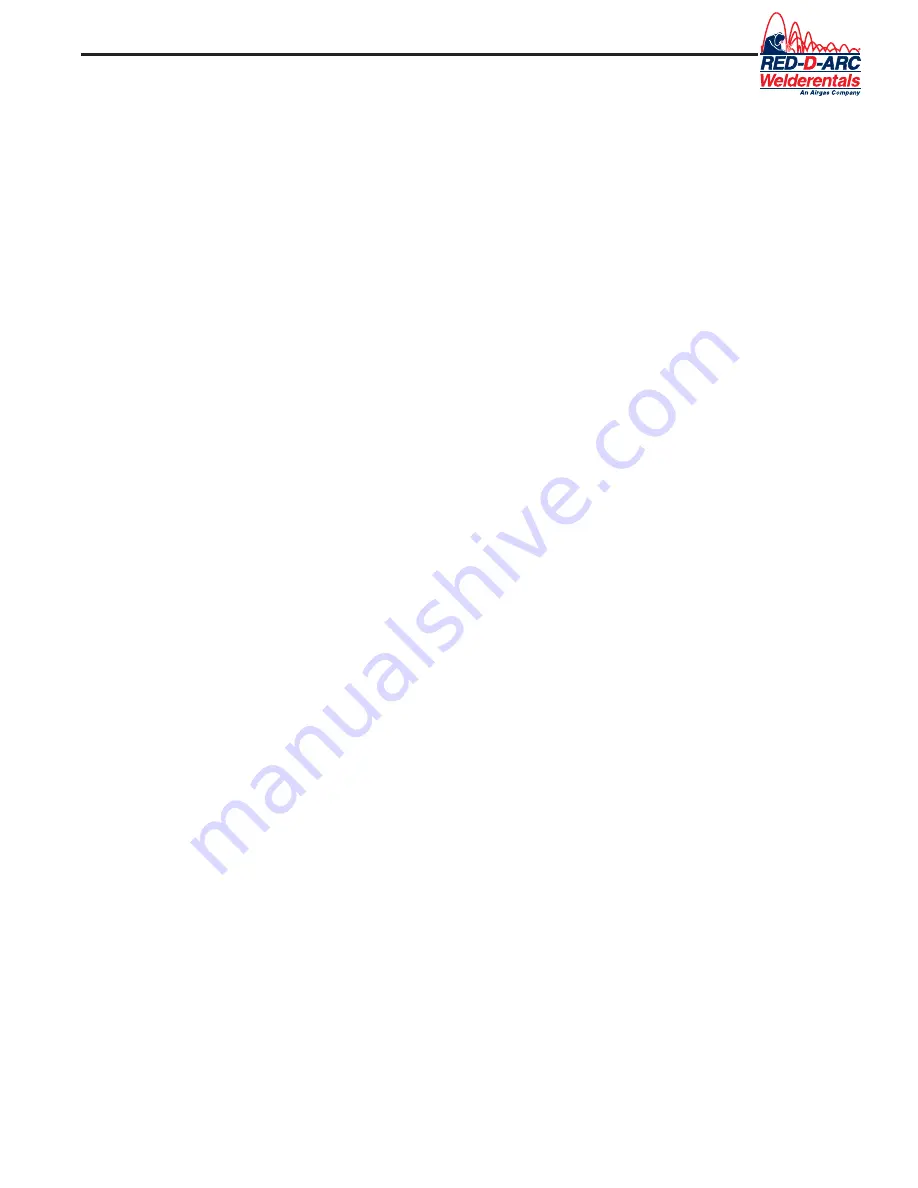
SAFETY
3
AWS F4.1-80 from the American Welding Society.
e.
Vent hollow castings or containers before heating, cutting or
welding. They may explode.
f.
Also see items 6c and 9c.
6. For Welding in General.
a.
Droplets of molten slag and metal are thrown or fall from the
welding arc. Protect yourself with oil free protective garments
such as leather gloves, heavy shirt, cuffless trousers, high shoes
and a cap over your hair. Wear ear plugs when welding out of
position or in confined places. Always wear safety glasses when
in a welding area. Use glasses with side shields when near slag
chipping operations.
b.
Keep all equipment safety guards, covers and devices in position
and in good repair. Keep hands, hair, clothing and tools away
from V-belts, gears, fans and all other moving parts when start-
ing, operating or repairing equipment.
c.
Be sure the work cable is connected to the work as close to the
welding area as practical. Work cables connected to the building
framework or other locations some distance from the welding
area increase the possibility of the welding current passing
through lifting chains, crane cables or other alternate circuits.
This can create fire hazards or overheat lifting chains or cables
until they fail.
7. For Gas-Shielded Arc Welding.
a.
Use only compressed gas cylinders containing the correct shield-
ing gas for the process used and properly operating regulators
designed for the gas and pressure used. All hoses, fittings, etc.
should be suitable for the application and maintained in good
condition.
b.
Always keeps cylinders in an upright position securely chained
to an undercarriage or fixed support.
c.
Cylinders should be located:
•
Away from areas where they may be struck or subjected to
physical damage.
•
A safe distance from arc welding or cutting operations and
any other source of heat, sparks, or flame.
d.
Never allow the electrode, electrode holder, or any other electri-
cally "hot" parts to touch a cylinder.
e.
Keep your head and face away from the cylinder valve outlet
when opening the cylinder valve.
f.
Valve protection caps should always be in place and handtight
except when the cylinder is in use or connected for use.
g.
Read and follow the instructions on compressed gas cylinders,
associated equipment, and CGA publication P-1 "Precautions for
Safe Handling of Compressed Gases in Cylinders" available
from the Compressed Gas Association, 1235 Jefferson Davis
Highway, Arlington, VA 22202.
8. For Electrically Powered Equipment.
a.
Turn off input power using the disconnect switch at the fuse box
before working on the equipment.
b.
Make the electrical installation in accordance with the
National Electrical Code, all local codes and the manufacturer's
recommendations.
c.
Properly ground the equipment in accordance with the National
Electrical Code and the manufacturer's recommendations.
9. For Engine Powered Equipment.
a.
Turn the engine off before troubleshooting and maintenance
work unless the maintenance work requires it to be running.
b.
Operate the internal combustion engines in open, well ventilated
areas or vent the engine exhaust fumes outdoors.
c.
Do not add the fuel near an open flame, welding arc or when the
engine is running. Stop the engine and, if possible, allow it to
cool when refuelling to prevent spilled fuel from vaporizing on
contact with hot engine parts and igniting. Do not spill fuel
when filling tank. If fuel is spilled, wipe it up and do not start
engine until fumes have been eliminated.
d.
In some cases it may be necessary to remove safety guards to
perform required maintenance. Remove guards only when nec-
essary and replace them when the maintenance requiring their
removal is complete. Always use the greatest care when working
near moving parts.
e.
Do not put your hands near the engine fan. Do not attempt to
override the governor or idler by pushing on the throttle control
rods while the engine is running.
f.
To prevent accidentally starting gasoline engines while turning
the engine or welding generator during maintenance work, dis-
connect the spark plug wires, distributor cap or magneto wire as
appropriate.
g.
To avoid scalding, do not remove the radiator pressure cap when
the engine is hot.
For more detailed information it is strongly recommended that you
purchase a copy of "Safety in Welding & Cutting - ANSI Standard
249.1" from the American Welding Society, P.O. Box 351040 Miami,
Florida 33135.