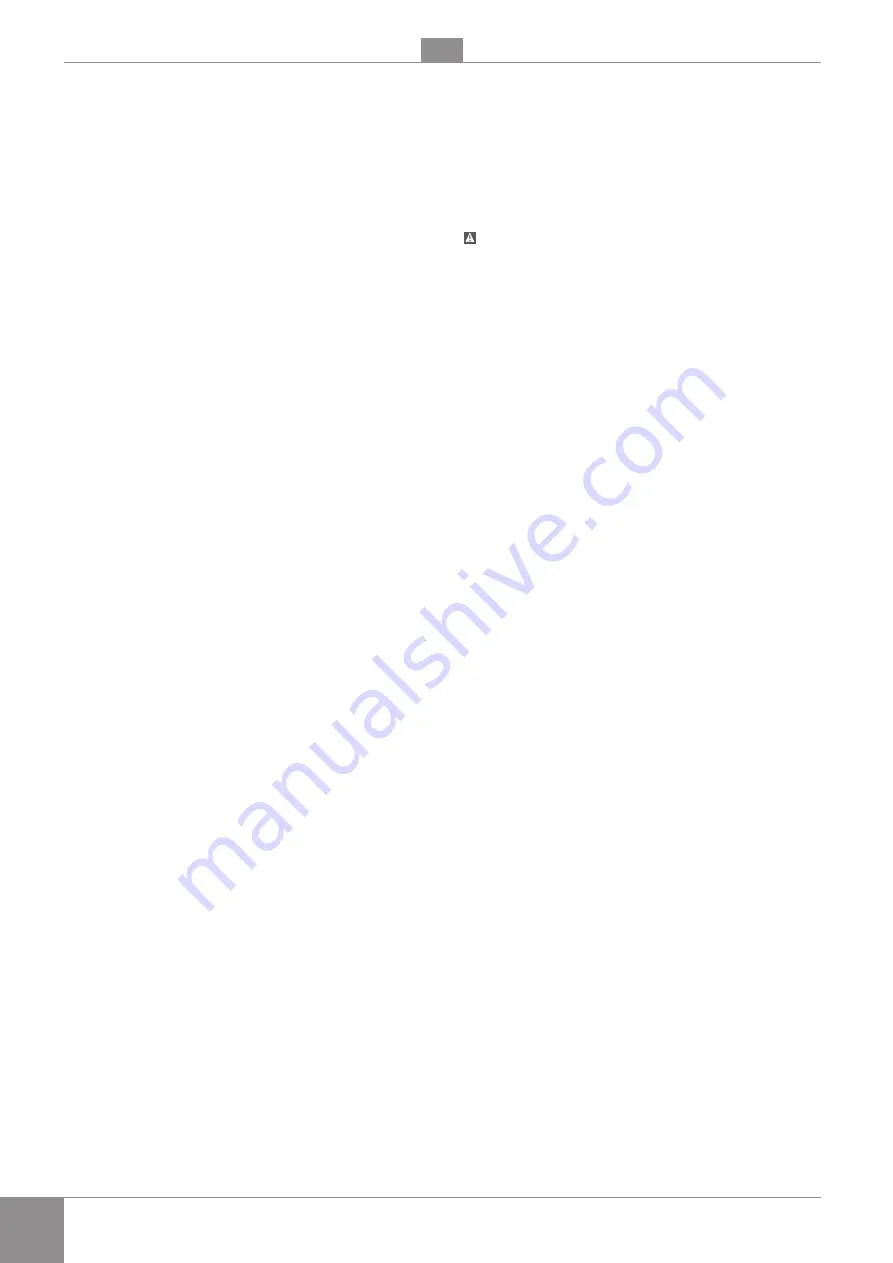
EN
48
The low temperature (5 °C antifreeze signalled on the display
by the Lo prompt) and high temperature (80° hi on the display)
alarms are managed by means of the temperature sensor T2 po-
sitioned at the plate heat exchanger outlet and the hot water
tank sensor T3. The low temperature alarm is monitored also
when the controller is in standby, and triggers the oFF and ALo
prompts alternatively and the starting of the circulation pump
P1.
The alarm is reset when the water temperature goes up again to
above the 5°C + hysteresis threshold.
Alarm PdC appears on the display in case of malfunctioning of
the external condenser (see paragraph 3.10).
If the anti-Legionella cycle ends because the timeout has ex-
pired, only the LEG prompt is displayed.
If the CAL function, specially designed for connecting a boiler
as auxiliary heating, is activate, the device switches to standby
(prompt “CAL” will appear on the display) and only the three-way
valve output will be activated. This is managed according to the
reading of sensor T3, the state of input DI3 TA and the reading
of T1.
Indications E1, E2, E3 and E4 may appear in case of failure or in-
correct measurement of the three temperature sensors.
If a power blackout occurs during operation of the unit, the
unit will restart after a few minutes maintaining the same set-
tings made before the current was interrupted.
Summary of Contents for PDC FLOOR 12T
Page 2: ......
Page 58: ...IT 58 4 7 Esempi Schemi Idraulici ...
Page 59: ...IT 59 ...
Page 60: ......
Page 61: ......
Page 62: ......
Page 63: ......