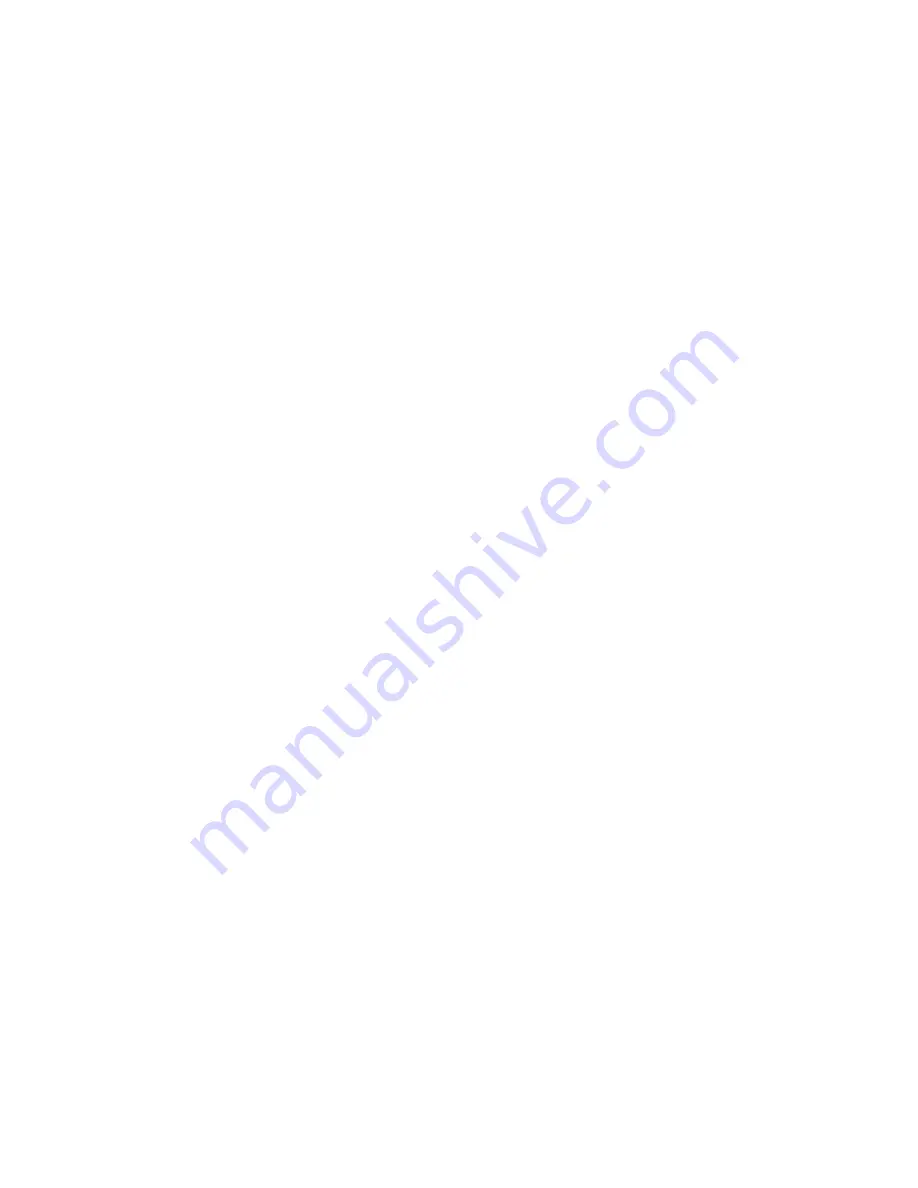
SPECTRUM INSTALLATION AND OPERATING INSTRUCTIONS
Page 13
Variable Water Flows
Figure 5 shows a typical primary/secondary piping
system. A dedicated pump is used to maintain a
constant water flow through the boiler. This secondary
pump is sized to overcome the head loss of the boiler
and secondary piping system while supplying the flow
rate required to maintain the desired temperature rise
across the boiler. The primary pump is sized to provide
the required flow to the heating system. The secondary
piping connections to the primary system piping must
not be more than
12 in
,
305 mm apart to ensure zero
pressure drop in the primary system, see Figure 5.
Low Return Water Temperatures
To prevent the problems associated with condensation
of the products of combustion due to low return water
temperatures a primary/secondary piping system with
a bypass and bypass valve must be installed, see Figure
6. The bypass and bypass valve must be sized the same
as the secondary piping. A balancing valve must also
be installed in the supply side of the secondary piping
downstream of the bypass. The balancing valve should
be adjusted to divert some of the heated discharge
water into the return water until the required inlet water
temperature is achieved. The primary and secondary
pumps should be sized to provide the required flow
through each system. The secondary piping connections
to the primary system piping must not be more than
12
in
,
305 mm apart to ensure zero pressure drop in the
primary system, see Figure 6.
Multiple Boiler Systems
Systems using multiple boilers can also be installed
using a primary/secondary manifold system, Figure 7.
Piping For Use With Cooling Units
The boiler, when used in connection with a refrigeration
system, must be installed so the chilled medium is piped
in parallel with the boiler. Appropriate valves must be
used to prevent the chilled water from entering the
boiler.
When a boiler is connected to a heating coil that may
be exposed to refrigerated air from an air handling
device, the piping system must be equipped with flow-
control valves or some other automatic means of
preventing gravity circulation of the boiler water during
the cooling cycle.
DOMESTIC WATER SUPPLY PIPING
CAUTION: Proper controls must be used to prevent
water supplied for domestic use from exceeding
130
°
F,
54
°
C
or a scald injury will occur! When higher
water temperatures are required for appliances such
as a dishwasher, a mixing valve or some other
tempering means must be installed. Households with
small children may require water temperatures less
than 120
°
F,
49
°
C
. Local codes must be complied with!
General Piping Requirements
Ensure that the water heater is equipped with bronze
headers. Piping and components connected to the water
heater must be suitable for use with potable water. The
water heater must not be connected to any heating
system piping or components previously used with a
non-potable water heating appliance. No toxic
chemicals, such as those used for boiler treatment, are
to be introduced into any potable water used for space
heating. If a hot water storage tank is used in the
system, it must be equipped with a temperature and
pressure relief valve that complies with ANSI Z21.22 or
CAN-4.4 and CAN-4.6.
NOTE: The storage tank must be located as close
to the water heater as possible to prevent excessive
head loss which will reduce flow.
Water Chemistry
The required temperature rise across the water heater
is based on water having a hardness between 5 and
25 grains per gallon with a level of dissolved solids not
exceeding 350 ppm. Water having a hardness less than
5 grains can cause excessive corrosion of the heat
exchanger. Water that has a hardness greater than 25
grains per gallon and/or a level of dissolved solids
exceeding 350 ppm will require a recalculation of the
pump size and temperature rise.
A cupro-nickel heat exchanger may also be required.
The manufacturer should be consulted when these
water conditions are encountered. See Table 7A.