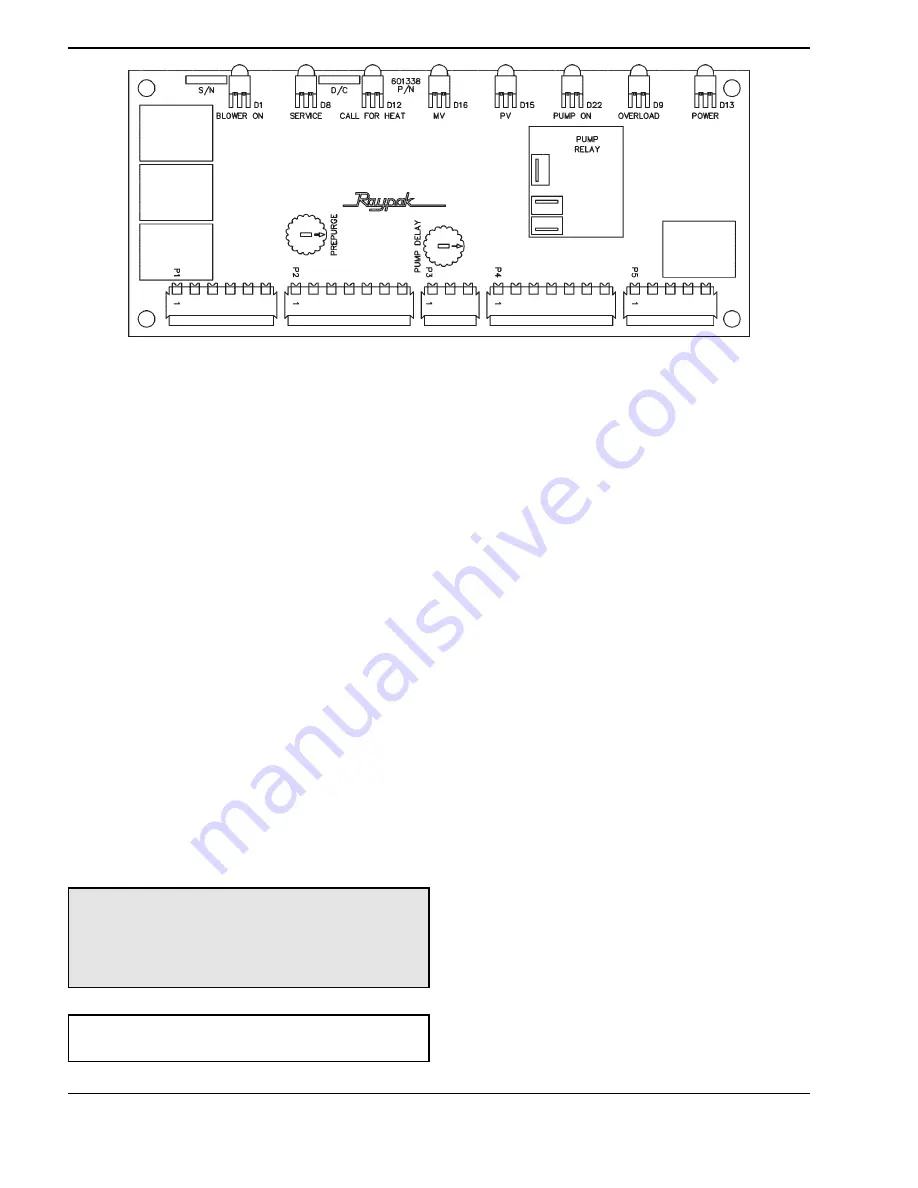
42
Fig. 30: CPW Board
Pump Turn-off Delay
The CPW board has a built-in pump driver with pump
turn-off delay, which allows the operator to set how
long the pump will run after the boiler shuts off. The
delay is factory-set for 7 minutes but can be field-
adjusted from 3 minutes to 10 minutes. The pump
relay can directly power a pump of up to 12.0 amps
draw or 3/4 hp capacity. Pumps with larger amp draws
should be energized through a pump contactor that is
controlled by the CPW board.
By properly setting the pump turn-off delay, the boiler
pump will continue running for a limited period of time
in order to extract any residual heat from the combus-
tion chamber. The pump will then shut off to conserve
energy until the next call for heat.
The pump-off time delay should be set to the minimum
time required to extract all residual heat from the heat
exchanger. If temperature as monitored at the boiler
outlet increases more than 5°F after the pump turns off
following a firing cycle, the pump-off time delay should
be extended by thirty seconds. Increase or decrease
time delay as appropriate until outlet temperature does
not spike more than 5°F after pump shut-off following
a prolonged firing cycle (> 5min.)
Blower Fan Pre-purge
The CPW board has a built-in pre-purge delay which
operates the blower fan for a user-adjustable time
period prior to pilot trial for ignition. The pre-purge peri-
od ensures that the combustion chamber is clear of all
excess combustible gases prior to commencing the
pilot ignition cycle. The pre-purge delay is factory set
for 45 seconds and it can be adjusted in the field from
45 seconds to 120 seconds. To optimize boiler
response time on call-for-heat, set the pre-purge delay
to the minimum allowed by local, state or national
code.
Blower Fan Post-purge
The CPW board has a built-in post-purge delay to
exhaust residual combustion products after the main
gas valve closes. The post-purge timing is factory set
at 3 minutes and is not field-adjustable.
Freeze Protection Feature
The CPW board is programmed to turn-off the blower
in case there is a lock-out condition. If there is a call for
heat signal, and the pilot valve signal is removed and
not reactivated within a pre-set time for any reason,
the CPW board will turn off the blower to prevent blow-
ing cold air continuously and freezing the heat
exchanger. The blower drives will open and the system
will lock in the off state.
To restart the system, primary power or the thermostat
signal must be turned off and back on. The pre-set
freeze protection feature time is approximately 5 min-
utes.
CAUTION:
The boiler requires forced water
circulation when the burner is operating and the
pump must be interlocked with the boiler. See the
Water Piping section for minimum and maximum
water flow rates and pump selection.
NOTE:
Pump will come on when power is first
applied to the boiler.
Summary of Contents for 751
Page 2: ...2...
Page 6: ...6 Component Locations Fig 1 Component Locations...
Page 15: ...15 Fig 6 Dual Boiler Piping Fig 7 Dual Boiler Piping with CHX...
Page 20: ...20 Fig 13 Single Boiler Pool Application Fig 14 Single Boiler Pool Application with CHX...