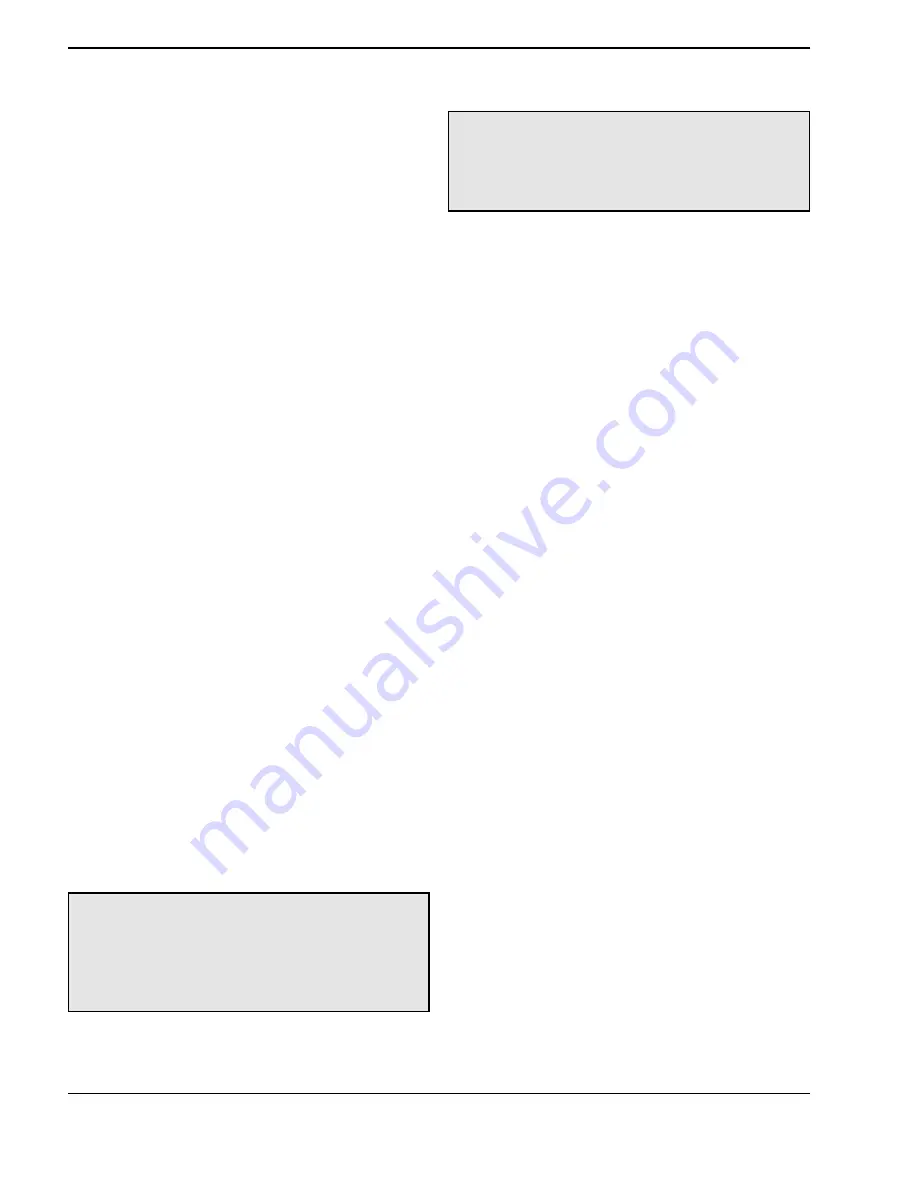
of 1 million BTUH. This opening(s) shall be either
located at or ducted to a point neither more than
18 inches (450 mm) nor less than 6 inches (150
mm) above the floor level. The duct can also
"Goose Neck" through the roof. The duct is pre-
ferred straight down 18 inches from floor, but do
not place near piping. This air supply opening
requirement shall be in addition to the air opening
for ventilation air required in (1).
3. When air supply is provided by natural air flow
from outdoors for a power burner and there is no
draft regulator, draft hood or similar flue gas dilu-
tion device installed in the same space, in addition
to the opening for ventilation air required in (1),
there shall be a permanent air supply opening(s)
having a total cross-sectional area of not less than
1 sq. in. for each 30,000 BTUH (70 sq. mm per
kW) of total rated input of the burner(s), and the
location of the opening(s) shall not interfere with
the intended purpose of the opening(s) for ventila-
tion air referred to (1). This opening(s) can be
ducted to a point neither more than 18 inches (450
mm) nor less than 6 inches (150 mm) above the
floor level. The duct can also "Goose Neck"
through the roof. The duct is preferred to be
straight down 18 inches from floor, but do not
place near piping.
4. Refer to the latest version of CSA B149 for addi-
tional information.
WATER PIPING
General
The boiler should be located so that any water leaks
will not cause damage to the adjacent area or struc-
tures.
All units should be plumbed in accordance with the
appropriate diagram from the following sections or per
a suitable engineered piping arrangement.
12
Relief Valve Piping
Hydrostatic Test
Unlike many other types of boilers, Raypak boilers do
not require hydrostatic testing prior to being placed in
operation. The heat exchanger has already been fac-
tory-tested and is rated for 160 PSI operating
pressure. However, Raypak does recommend hydro-
statically testing the piping connections to the boiler
and the rest of the system prior to operation. This is
particularly true for hydronic systems using expensive
glycol-based antifreeze. Raypak recommends con-
ducting the hydrostatic test before connecting gas
piping or electrical supply.
Leaks must be repaired at once to prevent damage to
the boiler. NEVER use petroleum-based stop-leak
compounds.
1. Connect fill water supply. Fill boiler with water (be
sure bleed valve is open). When water flows from
bleed valve, shut off water. Close bleed valve.
Carefully fill the rest of the system, being sure to
eliminate any entrapped air by using high point
vents. Close feed valve. TEST AT standard oper-
ating pressure for at least 24 hours.
2. Make sure constant gauge pressure has been
maintained throughout test.
3. Check for leaks. Repair if found.
Low Temperature System
Boiler requires minimum inlet temperature of 105°F.
Consult the following sections for piping details. (For
Pool temperature requirements, See the Pool Heating
Section).
Temperature & Pressure
Gauge
The temperature and pressure gauge is factory-
mounted in the inlet/outlet header.
WARNING:
Pressure relief valve discharge piping
must be piped near the floor close to a floor drain to
eliminate the potential of severe burns. Do not pipe
to any area where freezing could occur. Refer to
local codes.
CAUTION:
This boiler requires forced water
circulation when the burner is operating. See Table E
for minimum and maximum flow rates and water
pump selection. The pump must be interlocked with
the boiler to prevent boiler operation without water
circulation.
Summary of Contents for 751
Page 2: ...2...
Page 6: ...6 Component Locations Fig 1 Component Locations...
Page 15: ...15 Fig 6 Dual Boiler Piping Fig 7 Dual Boiler Piping with CHX...
Page 20: ...20 Fig 13 Single Boiler Pool Application Fig 14 Single Boiler Pool Application with CHX...