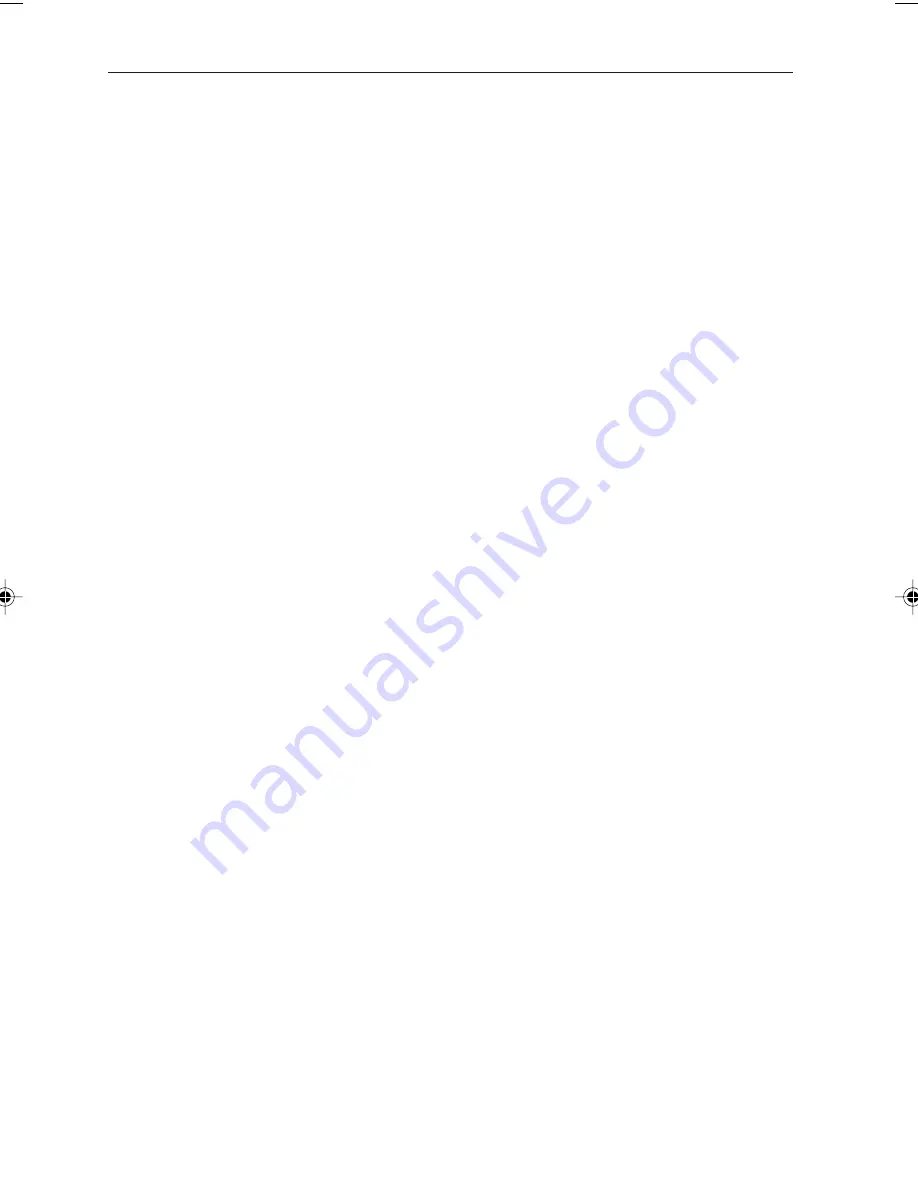
ST600R Autopilot Control Unit
iv
Safety Information
Passage making under autopilot control is an enjoyable experience
that can, if you are not careful, lead to the relaxation of the
permanent watch. A permanent watch MUST be maintained no
matter how clear the sea may appear to be.
Remember, a large ship can travel two miles in five minutes – just
the time it takes to make a cup of coffee.
The following rules should always be observed:
• Maintain a permanent watch and regularly check all around for
other vessels and obstacles to navigation – no matter how clear the
sea may appear a dangerous situation can develop rapidly.
• Maintain an accurate record of the vessel’s position either by use of
a radio navigation receiver or visual bearings.
• Maintain a continuous plot of position on a current chart. Ensure the
locked autopilot heading steers you clear of all obstacles. Make
proper allowance for Tidal Set – the autopilot cannot!
• Even when your autopilot is locked onto the desired Track using a
radio navigation receiver, always maintain a log and make regular
positional plots. Radio navigation signals can produce significant
errors under some circumstances and the autopilot cannot detect this
situation.
• Make sure that all members of crew are familiar with the procedures
to disengage the autopilot.
Your
Raymarine
autopilot will add a new dimension to your boating
enjoyment. However, it is the responsibility of the skipper to ensure
the safety of the vessel at all times by careful observance of these
basic rules.
EMC Conformance
All
Raymarine
equipment and accessories are designed to the best
industry standards for use in the leisure marine environment.
Their design and manufacture conforms to the appropriate
Electromagnetic Compatibility (EMC) standards, but good
installation is required to ensure that performance is not
compromised.
Summary of Contents for ST600R
Page 2: ...ST600R Autopilot Control Unit Owner s Handbook Document number 81134 3 Date May 2001 ...
Page 3: ......
Page 5: ...ST600RAutopilotControlUnit ii ...
Page 24: ...13 Chapter2 BasicOperation SeaTalk Data Chart ...
Page 41: ...30 ST600RAutopilot ControlUnit ...