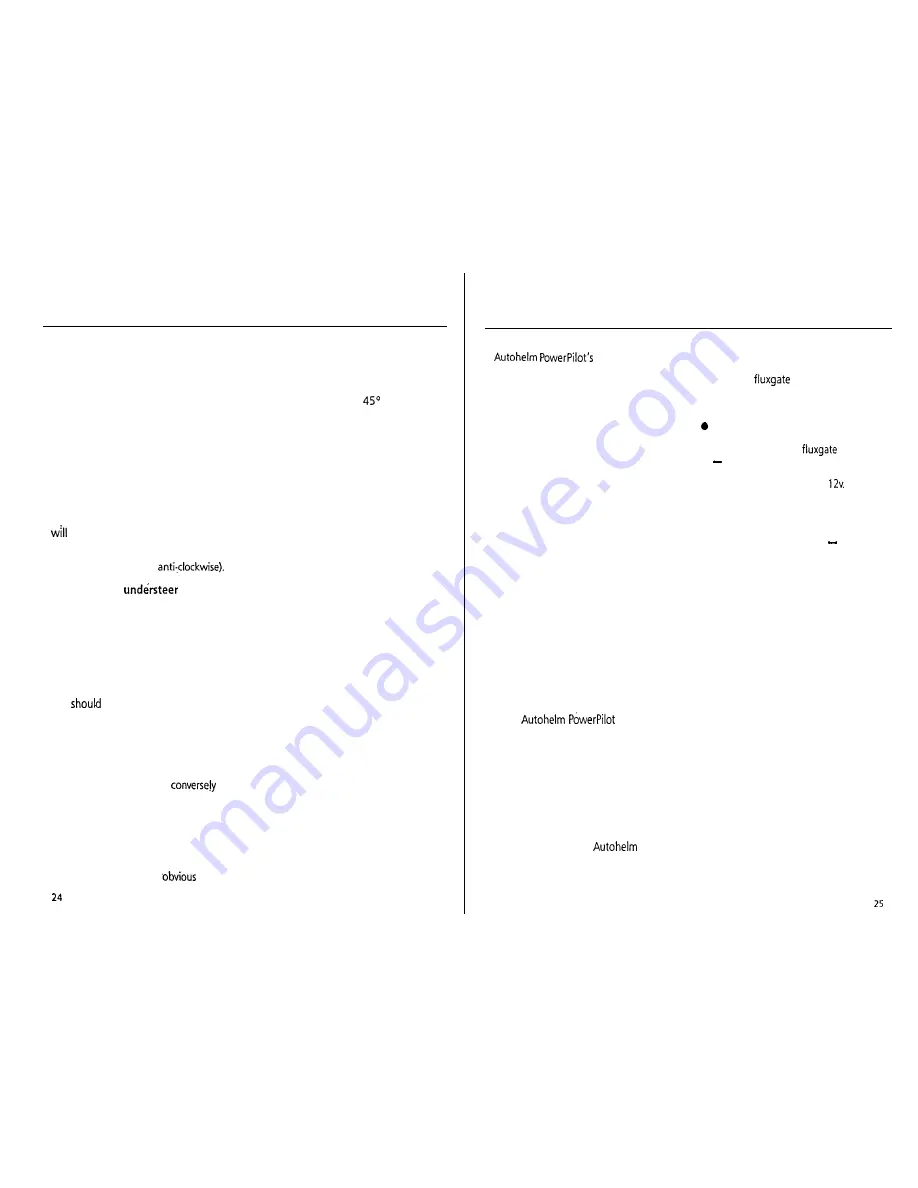
4.2 RUDDER CONTROL
ADJUSTMENT
The rudder control setting recommended
on page 22 will provide
stable
control for
initial sea trials. However, power craft can
vary widely in their response to the helm
and further adjustment of the rudder
control setting may improve the
Autohelm’s steering characteristics.
An excessively high rudder control
setting results in
oversteer
which can be
recognised by the vessel swinging from
side to side of the automatic heading
accompanied by excessive rudder
movement. In addition, distinct overshoot
be observed when the course is
changed. This condition can be corrected
by reducing the rudder control setting
(rotating rudder control
Similarly, an insufficient rudder control
setting results in
which gives
sluggish steering performance and is
particularly apparent when’changing
course. This is corrected by increasing the
rudder control setting (rotating rudder
control clockwise). These tendencies are
most easily recognised in calm sea
conditions where wave action does not
mask basic steering performance. The
rudder control setting is not over critical
and
be set to the lowest setting
consistent with accurate course keeping.
This will minimise actuator movements
and hence reduce power consumption.
It may be noticed that the autopilot
tends to be a little less stable on northerly
headings in the higher latitudes of the
northern hemisphere (and
southerly headings in the southern
hemisphere). This is caused by the
increasing angle of dip of the earth’s
magnetic field at higher latitudes which
has the effect of amplifying rudder
response on northerly. headings. The
tendency towards northerly heading
instability is usually more
in
higher speed craft and when it occurs can
be corrected by reducing the rudder
control setting. In excess of 30 knots, a
reduction by at least two positions can
often be required within
of North.
Planing Craft
On
fast planing craft which operate over a
wide speed range, the rudder control
setting often requires reduction at higher
speeds where steering effectiveness is
increased. Oversteer can be extremely
violent at planing speeds and it is
recommended that the rudder control
setting is reduced before opening the
throttle.
5. OPERATING HINTS
central course
computer continuously optimises
automatic steering performance
eliminating the need for operator
supervision.
It is, however, very important to
understand the effect of sudden trim
changes on steering performance.
At planing speeds, where only a small
proportion of the hull is in contact with
the water, variations in wind speed and
direction can produce significant changes
in trim. Similarly, variations in vessel
attitude and engine settings also produce
trim changes. When a change in trim
occurs the automatic trim compensation
system requires at least 120 seconds to
apply the necessary rudder off-set to
restore the automatic heading. In gusting
conditions, therefore, particularly when
the wind is forward of the beam, the
course may tend to wander slightly.
Passage making under automatic pilot
is a very pleasant experience which can
lead to the temptation of relaxing
permanent watch. This must always be
avoided no matter how clear the sea may
appear to be.
5.1 UNSATISFACTORY STEERING
PERFORMANCE
If the
has been
correctly specified, installed in accordance
with the instructions and adjusted
correctly it will provide outstandingly
good steering precision over a very wide
range of wind and sea conditions.
If the performance falls below your
expectations and the pilot appears to be
working correctly the fault will normally
be found by carrying out the simple
checks outlined below. Before reporting
your difficulties to an
specialist,
please check the following:-
* Have the test procedures and
adjustments detailed in Section 3.3
been carried out correctly? Check
again.
l
Has the
compass been
installed in an area free from large
magnetic deviation? If in doubt use a
hand bearing compass to check.
If performance has changed recently
has a magnetic influence been
introduced near the
compass?
anchor/chain/radio equipment/
loudspeaker/tools/AC. generator, etc.
l
Is battery voltage correct?
l
Are fuses intact and of correct rating?
l
Are circuit breakers engaged?
l
Is wiring of correct diameter and are
screw connectors firmly tight?
l
If pilot fails to hold course
check
rudder setting at control units.
If vessel wanders under pilot control
l
Verity that hydraulic pump is correct for
size and type of vessel.
l
Check steering ram and actuator are of
compatible type and bleed system to
remove air.
l
Check rudder reference transducer
linkages for security and correct
alignment.